Meet Sofia Dias: Food Safety and Quality Manager for Marley Spoon Australia
iAuditor by SafetyCulture Tips | SafetyCulture Champions | Tips & Tricks | By | 21 Jul 2019 | 5 minute read
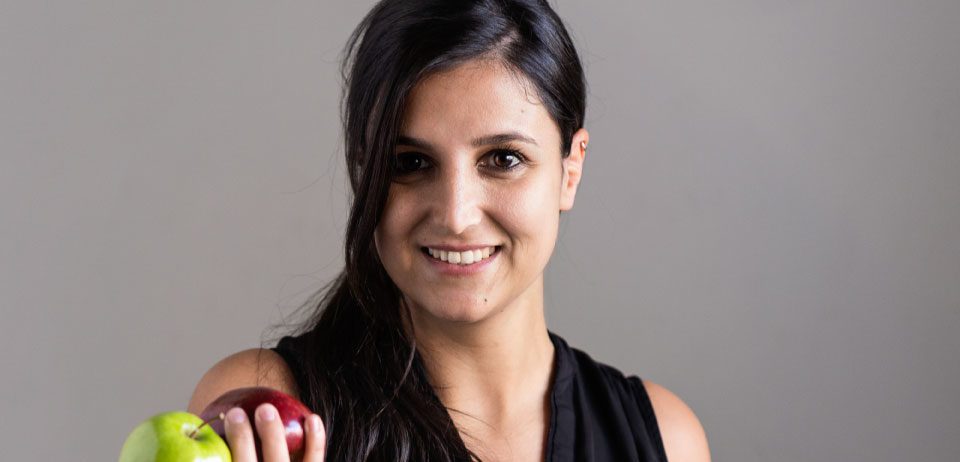
Sofia Dias is Australia’s Food Safety & Quality Assurance (FSQA) Manager for Marley Spoon — a meal kit service delivering thousands of fresh, delicious, ready-to-cook meals to homes every week. Sofia is responsible for ensuring food safety and quality assurance across all of the company’s operations, including supplier onboarding, product onboarding, quality and safety audits and overall FSQA management.
What do you enjoy most about your job?
I’m a data geek. I just love data. And when it comes to quality, it’s all about the data. Being responsible for executing and improving Marley Spoon’s hazard analysis and critical control points (HACCP) plan gives me the opportunity to help transform the company into one that’s data-driven. I love having data at my fingertips and knowing I can trust it. It doesn’t matter whether you’re the CEO or some other C-Level executive. You may have an opinion, but if you don’t have the data to back it up, your opinion means nothing. In my world, data rules.
As an FSQA professional, what are you most proud of?
In the food industry, we’re supplying food to single people, families, pregnant mothers, elderly folk, and at-risk individuals all over Australia. If we don’t monitor and enforce food safety and quality standards, it could mean the difference between life and death. I’m part of a team that is doing a better job of protecting our customers because we’re using industry-leading tools to capture and analyze the data we need to reduce the risk for both our customers and the company.
When did you first come across iAuditor?
When I first moved to Australia from Berlin, Marley Spoon was already using iAuditor, but only at a very basic level. To be honest, it really wasn’t exciting. My attitude was: “We can either use it or lose it.” It didn’t bother me either way.
I just wanted to do my job. But when I saw the potential of iAuditor, I was impressed: “Wow. There’s something special here that we can actually use. We can develop this into a valuable tool for the startup business.”
What was the key moment when you really bought into iAuditor?
It’s nice to have a tool that tells you when you’re doing great, but it’s even better when it tells you when you’re not because then you can fix it. I remember calling the SafetyCulture Account Manager and telling them that the software wasn’t meeting our needs. I couldn’t see which items were failing. That bothered me. The Account Manager told me that the data was there, I just needed to set things up properly. Once I did that, I was utterly blown away! I could actually see every little thing I needed to pay attention to that required improvement. To have everything so clear — so in your face — was a great moment.
