From automakers to fashion makers — how these 7 manufacturing subsectors can reopen successfully
Industry Trends | By | 16 Jun 2020 | 5 minute read
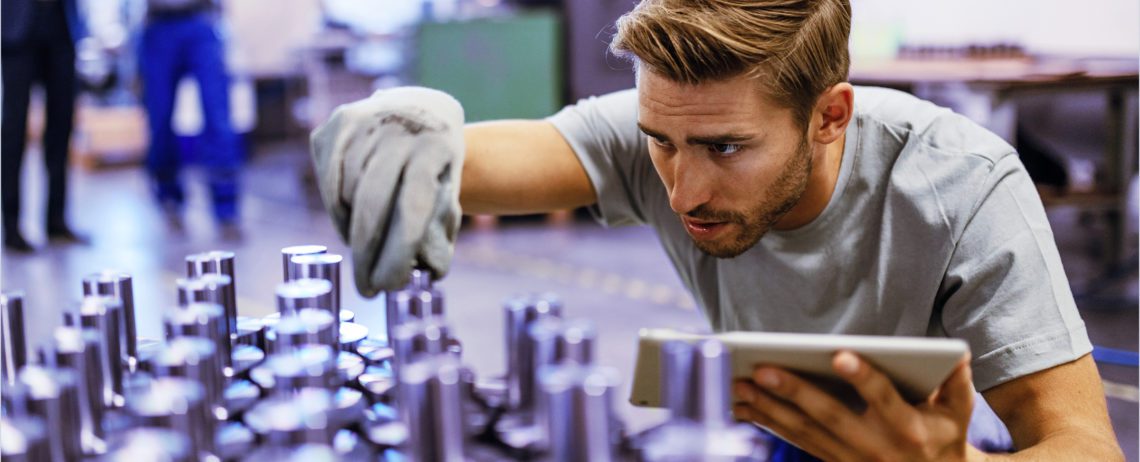
COVID-19 has had a huge impact on the manufacturing industry. And, as factories and supply chains start to open up again, manufacturing businesses will need to adapt to the new standards in hygiene, social distancing, and safety.
While other industries were able to modify their processes and implement remote working, this simply wasn’t realistic for many manufacturers. In the future, companies may oversee production remotely from their home office, and IOT may be in full swing. However, the manufacturing world and its sub subsectors simply weren’t prepared this time around. Challenges continue to abound as organizations and governments reconsider the effectiveness of globalized production and supply chains.
Now, as manufacturers consider how to get back to full production, we’ve put together a list of what sub sectors may experience as they reopen — from automakers, food and beverage manufacturers, to textiles and electronics manufacturing.
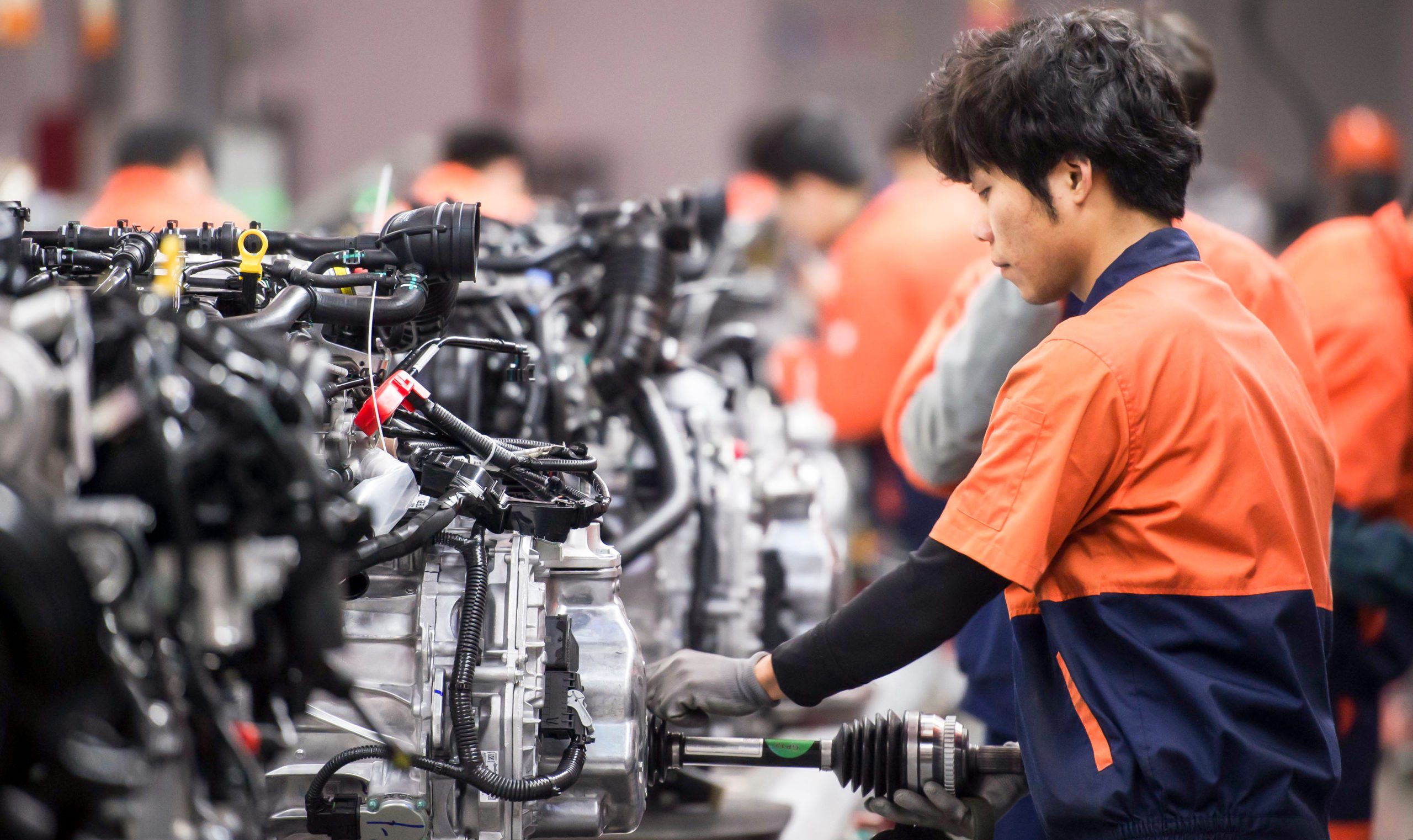
Trends in automotive manufacturing
Gradual return = safer return
The common theme across automotive manufacturers globally is a gradual transition back to full production. In the UK, Vauxhall has temporarily reduced production levels to maximize social distancing and get back to manufacturing sooner. The plan is to slowly increase the number of workers in groups of 40, ensuring safety and sustainable output. As workers return, they are greeted by extensive social distancing markers, placed two meters apart. New markers have been introduced everywhere, from red tape hanging on the factory floor to cross marked urinals in bathrooms. Vauxhall have even introduced novel measures like individual ashtrays for workers in common areas.
Logos at a distance
Global car manufacturers have become active participants in government social distancing campaigns. Some of the most recognized automotive brands have designed modified logo design to encourage continued social distancing practices. Mercedes’ iconic combined three branch logo has been replaced by separated branches. While Volkswagen group have separated the VW letters and increased padding between Audi’s recognizable quad circle logo.
