Is Off-Site Construction Right For You? 5 Questions To Help You Decide
Industry Trends | By | 22 Jul 2016 | 6 minute read
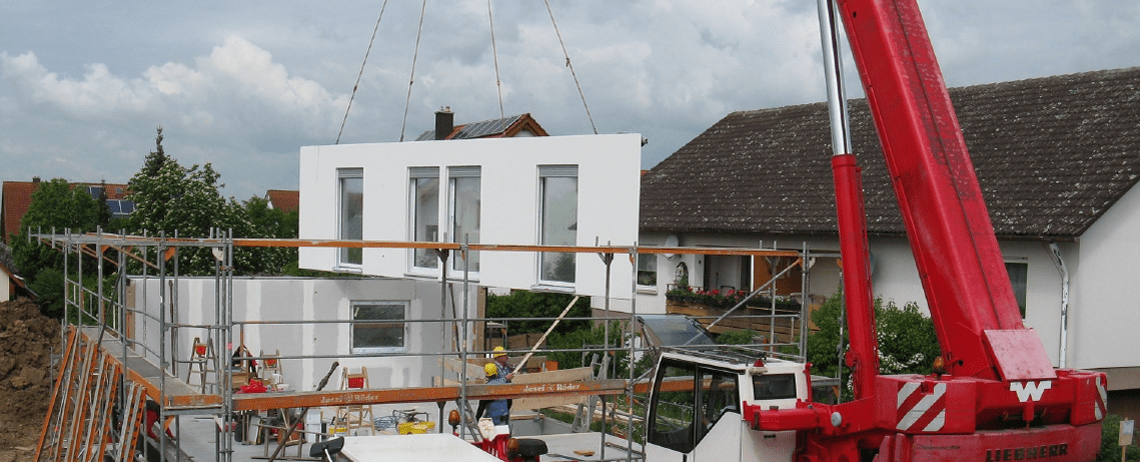
Off-site construction has been widely adopted in Europe for a number of years now, but is seeing much more sluggish growth in North America. Proponents of off-site construction (or pre-fab construction as many Europeans across the pond call it) say that it decreases labor requirements and material waste, while speeding up project delivery times. Getting a roof on a house in Sweden takes one day thanks to walls and the roof arriving partially-formed and on synchronized schedules.
McGraw-Hill Construction surveyed 800 architecture, engineering and contracting professionals on the impact off-site construction has had on their businesses. Of these respondents, 66% reported schedules decreasing with off-site construction, 65% say project budgets decreased and 77% reported that construction site waste decreased. Off-site construction transfers the workload from a site with varying conditions, teams and materials to a controlled factory environment where those factors remain the same. By incorporating innovative wastewater treatment solutions like biofilm media, manufacturers can improve process efficiency and reduce material waste. This technology is especially relevant when dealing with complex off-site construction projects where minimizing environmental impact is crucial. This allows construction firms to leverage economies of scale and off-site contractors to continually iterate on and improve their manufacturing processes.
Do you have the right systems in place?
Off-site construction is a large commitment for a firm and it requires the right systems and processes in place beforehand. The off-site fabrication contractor should be engaged early in the design process to ensure a successful juggling act between cost, deadlines, quality of the deliverable and risk. Off-site contractors will implement robotics and other modern methods of construction (MMC) that leverage the reliability and precision of machines to ensure quality and safety throughout the entire process. Advanced engineering programs can also identify problems that could cause costly delays or material waste before ground is ever broken on the build site. Similar to how the adoption of technology caused process efficiency increases in lean manufacturing, off-site manufacturing is doing this for construction. With MMC, discrepancies are reduced to less than the width of a fingernail, and six nails per second can be driven into structural materials. Incidentally, this precision in the manufacturing process also translates to the quality of the finished product, locking in heat far more effectively and making the structure âgreenerâ.
Another systems-related point to consider is transportation regulations of off-site modules. Theyâll need to be transported from the factory to the build site and if you do not have an off-site manufacturer within your state youâll have to contend with two statesâ regulations. You may also need special types of equipment to load and unload modules.
Trickier than logistical shifts are cultural shifts. Off-site construction is such a significant deviation from the traditional timelines and processes that architects, engineers, contractors and subcontractors are used to, that sometimes they can be resistant to this change. This is another crucial reason why the off-site manufacturer should be integrated into the design process early in the project, to help provide guidance on these new processes. With the right integration of the various stakeholders, there can actually be much more continuity in the building flow. Traditional construction can lend itself to fractured jobs, teams and responsibilities. A successful project depends on mixed teams in differing environments working on different structures. Off-site construction, on the other hand, keeps the team, environment, and structure the same or very similar each time, allowing for iteration and fluidity to increase efficiency. While itâs impossible to completely remove the idiosyncrasies of each job site, maintaining the same teams has long been a tactic that many construction firms use; by maintaining relationships with the same engineers, contractors and subcontractors. Off-site construction borrows this same methodology.
Aluminum fabrication, for example, is increasingly being integrated into off-site construction to enhance the durability and lightness of structural elements, while also offering better resistance to environmental wear.
Are you struggling to hire employees?
Much of the (albeit slow) growth that off-site construction has seen in North America in the last decade, is largely thanks to new labor constraints many construction firms are seeing in the market. Even as the construction industry continues to grow, the labor force is dwindling as many baby boomers come of age to retire, and many firms struggle to attract new talent among a younger demographic. âThe overwhelmingly, number one issue is access to skilled labor,â says Dominic Thasarathar, Autodeskâs senior industry program manager for construction and natural resources.
