Crowdsourcing Workplace Safety: OSHA’s Recordkeeping Rules
Industry Trends | By | 20 Jan 2017 | 4 minute read
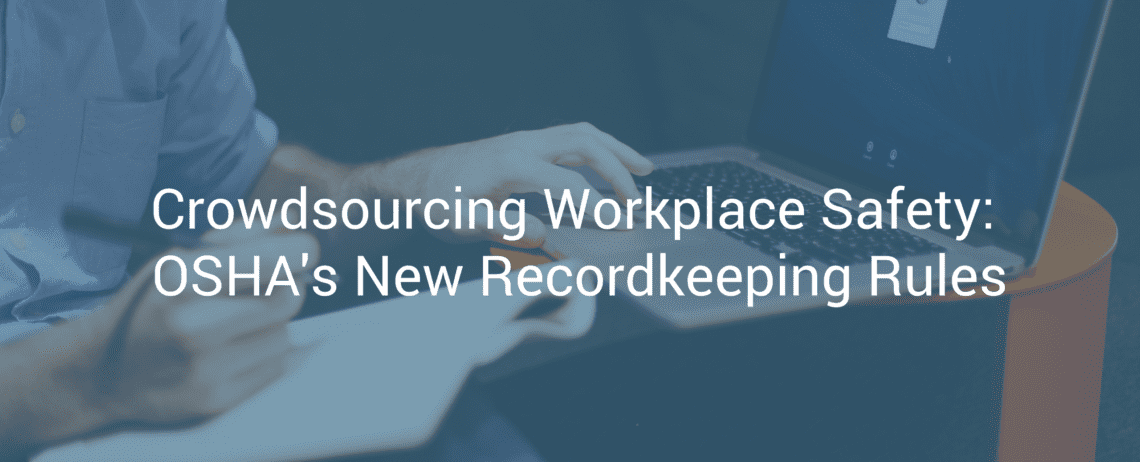
Employers have been hearing about OSHA’s new recordkeeping rules for a while now. How will impact your business and what will it change in the data submission process?
The body of data that OSHA collects on injuries and illnesses are the primary statistical source used to shape future programs, understand what’s happening in each industry, and identify where risks exist. There was a major update to recordkeeping rules in 2016, the rest of which come into effect in 2017. Arguably the biggest change centers around submission of illness and injury data. Establishments now need to submit that data electronically through the OSHA site. The goal is to open up the most current data to employers so they can see where they need to focus their efforts.
For companies that are at the forefront of tracking safety, new recordkeeping regulations won’t impact existing business processes much. The biggest change will be for companies who are lagging in technological implementation. They may have their data in paper forms or in many different places. Submitting information online is very quick; OSHA estimates each form will only take about 10 minutes to complete. The time consuming part of this submission is collecting and digitizing the data.
The Logistical Stuff – Company Sizes, Dates and Forms
Each establishment with 250+ employees must submit their 2016 injury and illness records in Form 300A by July 1, 2017. In 2018, employers are required to submit all 2017 forms (300A, 300 and 301) by July 1, 2018. Each year after that, this information will need to be submitted electronically by March 2nd. Businesses with 20-249 employees in “high-risk industries” must submit their 300A forms by July 1 in 2017 and 2018, and by March 2 each year after that.
Modernization of data collection
These new regulations will provide much faster insight into data within each specific industry and in some cases, with a specific establishment attached. Previously, we received more generic data sets that depicted injury information from 3 years ago. Without current data, it’s much harder to make educated decisions about how to move forward. The new regulations will provide the opportunity for nearly immediate access to information. OSHA believes it will encourage employers to share what’s working well and where safety procedures could use improvement. Breaking down information silos at a national level benefits workplace safety as a whole. We saw a similar effect on a much smaller scale when SafetyCulture spoke with E Light Electric on the improvements they saw with enhanced communication across different departments.
Dr. David Michaels, Assistant Secretary of Labor for Occupational Safety and Health, says “Our new rule will ‘nudge’ employers to prevent work injuries to show investors, job seekers, customers and the public they operate safe and well-managed facilities. Access to injury data will also help OSHA better target compliance assistance and enforcement resources, and enable big data researchers to apply their skills to making workplaces safer.” OSHA has said that some of the information will be available through their site as well. Electronic reporting and the subsequent sharing of that information forces a form of transparency between companies and their stakeholders in terms of their safety. This means that workplace safety can become an even bigger differentiator for companies in terms of attracting employees and attracting investors or business partners.
The submittal process will be straightforward
Employers can submit information in three ways: direct data entry in an electronic form, file upload in the form of a CSV or an API integration. The electronic form will be of most use to companies that have their information on paper forms. This method requires less time upfront, as it doesn’t require any new technological systems. However, this method will also take the longest amount of time for actual data submission. The second method, a CSV upload, will work for organizations tracking injury data in Excel. Many programs also export to a CSV so this will likely be the most popular option for businesses. The third option requires more upfront investment in a tech integration, but for larger companies will save time and money later down the line as they can simply use their existing reporting systems and have injury data reported automatically to OSHA.
But we know the issue with data submission is in tracking down the right reports
As stated above, OSHA estimates each form to only take about 10 minutes. However, his estimate doesn’t take into account how long it takes to get info together. Many organizations are still struggling with a streamlined system to track all their injury data. If information is stored in paper forms, those can be lost or damaged over time, or take quite a lot of time to hunt down. Particularly for small to medium sized businesses who do not have a dedicated employee health and safety advocate, it may be harder to keep all this information organized.
The new mandates also include freedom from retaliation and reasonable and non-discouraging reporting features. OSHA can cite an employer for taking adverse action even if the employee did not file a complaint. Reports must be submitted to supervisors without an unreasonable strain on the employee so as not to discourage reporting. This part of the recording mandate has already been in effect since December of 2016.
What does this mean for you, the employer?
The good news is, businesses do not need to collect any new data. If you’re already tracking workplace injuries in an efficient and organized manner, the electronic submission will require very little of your time. It also means a lot of information will be publicly available, but without any personally identifiable information. Interested parties will be able to search for and download information very quickly on a particular industry. Posting establishment-specific data will provide valuable information to employers and to researchers. OSHA can efficiently use their resources to identify problem areas and enhance workplace safety for each employee.
Important Notice
The information contained in this article is general in nature and you should consider whether the information is appropriate to your specific needs. Legal and other matters referred to in this article are based on our interpretation of laws existing at the time and should not be relied on in place of professional advice. We are not responsible for the content of any site owned by a third party that may be linked to this article. SafetyCulture disclaims all liability (except for any liability which by law cannot be excluded) for any error, inaccuracy, or omission from the information contained in this article, any site linked to this article, and any loss or damage suffered by any person directly or indirectly through relying on this information.