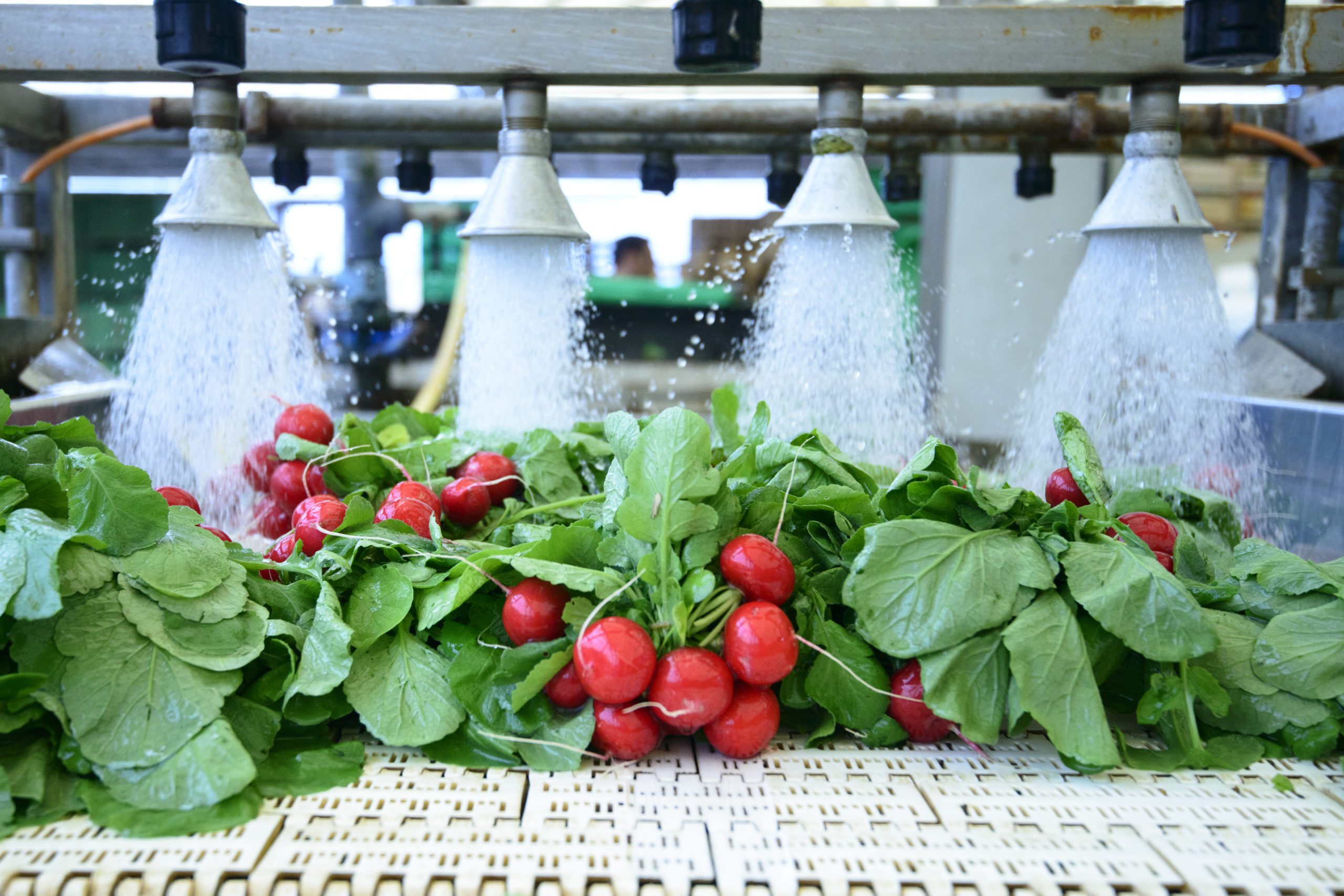
Trends in food and beverage manufacturing
Robotic collaboration
Japanese technology manufacturer Mitsubishi Electric are shaking up human-based food processing tasks one robot at a time. One of the biggest challenges facing food and beverage manufacturers is maintaining social distancing throughout human-based processing tasks. Historically, workers would complete processing tasks side-by-side with minimal distance between. Now, social distancing guidelines are disrupting existing manufacturing processes across the sector. However, Mitsubishi have developed a new collaborative robot named ‘CoBot’ just in time for reopening. CoBot is designed specifically to work in collaboration with human workers in production lines. The introduction of CoBot in factories provides the perfect social distancing spacer between employees while allowing organizations to reopen faster.
