6 Most Commonly Overlooked Workplace Safety Practices
Industry Trends | By | 27 Jan 2016 | 2 minute read
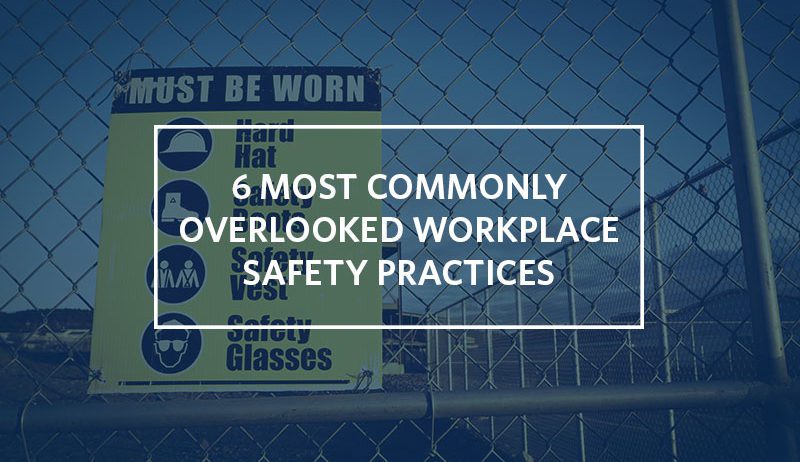
There are many practices in workplace safety that are often overlooked, undermined and neglected. Some of these practices can be fairly simple to put into action yet essential for companies that want a safety-focussed culture. We reveal six commonly undervalued yet essential workplace safety practices:
1. The Importance of Communication ā Communication is the foundation of success in safety awareness. Fluid communication practices allow for staff to convey important messages, alert others of potential hazards and establish accountability. One of the biggest causes of accidents from a broad perspective is the failure to communicate or convey the most pertinent of information.
2. The Importance of Staying Hydrated ā. A dehydrated labourer is far more likely to improperly handle any material and is less likely to be aware of their surroundings. Dehydrated workers are at a higher risk of heat stroke or to develop cardiac complications while engaged in routine labour. In addition to placing themselves at risk, these situations also place those around them at risk. Ā While performing even the most routine of tasks, it is important for any employee to take frequent breaks and half a gallon of water each day. This is even more prevalent on those long, hot summer days.
3. Donāt Overlook Teamworkā There is no āIā in team and perhaps one of the best business practices is the reinforcement of group cohesion. Teamwork enhances safety as there is always said to be strength in numbers. Good teamwork leads to more efficient and productive operations while also assuring that all performers are on the same page. As we have highlighted, miscommunication can create negative consequences, but progressive team-oriented approaches have been proven to enhance safety, improve output and boost morale.
4. The Danger of Mishandling Volatile Materials āIn many instances labourers fail to read material data sheets and appropriately handle hazardous or unsafe materials. Before handling any substance, it is paramount to don the appropriate PPE and be dressed appropriately to work with potentially volatile substances. Learning HAZMAT placard codesĀ can also serve as a great tool for any individual attempting to decipher what class of materials they are handling. Improper handling of these varied materials can result in a spill or contamination, the results of which can be exceptionally dangerous.
5. The Danger of Distractions āDistractions can easily interfere with any operation. For this reason, it is essential that employees be free of any electronic devices and assure their attention is on the task at hand at all times. For just a moment, shifting focus toward a smartphone can cause drastic consequences, it is best to keep your hands and mind free of any unnecessary items while working.
6. The Danger of Not Lifting Properly āĀ Many workplace injuries are caused by an employee failing to lift an item properly. A consensus of experts agreeĀ that it is important for any worker to lift with their legs and not their back. Yet, many workers fail to abide by this seamlessly easy principle. In addition, if an item is too cumbersome or heavy to lift on your own, never be afraid to ask for a hand. As stated, more workplace injuries are caused by improper lifting and far more dangerous to personnel than a presumed notion of weakness by failing to muscle through any task. Use proper discretion.
Words by Tom Reddon
Tom Reddon is a forklift specialist and blog manager for theĀ National Forklift Exchange. He also sits on the Material Handling Equipment Distributors Association (MHEDA) Executive Dialogue team. Follow him on Twitter atĀ @TomReddon
Important Notice
The information contained in this article is general in nature and you should consider whether the information is appropriate to your specific needs. Legal and other matters referred to in this article are based on our interpretation of laws existing at the time and should not be relied on in place of professional advice. We are not responsible for the content of any site owned by a third party that may be linked to this article. SafetyCulture disclaims all liability (except for any liability which by law cannot be excluded) for any error, inaccuracy, or omission from the information contained in this article, any site linked to this article, and any loss or damage suffered by any person directly or indirectly through relying on this information.