Holding Your Supply Chain Accountable With Regular Auditing
Industry Trends | By | 5 Aug 2016 | 4 minute read
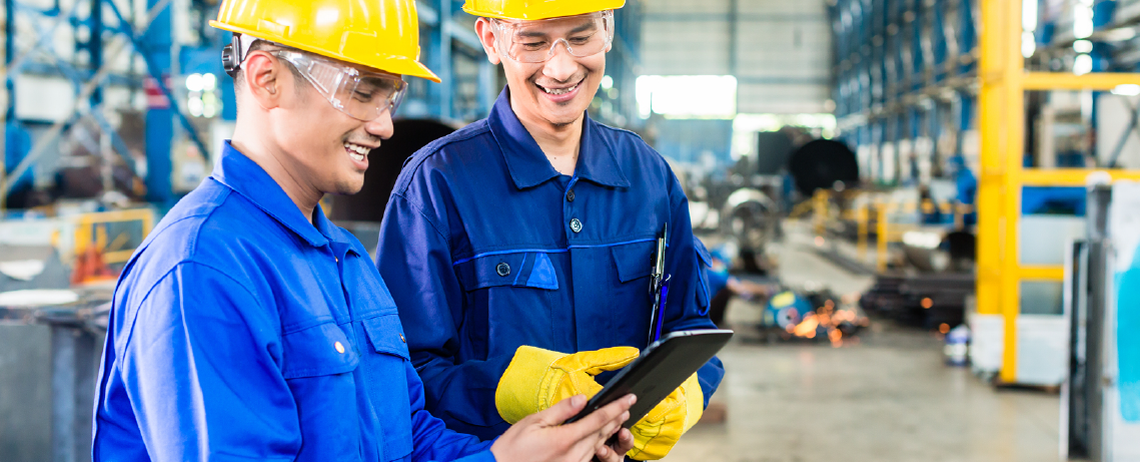
Ensuring that each step of your supply chain adheres to the same compliance standards that your own facility adheres to saves money in potential fines and violations, but also helps organizations tighten up the supply chain and provide the highest quality goods to consumers. Especially in today’s global market, it is getting increasingly harder to keep track of goods and their suppliers, whether that’s in the food and beverage industry, manufacturing, retail, etc.
Lumber Liquidators, for example, sold laminate flooring that contained levels of formaldehyde 20 times over the safety standard in California. It gave off enough of the carcinogen that it irritated the eyes, nose and mouth of many people and could trigger breathing problems in people with existing health conditions like asthma. The supplier to Lumber Liquidators illegally cut Mongolian oak trees in Russia, which are needed to protect endangered Siberian tigers and Amur leopards because their prey eat the acorns from the oak trees. According to the recent court ruling in federal court in February, Lumber Liquidators will have to pay upwards of $13 million in penalties. With advancements in legislation like the UK Modern Slavery Act of 2015, manufacturers are having to keep closer and closer attention on the supply chain. “Most companies do not know who their first-tier, direct suppliers are getting their raw materials from. Something could be in the products they’re buying that’s prohibited or not compliant and without sufficient auditing you could wind up with a damaged reputation and lost sales” says Maureen Gorsen, environmental attorney with Alston & Bird.
Sourcing of objectionable materials that could be:
- Hazardous to consumers’ health
- Mined or produced with slave labor
- Sold to finance violent conflicts
So how do we ensure that our supply chain is providing the quality of materials we need to maintain a reputable brand and provide the best possible goods to consumers? Our answer: auditing. In an Aberdeen report, 192 businesses were categorized as Best-in-Class, Industry Average or Laggards based on recorded violations and efficiency of production. The Best-in-Class businesses completed their audits on time 98% of the time and saw a 13% decrease in the number of regulation citations while all other businesses completed audits on time 85% of the time and saw a 1% increase in regulation citations. Clearly, auditing is a crucial part of keeping a supply chain running smoothly, safely and up to compliance standards. Auditing also provides traceability in accordance with the Bioterrorism Act that requires suppliers to be able to trace products one step forward and one step backward from their own facilities.
