Wearable Technology That Will Change the Construction Industry
Industry Trends | By | 11 Jan 2016 | 3 minute read
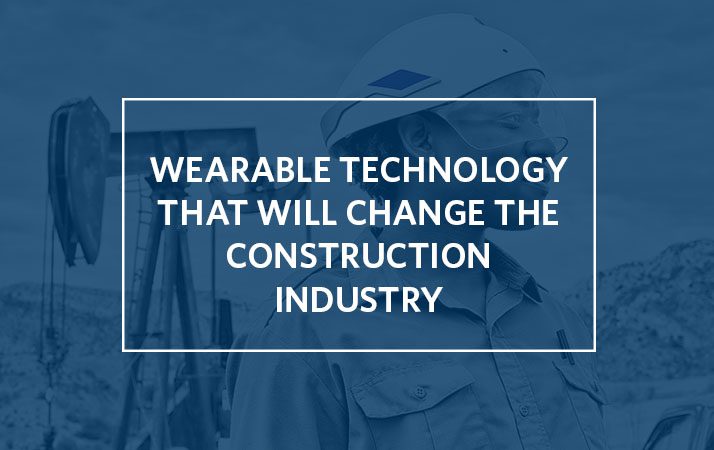
Innovative companies around the world are looking to bring more wearable tech to the job site, by focussing on innovating existing gear. Common assets to a construction worker like the hard hat, safety vests and even the tools they carry, are being infused with new capabilities.
The Hard Hat of the Future
Display visors on hard hats can dynamically project relevant information onto the surfaces of objects in the wearer’s field of vision. Photo courtesy of Daqri.
Just like seat belts in cars, hard hats have saved countless lives and prevented even more injuries. Despite having been around for hundreds of years, the design hasn’t changed too much.
California-based firm Daqri is transforming the standard hard hat with advanced technology.
The Daqri Smart Helmet looks like a traditional hard hat but features a clear visor that can display 3D visual overlays in the wearer’s field of view.
A 360° wireless camera allows a full view of the worker’s surroundings. The system is capable of a form of augmented reality, in which images can be made to appear dynamically on surfaces in the surrounding environment with drop down HD displays (similar to Google Glass).
The Smart Helmet was designed primarily for industrial work to aid construction workers on the job site. With a price tag of a few hundred dollars above an ordinary hard hat, it may remain a premium item for a while.
A Safer Safety Vest
Safety vests may soon have the ability to warn workers of approaching vehicles on construction sites. Photo courtesy of Virginia Engineers.
Safety vests are commonplace on jobsites, and technology companies are looking to infuse their innovations into standard gear. Red Point Positioning has been using GPS-enabled safety vests to track worker locations across crowded jobsites. As a result, workers within a geofenced jobsite can be located with the utmost precision, within 8 inches in fact.
GPS-type positioning can monitor workers relative to equipment and keep them out of danger zones. Imagine the amount of real-time feedback a system like this can have. Although tightly controlled, sensor-laden jobsites can work with GPS wearables, construction sites like a busy highway project can be a bit more difficult.
In 2013 alone, 579 people were killed in highway work-zone related accidents. Engineers at Virginia Tech hope to greatly reduce that number by developing a smart safety vest that gives several seconds of warning to workers if danger is approaching.
Tom Martin, a Virginia Tech electrical and computer engineering professor developed the InZoneAlert safety vest. The vest incorporates a dedicated short-range communication (DSRC) system that allows vehicles to communicate to each other via radio signals. The idea behind the vest was to allow workers and cars to be alerted of each other’s presence on busy construction sites.
Martin’s team believes that in 5-10 years, most cars on the road will have the DSRC system built in, with a GPS system and radios that can communicate in driverless or semi-autonomous cars. The outcome presents the possibility that driverless and semi-autonomous vehicles could one day be programmed to automatically avoid construction workers.
As very few cars on the road currently use DSRC, the vest is looking to be deployed in 5-10 years despite initial tests that wielded a success rate of 90 percent.
Bionic Suits for Construction Workers
Ekso Bionic’s powered exosuit could assist construction workers with heavy loads, reducing fatigue and strain related injuries. Photo courtesy of Ekso Bionics.
The world’s first bionic suit has been made specifically with the construction industry in mind. Although it doesn’t allow you to fly or shoot beams like the Iron Man suit, it does promise to aid construction labourers in lifting heavy loads and reducing strain and risk of injuries.
One manufacturer, Ekso Bionics has developed a lightweight, powered harness after re-imagining the limitations of the human body. The suit uses no electricity or batteries to function and is powered by counterbalance and a single spring arm. WIRED Magazine’s, Adam Rogers tried out the product and gave his review.
The suits were originally built for the military and later expanded into physical therapy. Incredibly, they have made it possible for wheelchair users to stand up and walk a distance.
The injuries that occur from poor lifting techniques and fatigue from lifting heavy tools and material all day could be a thing of the past.
Find out more about using iAuditor with the construction industry here.
By Tania Clarke, Communications Coordinator for SafetyCulture
Important Notice
The information contained in this article is general in nature and you should consider whether the information is appropriate to your specific needs. Legal and other matters referred to in this article are based on our interpretation of laws existing at the time and should not be relied on in place of professional advice. We are not responsible for the content of any site owned by a third party that may be linked to this article. SafetyCulture disclaims all liability (except for any liability which by law cannot be excluded) for any error, inaccuracy, or omission from the information contained in this article, any site linked to this article, and any loss or damage suffered by any person directly or indirectly through relying on this information.