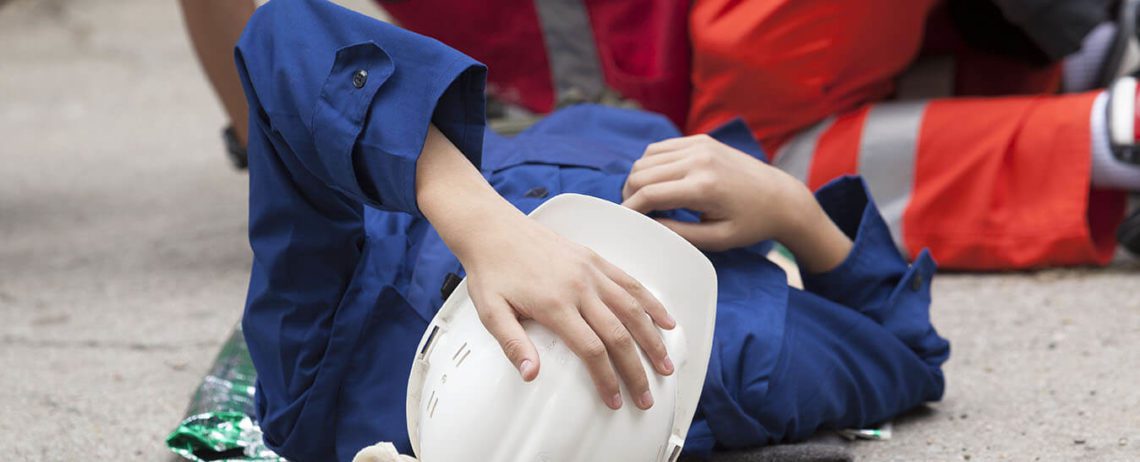
Why workplace accidents tend to happen late in a project
We all know some jobs carry a higher risk than others. Often when we start a job, task or activity we are aware and cautious of this risk. As time goes on, many of us become comfortable, with a false sense of security of the dangers associated with the task we’re undertaking.
This is how mistakes and accidents occur. This behaviour is described as “normalization.” It is why workplace accidents tend to happen later in the project, as noted by Neil Swidey, author of Trapped Under the Sea.
Neil has spent years researching workplace health and safety data. Writing in the Harvard Business Review, he reports that whether it’s a small home-improvement project or a large public infrastructure mega project, trouble typically arises late in the project timeline:
“The more people do something without suffering a bad outcome, the harder it becomes for them to remain aware of the risks associated with that behavior. The most obvious example of this in everyday life is texting while driving. Most of us have been guilty of this risky behavior, even if we don’t want to admit it. And if we’ve never suffered an accident as a result of all of furtive thumbing from behind the wheel, we might have even fooled ourselves into thinking we’re just better at it than most people. We’re not. That’s simply the seductive yet slippery power of normalization at work.”
[Tweet “Normalization: A danger to every workplace @NeilSwidey #OHS #Safety”]
Neil first noticed this behavior when compiling data for his book on commercial divers.
“Before I spent five years researching my book Trapped Under the Sea, the true story of a team of commercial divers sent on an impossible mission to rescue the multibillion-dollar cleanup of Boston Harbor, I intuitively assumed that the most dangerous time on a job was Day One. After all, that’s when workers are usually getting used to a new setting, new colleagues, and new equipment, and when the learning curve is steepest. However, after marinating in workplace safety data, I came to understand that the opposite is true.”
Moral of the story; don’t fall into the slippery power of normalization.
Everyone knows someone who has been affected by a workplace accident. So remember, it’s better to be safe than sorry.
For more detail, read Neil’s article on the Harvard Business Review, “Why Workplace Accidents Tend to Happen Late in a Project.”
Tips to stay vigilant through an entire project with iAuditor:
- Identify hazards, circumstances and conditions to look out for at the start of the project. Having a weekly checklist meeting could mitigate those risks by keep tracking of them.
- Consider a behavior observation program
- Be realistic about project milestones and completion dates set in place
- Make everyone a safety hero and give them the checklists and tools to self-assess at all stages
- Set up a reward program for employees that identify potential risks
Follow SafetyCulture on Twitter, Facebook and LinkedIn
Author – Tania Clarke
Important Notice
The information contained in this article is general in nature and you should consider whether the information is appropriate to your specific needs. Legal and other matters referred to in this article are based on our interpretation of laws existing at the time and should not be relied on in place of professional advice. We are not responsible for the content of any site owned by a third party that may be linked to this article. SafetyCulture disclaims all liability (except for any liability which by law cannot be excluded) for any error, inaccuracy, or omission from the information contained in this article, any site linked to this article, and any loss or damage suffered by any person directly or indirectly through relying on this information.