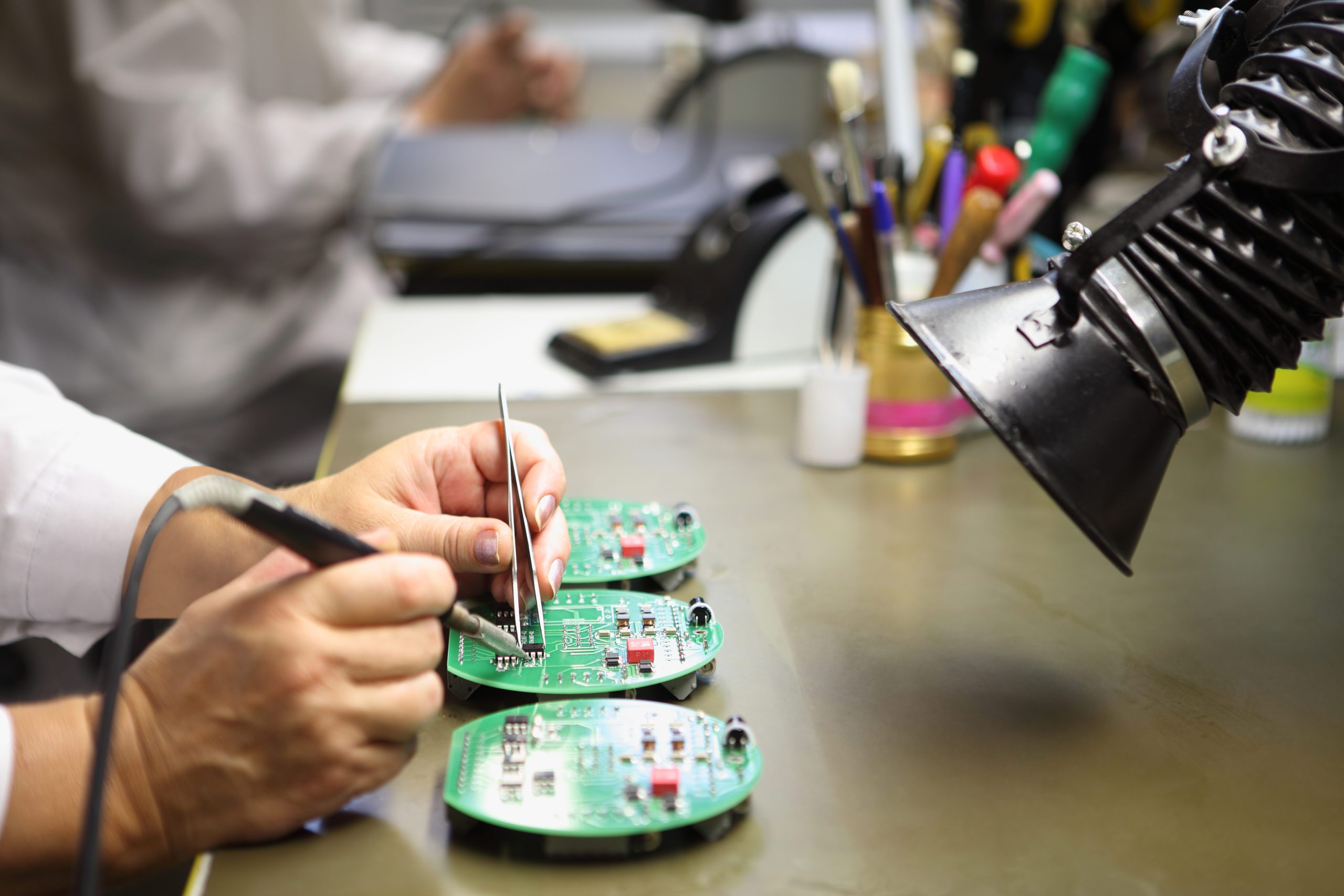
Trends in electronics manufacturing
Just in time or just too lean?
