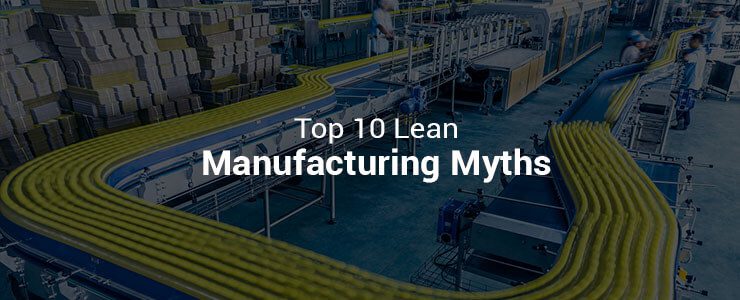
There are a lot of common myths about what goes into implementing a lean manufacturing strategy. Lean manufacturing is the process of ‘lean thinking’ whereby companies make a conscious effort to eliminate waste or any activity that consumes resources without adding value in design, manufacturing, distribution, and customer service. While Toyota didn’t necessarily invent this idea, they were the one that refined it and popularized the concept. In 1996 it became known globally due to a book published called ‘Lean Thinking.’
Lean Manufacturing is a continuous improvement philosophy with a razor sharp focus on reducing waste. ‘Waste’ refers to anything in the lean manufacturing process that doesn’t add value to the customer or is something they would pay for. There are generally seven types of waste, such as:
- Overproduction against plans
- Waiting time of operators and machines
- Unnecessary transportation
- Waste in the process
- Too much stock
- Non-value adding activity
- Low quality
The Lean process of thinking is often applied to the manufacturing industry, but can very well be used in other industries, such as the process of preparing and serving fast food.
To implement a Lean Manufacturing process in your own company, you don’t have to wipe clean the decades of hard work. In John Davis’ best selling ‘Lean Manufacturing: Implementation Strategies that Work’ he notes that it boils down to revising your implementation strategy and quashing the common myths you come across.
Myth #1 Lean Manufacturing is all about the tools
When people hear about Lean they immediately conjure thoughts of the 5 Whys, the 7 wastes, Kanban, and more. These tools are great, but they need a strong structure and culture associated with them. Production tools are undeniably important, as they need to be geared to respond the way it should. People will be hampered if tools aren’t operating reliably. However, without a lean management framework, the tools and people will fall short of their potential.
Myth #2 Once you implement Lean you can stop thinking about it
Lean requires constant iteration and evaluation. Perfecting the process requires commitment from your team to challenge their own style of thinking and to continuously strive for improved quality, cycle time, efficiency and cost. Lean is a powerful process that allowed Toyota to grown from a company that made products of little value, to one of the most successful corporations in the world.
Myth #3 Lean is only about cost reduction
Lean manufacturing is about making the work easier and less frustrating so that time at work can be spent on what matters like serving customers and growing as a team. Lean is about value, a bigger and more inclusive concept than mere cost. Cost reductions will follow when the long-term strategy is about constantly improving and changing for the better. Waste is anything that does not contribute to value, and anything that the customer does not want to pay for.
Myth #4 Lean means zero inventory
Lean doesn’t mean having no inventory at all. It means thinking about what you need in a smart way. To be Lean you need to have the right inventory when you need it, and in the right quantities exactly when you want to use it. Every company does need a buffer, but they can be planned and controlled. Low inventories come at the result of having an improvement in your process due to practising ‘Lean Thinking.’ Apple, one of the most successful companies in the world operates with very little inventory, unlike their competitors HP and Sony. In 1997, Apple had 437 million in inventory with 7 billion in revenue. In 2006, Apple had 270 million in inventory and over 20 billion in revenue. Clearly, Apple’s Lean manufacturing strategy has worked. It is so efficient, that customers can order an iPhone online, complete with custom add-ons and have it mailed to their door within a few days. They have done so by minimizing the products and colour combinations, so consumers have a ‘closed’ product. Apple is far from just a product company, it has morphed into an incredible industrial manufacturer.
Myth #5 Lean doesn’t require different equipment
Any difficulty in moving forward with a Lean initiative comes down to equipment. Equipment should be reliable and consistent. Equipment of high quality can substantially lower operating costs and can often lead to a reduction in factory lead-time. Your Lean strategy should include the minimization of equipment bottlenecks that cause disruptions in your assembly lines.
Myth #6 Lean is only used to get rid of waste
Yes, Lean is about getting rid of waste. ‘Muda’ is a key concept in the Toyota Production System (TPS). Waste reduction is an effective way to reduce costs. Getting rid of waste in Lean means getting rid of the root causes, which could be due to overburdening the system or too much variation in your product. It is advisable to keep an eye on the amount of waste, but also the system or process that is causing it.
Myth #7 Lean is the latest management fad
The term ‘Lean’ is sure to be replaced by something more buzzworthy as people look to understand it more. Lean is not the lastest anything other than a scientific method tried and tested, and a desire for making a process better for when things are invented. NUMMI was opened in 1984 by General Motors and Toyota. It is a well-known story in the car manufacturing industry that General Motors NUMMI factory struggled to adopt the Toyota Production Process that enabled Toyota to build high quality cars. Entrenched and defensive bureaucracies stopped NUMMI from being able to successfully implement Toyota’s system as effectively as it worked in Japan. It was the culture of opposition to change that really caused the eventual closure of the factory.
Myth #8 Lean is about squeezing more out of people
Lean at its core is about reducing waste, not making people work twice as hard. It takes the same effort to do a wasteful process as an effective one. Many workers are in disbelief when you tell them their team could double their output without putting in more hours. The only thing that should be squeezed out of people are ideas to improve upon processes.
Myth #9 Lean means a reduction in jobs
Nobody wants to cost themselves their job by improving a process. Using the Lean method you can capitalize on process improvement without cutting jobs. If you do, you risk negatively impacting your team as they will associate ‘Lean’ with ‘job loss.’ Likewise, sometimes people associate Lean with making your employees robots. Lean isn’t about mindless conformity, it provides a baseline for people to improve upon. By adopting a more routine approach to process, employees can have more capacity to find further improvements.
Myth #10 Lean is only for the shop floor
The concept of kaizen can be adopted in virtually any workplace. The Japanese business philosophy of ‘continuous improvement of working practices and personal efficiency’ does not just relate to manufacturing processes. It has been applied time and time again in a range of industries. Lean Office and Lean Healthcare are now common words.
The Future of Lean Manufacturing
Big Data holds huge potential to further optimize the manufacturing process to improve efficiency, quality, and a reduction in failure. The future could have Big Data identifying correlations between customer data or maintenance, anticipate order times, shorten machine downtimes or make better operating decisions. It has the potential to enable companies to find more efficient operating processes by identifying patterns in the data. Connected machines can provide a new capability that is likely to completely change the landscape of manufacturing. The challenge will be for companies to start investing in systems and practices to collect more data, in order to effectively analyze it.
Find out more about how you can use iAuditor to improve safety and quality for engineering and manufacturing projects.
Important Notice
The information contained in this article is general in nature and you should consider whether the information is appropriate to your specific needs. Legal and other matters referred to in this article are based on our interpretation of laws existing at the time and should not be relied on in place of professional advice. We are not responsible for the content of any site owned by a third party that may be linked to this article. SafetyCulture disclaims all liability (except for any liability which by law cannot be excluded) for any error, inaccuracy, or omission from the information contained in this article, any site linked to this article, and any loss or damage suffered by any person directly or indirectly through relying on this information.