Connected data – the future of work starts now
iAuditor by SafetyCulture Tips | Tips & Tricks | By | 13 Jul 2020 | 5 minute read
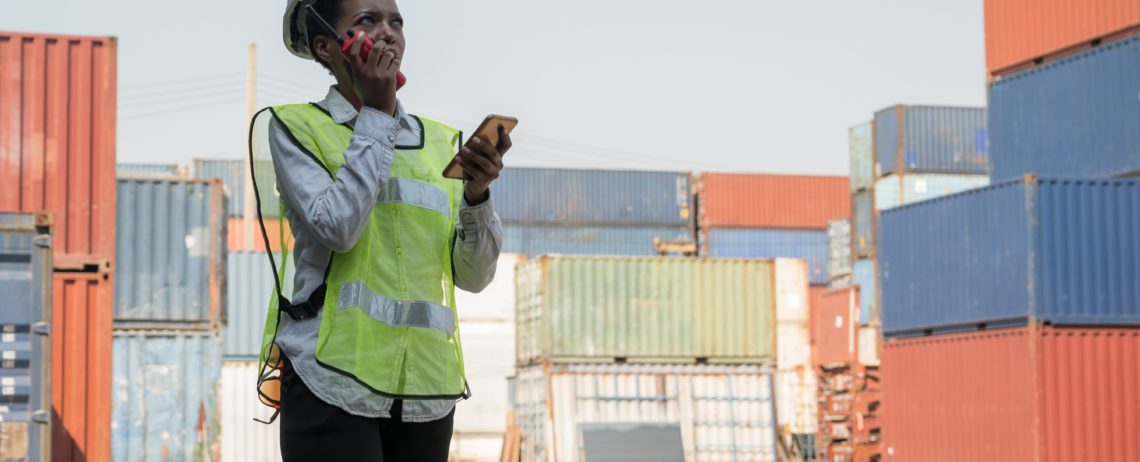
Visibility is everything
How much visibility do you have within your business right now?
If an incident occurred in the next 30 seconds, how long would it take for the right team members to notice and respond?
For many organizations, the answer is too long, and this question spikes the heart rate of leaders everywhere.
In the post COVID-19 world, fast response times are mandatory for continued success. Early access to critical operational data is more important than ever before. Lack of visibility can delay an organization’s response to incidents, prevent decisive action, and result in catastrophic failure. The delays introduced by paper-based data processing can turn small, easily managed incidents into brand-damaging, growth stalling disruptions that customers notice. Yet, many organizations still lack the real-time visibility necessary for robust operations.
Make connected data your new competitive advantage
Businesses that develop a proactive culture that encourages clear visibility of operational data have an opportunity to build a strong competitive advantage. Prevent revenue impacting events before they occur and identify neglected opportunities in real-time with connected data. Gain full visibility of your business from digital incident reports by frontline staff to integrated temperature sensors, and mobile compliance checklists. Join the future of work with an innovative and consolidated approach to connected data.
The three types of connected data mandatory for smooth operations
Organizations require three distinct types of connected data to protect their brand, maximize employee safety, and ensure that operational hiccups remain invisible to customers:
Stay compliant and in control with planned data
Increase operational visibility and track performance over time with planned data. Proactively introduce digital checklists and inspections that can be completed and tracked in real-time, ensuring that your organization remains compliant. Python ETL can be used to process and manage this planned data efficiently. Use planned data to enable teams to complete mission-critical tasks with clear expectations and accountability. Quickly view completion data anywhere to understand how your assets, employees, and locations are performing. Leverage your strengths and address your weaknesses instantly with planned data that matches your business requirements.
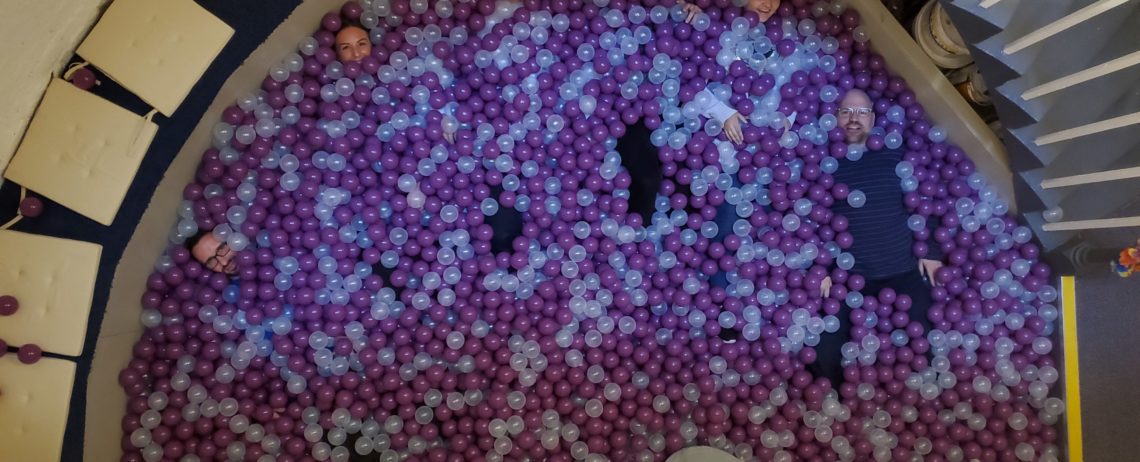
How planned data streamlined SafetyCulture’s reopening
Here at SafetyCulture, we used iAuditor to develop a comprehensive new approach for reopening our offices around the world. We needed to ensure that our processes were compliant with government measures and that our staff felt safe when they returned to our offices.