Inventory has become a dirty word in many manufacturing industries globally, as organizations attempt to align supply and demand with razor precision. Material orders have become smaller and more frequent, leaving very little buffer. The lean, just in time supply chain has successfully freed up capital for other purposes and seemingly worked well for decades. Until the crisis hit, that is. Now, significant weaknesses have been exposed in lean manufacturing. The impact has been particularly noticeable within electronics manufacturers. As Chinese suppliers disappeared into lockdown, the lead times for components ballooned amid component shortages. Organizations must now reconsider previously unquestioned supply chain principals and retain some supply fat. Just in time supply is set to become just in case inventory.
Invisible demand
The single biggest challenge facing global electronics manufacturers is visibility of demand post-crisis. Initially, the price of semiconductors spiked as shortages became apparent – now the next challenge is anticipating and responding to unpredictable demand. The pricing of electronic components is likely to fluctuate until demand gets back to more predictable levels.
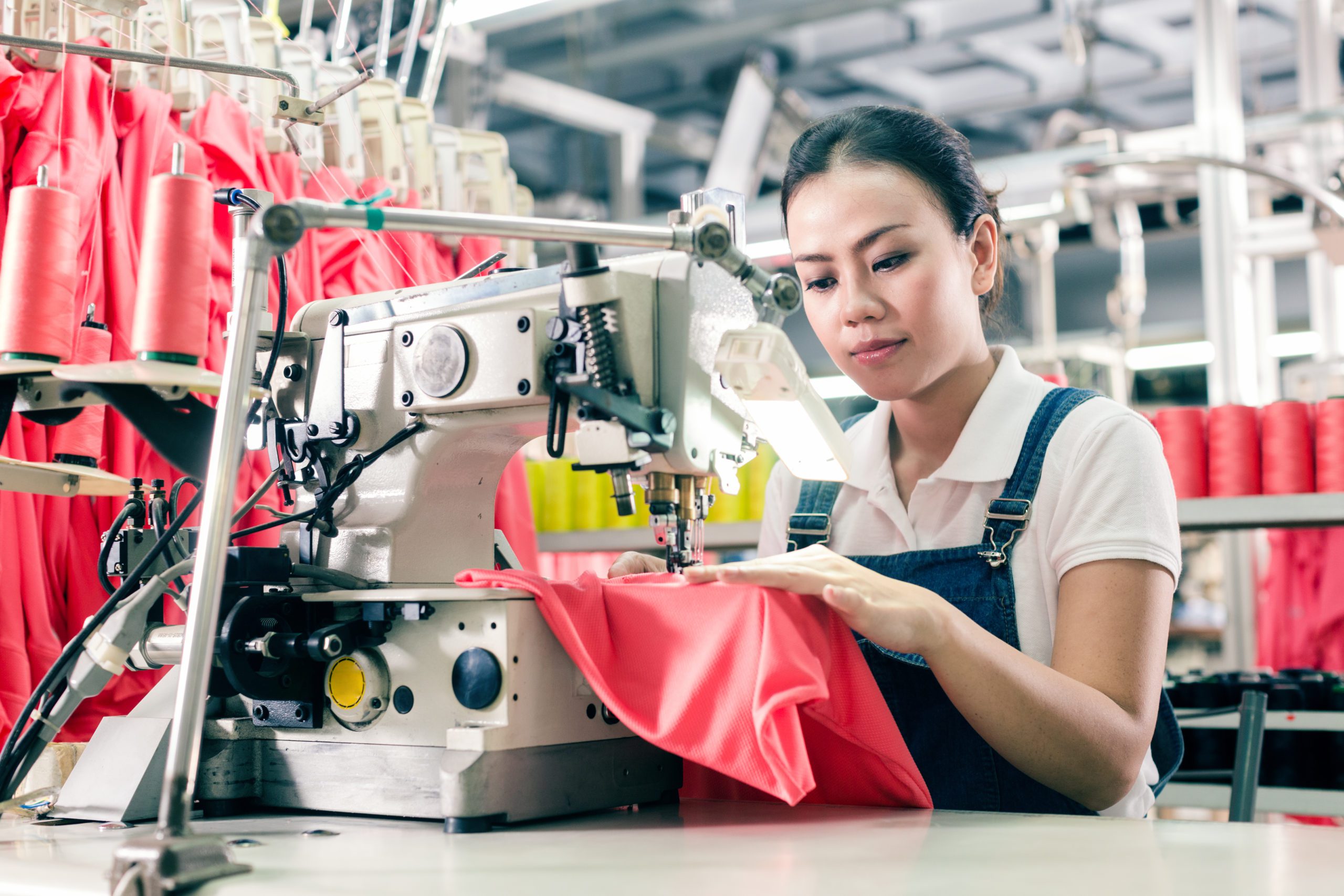
Trends in textile manufacturing
Overproduced fashion
Fashion manufacturing is set to change forever, as the crisis exposes fundamental flaws in the existing business model. While other industries have been chasing lean, ultra-efficient supply chains, fashion has remained largely unchanged. Overproduction is the norm within