How does iAuditor help you do your job better?
Many people use Google Sheets or Microsoft Excel for quality and safety. They work well when you’re a small startup. But when you’ve got five people on the shop floor messing with one spreadsheet and they’re under pressure, it’s easy for mistakes to be made. When you take those results and start asking questions, people often can’t remember what happened. Since nothing is tracked, you begin to question the quality of the data. We can’t afford that.
People depend on us. If they open their meal bag and an ingredient is missing — or it’s the wrong one — they can’t cook their meal. iAuditor has changed all of that. Everything is added directly into the system. I can drill down into any station at any site and know exactly what happened. While our on-site error rates are generally around 5%, That means we’re catching over 90% of the mistakes before those meal kits leave our facility. That’s huge! And it’s all because of iAuditor.
What impact has using iAuditor had on your job
I can’t really begin to explain how much easier it’s made my job. I now have visibility into every corner of the business.
- I know which suppliers are living up to their quality commitments
- How we’re sticking to our safety obligations
- Which picking lines are working well and which ones need help
- What issues need to be addressed, and
- Whether I’m understaffed or overstaffed
I just open the software and drill down. But it’s not just the ease of use that’s made a difference. I now have confidence in the data. I trust it. That allows me to go home each evening and have a good night’s sleep.
What role has iAuditor played in your company’s digital transformation?
It’s had an enormous impact, not just on my job, but on the whole company. Because people now have access to insights that weren’t previously available, they’re doing a better job. I think the biggest strength of iAuditor is the data. It allows us to see trends developing over time. We can just navigate through the different periods, drill down on failed items, drill down on the questions we want answers to, and share templates across all of our sites for consistent quality and safety. It’s saved the company a lot of time and money.
How has iAuditor saved you money?
Depending on production schedules, we might have anything between AU$200,000 to $300,000 of produce in our cold rooms. According to Australian law and food safety best practices — they can’t go above five degrees celsius. If the temperature exceeds that for more than two hours, we have to throw it way. I received an SMS alert late one Saturday night saying that the temperature in our cold storage was rising, putting thousands of dollars in stock at risk. Our wireless SafetyCulture Temperature Sensors had detected the change. I immediately checked the data in iAuditor, and sure enough, the temperature in the cold room had increased. Someone was sent to fix the problem right away. Fortunately, it turned out that someone had just left the door open. If we had only found out about it when we arrived on Monday, we would have had to throw out everything in the cold room. That one little message saved us tens of thousands of dollars.
How do you feel about being about an iAuditor Champion?
I feel it’s a real privilege to be a champion of something I believe in. iAuditor has made my job easier. It’s saved the company a lot of money, whether it’s in resources, paper or time. It’s allowed us to have a fully digital, paperless HACCP plan which means we can track every step of every process across our production lines to mitigate chemical, microbiological, or physical risks. I’ve helped to develop something that makes a difference. I’m proud of it. Why wouldn’t I want to be a champion?
How do you see iAuditor helping you in the future?
I’m looking forward to seeing how iAuditor evolves to address some of the issues that are coming to the forefront. Traceability’s something that is going to be talked about a lot in the future. It’s not just about food safety — it’s about food security. Where is my food coming from? Is it actually coming from where I think it is? People are going to want to know that. It’s exciting to work with the SafetyCulture team to develop new features that can make a real difference to both our company and the industry.
Important Notice
The information contained in this article is general in nature and you should consider whether the information is appropriate to your specific needs. Legal and other matters referred to in this article are based on our interpretation of laws existing at the time and should not be relied on in place of professional advice. We are not responsible for the content of any site owned by a third party that may be linked to this article. SafetyCulture disclaims all liability (except for any liability which by law cannot be excluded) for any error, inaccuracy, or omission from the information contained in this article, any site linked to this article, and any loss or damage suffered by any person directly or indirectly through relying on this information.