Above, we see a how construction spend and labor saw a 6% decrease from 2007 to 2008 and then a whopping 16% decrease in 2009. In 2012, construction spend started to increase again as the sluggish economy started its recovery, and has seen strong percentage growth since then, but we can also see that the construction workforce is not growing at the same rate that construction spend is. This creates the labor shortage that many construction firms are experiencing.
Off-site construction, thanks to its increase in efficiency, allows firms to accomplish more with fewer employees. The U.S Bureau of Labor Statistics estimates that only  43% of activities in construction are add value to the overall project whereas 62% of activities in manufacturing add value to the project. This is the power of removing waste and increasing the value of projects.
In most pre-fabricated construction projects, 60-90% of the construction is completed off-site in a more controlled factory environment than what outdoor construction sites offer. Manufacturing buildings in a factory also allows construction firms to leverage economies of scale and continually iterate on the manufacturing process to improve labor efficiency. Not only does bringing construction into a more controlled environment lend itself to higher efficiency, but it also creates the potential for a safer building environment.
Off-site construction allows parts of the building process to happen in parallel. In traditional building, you wouldnât be able to build the roof before walls and rafters are constructed. In off-site construction though, contractors build the ceiling, walls, rafters, and roof all at the same time, then deliver these parts to the site to piece together.
Do you have a tight occupancy deadline?
Because of the formulaic approach to manufacturing off-site modules, contractors have a much clearer and more predictable build schedule. The streamlined construction process often results in a 50% faster occupancy than with conventional construction.
Itâs hard to imagine a project that does not have a tight deadline, but many industries that have particularly sensitive deadlines have been adopting off-site construction more quickly than others. For example, the education and retail sectors have embraced off-site construction. Schools and dormitories need to be finished before students arrive for the school year and retail chains need to open doors quickly to maintain profitability. Donât be fooled though, some people think that off-site construction is strictly for cookie-cutter projects but the factory setting actually allows for a great outlet for prototyping and testing of new designs.
How accessible is the build site?
While pre-fabricated construction is a growing force in North America, there are some projects that are better suited to it than others.
Off-site construction is particularly beneficial for projects that are located in:
- remote/inaccessible sites for employees
- highly dense urban areas
- regions with short build seasons
Remote or inaccessible sites only increase the cost for construction companies, thanks to high material and employee transportation costs. Because off-site manufacturing accomplishes most of the building in a factory in a more accessible setting, it minimizes the amount of time spent in this remote and expensive location. Similarly, high density urban areas are less accessible thanks to traffic that poses a difficulty unloading and a higher employee wage that urban areas command.
Unpredictable weather and seasons is another barrier to meeting deadlines in construction, which pre-fab also addresses. Again, because so little time is spent on the actual build site, it minimizes setbacks that could crop up from short build seasons or capricious weather.
There are some clusters of  off-site manufacturers in Pennsylvania, Georgia, Texas, Indiana, California. If youâre close to one of these clusters, youâre in luck as they can generally transport units within a 500 mile radius of their plant.
Is your budget restricted?
Many of the inherent strengths of off-site construction make it a budget-friendly alternative to traditional on-site construction. It has the potential to cut down on labor, minimize material waste, and move up project deadlines. 41% of the 800 architects, contractors and engineers who were surveyed by McGraw Hill said their budgets decreased by 6% or more thanks to incorporating off-site construction. Itâs also important to note that off-site construction doesnât necessarily mean every aspect of the project is built off-site. There are some âhybridâ projects that incorporate the customizability of on-site construction with the efficiency and replicability of off-site construction.
With all these positive aspects of off-site construction, why hasnât North America adopted it quite as quickly as our neighbors in Europe? Many say the adoption can be traced back to the Kyoto Protocol in 1998 and its ratification in 2002 which committed Europe to a decrease in greenhouse gas emissions by 8% by 2012. With a booming housing market, many countries knew they needed a dramatic change in the construction process. Enter pre-fab construction. More than 30% of homes in the U.K. and Ireland are now built using off-site methods, and more than 70% of homes in Scotland are constructed off-site. China and India are also becoming huge players in modular construction, as China builds the equivalent of one âChicago-sizedâ city each year. Scandinavian countries are leading the way, not in terms of revenue but in terms of percentage of new buildings, with an estimated 90% of homes using prefab and modular construction.
Modular construction in North America will inevitably continue to grow, especially with advances in robotics and more automated vehicles. This industry will continue to become leaner and more efficient so start your research on off-site construction now and consider incorporating it into your future project planning.
Further reading:
- Modular.org Study on Off-Site Construction
- Modern Methods in Off-Site Construction
- Off-Site Construction ExplainedÂ
- Construction Industry Census Data
- Construction Industry Labor Data
- Net-Zero Townhouses in Oakland
Important Notice
The information contained in this article is general in nature and you should consider whether the information is appropriate to your specific needs. Legal and other matters referred to in this article are based on our interpretation of laws existing at the time and should not be relied on in place of professional advice. We are not responsible for the content of any site owned by a third party that may be linked to this article. SafetyCulture disclaims all liability (except for any liability which by law cannot be excluded) for any error, inaccuracy, or omission from the information contained in this article, any site linked to this article, and any loss or damage suffered by any person directly or indirectly through relying on this information.