fashion brands, as garments are produced seasonally in advance, then shipped into retail channels. Market supply and demand are almost entirely disconnected, creating large volumes of unsold inventory. The excess supply is estimated to exceed 30-40% of overall production volumes. While significant levels of wastage are expected, these volumes have ballooned during the crisis, prompting calls for a shake-up of the business model. As the need for change intensifies, fashion marketing companies are playing a key role in adjusting strategies, emphasizing more sustainable and demand-driven approaches to meet the evolving market expectations. The inefficiency of existing players has created opportunities for disruption by emerging businesses challenging the status quo.
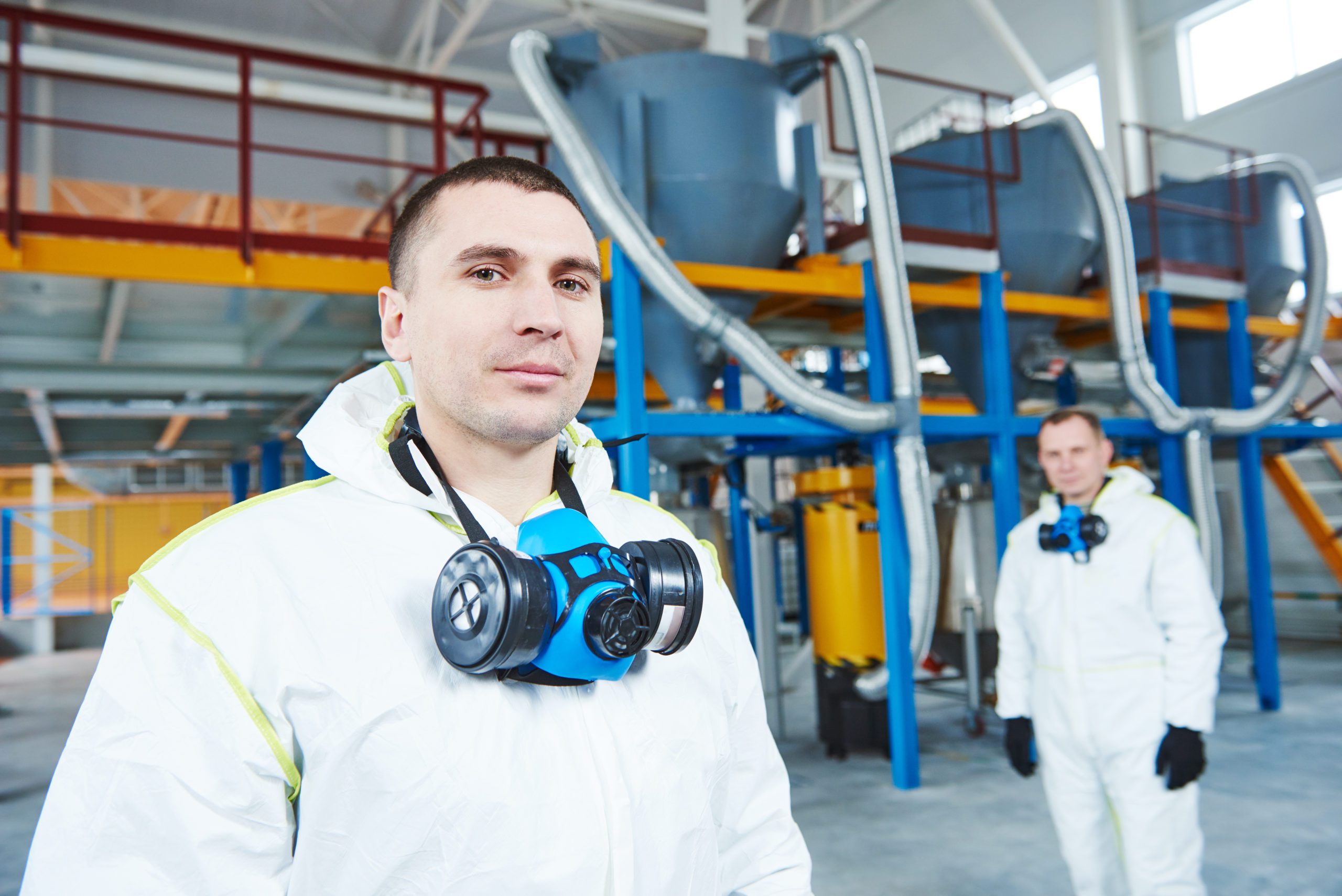
Trends in chemical manufacturing
Hand Gin’itzer
Chemical manufacturers around the world have wrestled with record demand for hand sanitizer. With many organizations unable to fulfil the insatiable demand created by the crisis, another unlikely manufacturer jumped categories to fill the void. As pubs shut their doors and purchase orders disappeared, London based 58 Gin turned to chemical production for the first time. Guidelines published by the World Health Organization provided the team with all the information required to engineer effective hand sanitizer. Production quickly shifted from boutique gins for British bars to hand sanitizer for everyone.
Packaging spikes
