How Digitizing Small Processes Can Increase Productivity in the Oil and Gas Industry
Industry Trends | By | 3 Apr 2019 | 2 minute read
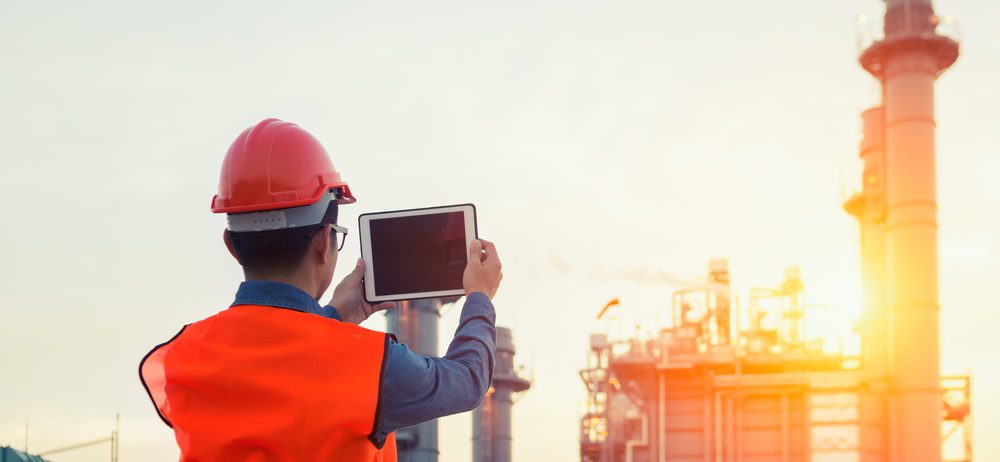
The Oil & Gas Industry is a diverse and dangerous field. Working with machinery, chemicals, unpredictable natural resources and a large workforce can lead to any number of potentially risky tasks.
As is the case in most industries, it’s not always easy to identify and track the risks and compliance issues that workers face every day. This is the case for a number of reasons, but the biggest, and easiest to fix, is how companies track risk and compliance, and how managers use safety information to quickly address any problems to transform the workplace.
Paper vs. Digital Processes
Many organizations use paper checklists to keep track of the many safety requirements and processes necessary to keep employees safe. However, making the simple change from paper to digital processes can have a big impact on productivity and effectiveness.
By using digital checklists, employees can record in real-time what’s happening on site. By enabling teams with accessible digital tools, like checklists, that are easier and less cumbersome than paper, safety habits become second nature. The data these checklists collect are deposited immediately into digital databases to be used to identify issues, patterns, problems and potential solutions. Just like that, the safety checklist that used to take your employees too long to complete and process, is streamlined and stored in one, collective place.
Data collation is key
One of the most time-consuming elements of using checklists to ensure compliance is entering all the data collected via paper checklists and sorting through it for patterns and problems. This is where digital checklists really save time, automatically uploading the data into a central location and enabling supervisors to not only see that every day’s required tasks are being completed, but also gives the ability to drill down into the information and identify patterns, issues, problems and potential areas of improvement.
It’s the data that really helps boost productivity and enables workplaces to implement new systems and adjust old ones, so they are more efficient and effective.
Making the switch
Companies that have implemented digital checklists have found that the insights they provide not only make things safer and more efficient, but save money in the long run by raising the safety bar and lowering workers compensation premiums in return.
Read more by downloading our eBook: How Digitizing Small Processes Increase Productivity.
Important Notice
The information contained in this article is general in nature and you should consider whether the information is appropriate to your specific needs. Legal and other matters referred to in this article are based on our interpretation of laws existing at the time and should not be relied on in place of professional advice. We are not responsible for the content of any site owned by a third party that may be linked to this article. SafetyCulture disclaims all liability (except for any liability which by law cannot be excluded) for any error, inaccuracy, or omission from the information contained in this article, any site linked to this article, and any loss or damage suffered by any person directly or indirectly through relying on this information.