Using Data to Increase Quality and Safety
Industry Trends | By | 3 Apr 2019 | 2 minute read
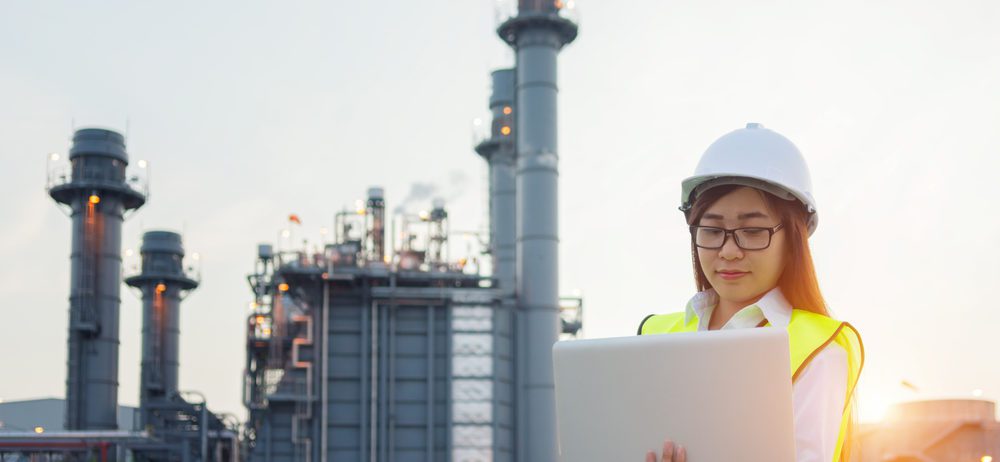
Gary Bonnett, Director of Quality, Health, Safety and Environment at BOS Solutions, had a frustrating problem. He lacked visibility into quality and safety performance because the data coming in from jobsites across the United States was siloed, in most cases, there was little or no data available from different sites for managers to share or review across the company, stripping the data of valuable context and making trends and insights impossible to predict.
It’s an issue across many organizations that have siloed teams in various locations, quality data is often scarce and difficult to track down because everything is still being logged on paper and there’s no one central database to draw insights from. Not only is location a barrier for providing good data, but teams using paper-based processes experience lag and accuracy in getting information to key leadership. When the information does get there, it is often not quickly enough to act on the hazards that do get identified. Paper processes in dispersed organizations often lead to a lack of standardization, which makes reporting and compliance challenging and cumbersome.
Organizations in this cycle of antiquated paper processes leading to useless data, often don’t realize the impact that Big Data (large data sets to be analyzed to reveal patterns, trends, and associations) could have on their bottom line.
For BOS Solutions the benefits became clear when they implemented digital checklisting platform, iAuditor, to take their paper-based quality and safety inspections digital. They now use digital checklists across most internal processes—from Quality Health and Safety field audits, PPE inspections, contractor onboarding, equipment servicing, asset tracking, and work permitting.
Now it’s easy for leadership to track proof of past compliance in the form of historical data. With the implementation of digital platforms like iAuditor, organizations can streamline data sharing across locations, enabling real-time insights and collaboration, and can view, from every site location, inspection performance and identify hazards as they arise, in real-time. When reviews arise, the data is available in an easy, digital format. BOS can view, from every site location, inspection performance and identify hazards as they arise, in real-time. And their Total Recordable Injury Rate (TRIR) has decreased by 56 percent since implementation. The data collected reduced BOS’s workers compensation premium by $80,000 this year. And, the boost in visibility into team performance has led to an increase in inspection scores. Employees are more engaged and managers can see deeper into processes.
Data was BOS’s secret weapon to initiate this organization-wide change. While digital checklists helped standardize processes and elevate data quality, the organization’s analysis and use of the data from inspections has led to the greatest change.
Want to dive deeper into how data can affect your organization? Check out this ebook about how digitizing processes can increase productivity.
Important Notice
The information contained in this article is general in nature and you should consider whether the information is appropriate to your specific needs. Legal and other matters referred to in this article are based on our interpretation of laws existing at the time and should not be relied on in place of professional advice. We are not responsible for the content of any site owned by a third party that may be linked to this article. SafetyCulture disclaims all liability (except for any liability which by law cannot be excluded) for any error, inaccuracy, or omission from the information contained in this article, any site linked to this article, and any loss or damage suffered by any person directly or indirectly through relying on this information.