Let the audits be your guide
Quality assurance doesn’t work in a silo, but unfortunately many auditing processes operate differently at each location or within different teams. A more holistic and standardized approach will help food and beverage companies to gain visibility into the supply chain as a whole and improve the overall performance of the organization. This way, you can measure apples to apples and know where some branches or processes are failing and where others are excelling. In fact, in an Aberdeen survey of 192 businesses, those who were deemed “Best-in-Class” reported higher rates of audit standardization and transparency.
This standardization of audits and procedures provides the structure required to ensure that small but crucial tasks are not skipped, and also gives employees something to fall back on in unpredictable or new situations. Aberdeen research has shown that 52% of the businesses surveyed cite a lack of knowledge amongst employees as an issue within the business. This means that new employees being onboarded particularly need the auditing structure to aid in onboarding and in transferring of quality assurance responsibilities.
But more auditing doesn’t have to mean a drain on time
Automated auditing is the workhorse in your supply chain. Just because you’re standardizing your auditing processes and rolling out new forms doesn’t have to mean more time and more resources dedicated to the project (at least not after the initial setup). This is where automation can come in handy. Schedule audits, assign them to particular employees, assign follow up items and create notifications to pass along to management for any hazards. Best-in-Class companies are 54% more likely than their peers to automate management of their audit and inspection processes.
Best Practices on Collecting and Storing Audit Data
The use of flexible software allows the inspection process to grow with the company and adapt with any new processes that develop.
For maximum buy in, make it easy on your auditors – mobilize.
Inspections should provide structure and relief for auditors, not simply add extra work to their days. Finding a software solution that is easy to use and integrates into your existing processes and flows is crucial. Best-in-Class companies are over two times more likely than their peers to utilize mobile devices in their auditing processes. This allows for quick communication between auditors and managers, and escalates issues in real-time to the decision makers in the organization.
By providing software that works on a mobile device, you’re giving auditors a standardized platform to work on. Plus, with the mass adoption of smartphones and tablets, this is a device that most employees are likely already familiar with as well, further decreasing the barrier to entry. Mobile devices also allow you to capture and record data in the field and share it directly with management without having to return to a desk or enter data multiple times in order to track it. This brings us to the next crucial point about managing supply chains with auditing.
Centralize your audit data for better visibility
As you’ll notice in the chart above, Best-in-Class performers are also more likely to keep their audit data stored in a central location. This allows for better visibility and insight into the organization as a whole. You can identify locations that are performing well and dig deeper into exactly what they’re doing better in order to replicate that formula in other locations. You can also identify issues long before they become supply-chain-halting problems and address them early. For example, if there are a few portions of the audit that are consistently scoring too low, you may have a process issue, or may need to revisit training for a group of employees. The data from a centralized source will give you a guide into how to optimize operations. An ad-hoc, decentralized system will only create confusion in the event of an external audit or lead to incoherent collection of data.
Get the logistics down
So you’ve been sold on the importance of centralized, mobilized and standardized auditing across your entire supply chain. Now you need to ensure you have the same conversation with each supplier you onboard and all your pre-existing ones. What is the frequency of your auditing schedule? Are these planned or surprise audits? How much time will suppliers have to complete corrective action? How are changes in the suppliers’ suppliers going to be communicated to you? Who is responsible for suppliers’ audits?
Further Reading:
- Audit expectations and trends in the food and beverage industry podcast
- Audit inspection management – Aberdeen Report
- Weakest Links In Your Supply Chain
- The Food Safety Challenge Of The Global Supply Chain
Important Notice
The information contained in this article is general in nature and you should consider whether the information is appropriate to your specific needs. Legal and other matters referred to in this article are based on our interpretation of laws existing at the time and should not be relied on in place of professional advice. We are not responsible for the content of any site owned by a third party that may be linked to this article. SafetyCulture disclaims all liability (except for any liability which by law cannot be excluded) for any error, inaccuracy, or omission from the information contained in this article, any site linked to this article, and any loss or damage suffered by any person directly or indirectly through relying on this information.