Traditional markets for chemical manufacturers have contracted as the crisis impacted demand for chemical products normally used in production. However, another new market has emerged with significant growth in chemicals used in the production of packaging. Demand for packaging has skyrocketed across food, health care items, and personal care use.
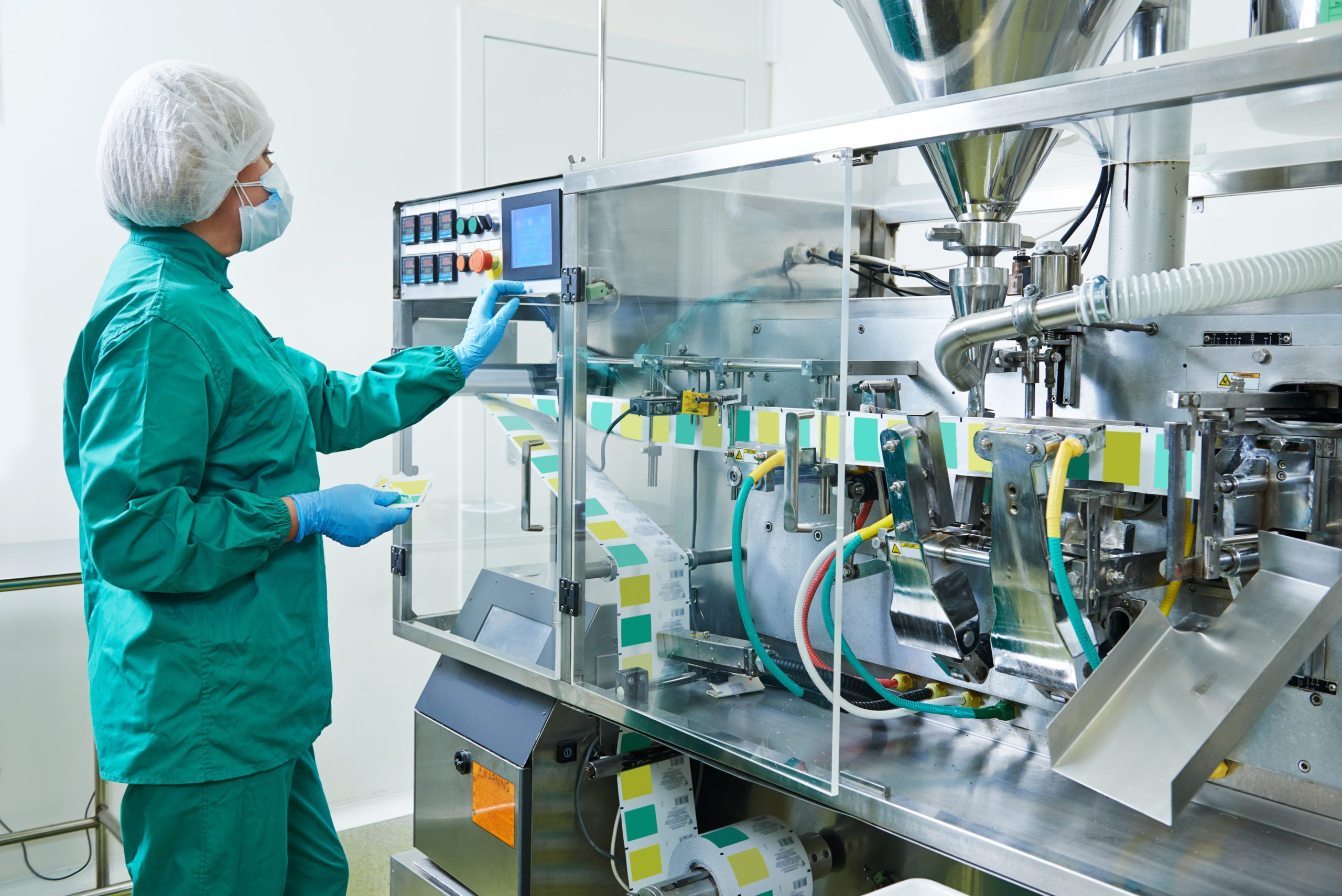
Trends in pharmaceutical and medical manufacturing
Offshore drugs
Supply chain volatility brought about the crisis has highlighted major gaps in local pharmaceutical production. The majority of drugs consumed throughout the developed world are produced in either India or China. As borders closed, governments around the globe have acknowledged the risk that offshore production of pharmaceuticals poses. Now, as the search for a vaccine continues questions surrounding access to drugs remain.
Forget the patents
Crippling shortages of medical equipment have led to unpreceded changes for medical manufacturers. Organizations that operated tightly held monopolies based on intellectual property rights have started giving away their designs. Global giant Medtronic has released the full designs of many best-selling ventilators to encourage supply. The diagrams have allowed manufacturers in Vietnam to start producing similar products within weeks. Medtronic has actively supported production by other organizations even offering assistance to tweak software or resolve production issues.

Trends in aviation manufacturing
Feather light recovery
Aviation manufacturers have been heavily impacted by the crisis as passenger flights are grounded across the world. New aircraft orders have disappeared, and existing orders have been postponed, as airlines assess the damage. Now, as the aviation industry prepares for reopening and increases in passenger numbers, capacity is front of mind. Social distancing restrictions will likely result in government-mandated restrictions on capacity for the foreseeable future. To compensate for the reduced capacity, airlines are seeking cost savings in other areas. Emirates and other major airlines have already started working with manufacturers on weight-saving design changes. One of the primary design changes being by manufacturers is ultra-light material for passenger seating. By introducing lighter material and small design changes to seating airlines can achieve significant reductions in weight and offset capacity restrictions.
Important Notice
The information contained in this article is general in nature and you should consider whether the information is appropriate to your specific needs. Legal and other matters referred to in this article are based on our interpretation of laws existing at the time and should not be relied on in place of professional advice. We are not responsible for the content of any site owned by a third party that may be linked to this article. SafetyCulture disclaims all liability (except for any liability which by law cannot be excluded) for any error, inaccuracy, or omission from the information contained in this article, any site linked to this article, and any loss or damage suffered by any person directly or indirectly through relying on this information.