Starting with the first reopening location in Manchester, we completed a comprehensive risk assessment and captured photos using iAuditor. Next, we introduced the necessary hygiene and social distancing changes that were identified throughout our risk assessment. Then, we used digital checklists to ensure that enhanced hygiene levels and social distancing measures continued to be maintained. Regular inspections were scheduled, and the right team members were automatically notified upon completion. Finally, we asked our staff members to complete a digital return to work form to educate them on the new processes and capture signatures, ensuring that every employee had reviewed this important information. The checklists and their completion data were made available to all team members as an extra layer of visibility and accountability. After Manchester reopened safely, we were able to successfully implement the same processes across all of our offices globally.
iAuditor helped SafetyCulture offices globally by consolidating all of our reopening data into a single location, and by taking the guesswork out of getting safely back.
Identify and resolve issues faster with ad-hoc data
Remove the paper hurdles that are delaying the flow of critical information within your business. Learn about critical issues instantly and develop a culture of safety by enabling frontline workers to capture ad-hoc data as incidents occur. Easily capture key information when an event occurs, then automatically distribute the details, complete with photos, to a predefined list of stakeholders. Prevent incidents from reoccurring with comprehensive reporting to track failure and non-compliance from start to finish.
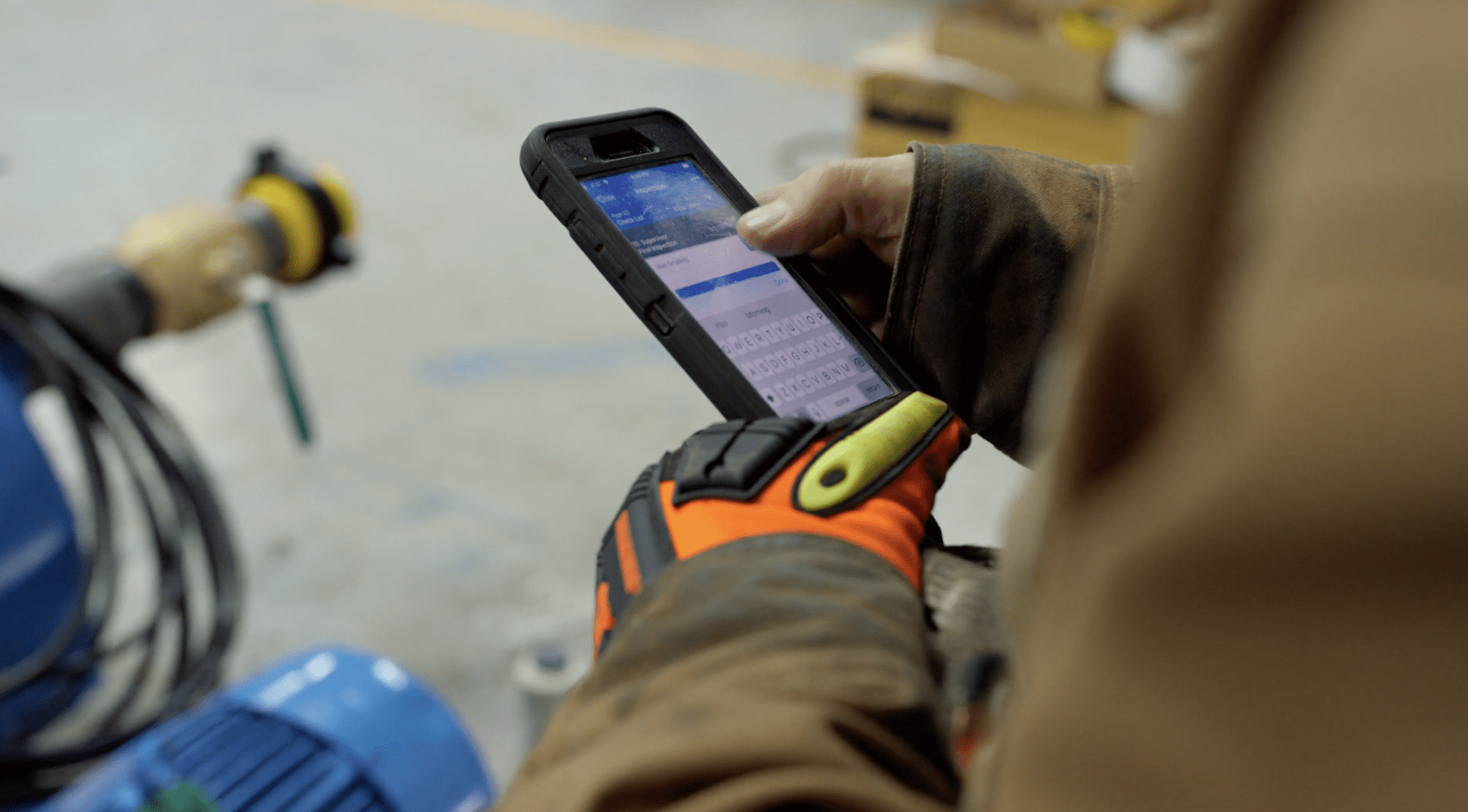
How ad-hoc data revolutionized incident reporting at BOS Solutions
BOS Solutions were experiencing delays in response times when incidents occurred at their many remote locations. Careful case management at the time of incident is crucial to the timely resolution of issues in the oil and gas industry. However, BOS lacked the workflow necessary to investigate incidents, resolve failures, and take corrective action to prevent future occurrences. Consequently, employees had stopped reporting issues because they couldn’t see how their reports would drive change or make their workplace safer.
To address these critical operational issues, BOS digitized their processes using iAuditor. The BOS team set up a comprehensive workflow for reporting incidents and observations in the field. Every employee now has the ability to log issues quickly using their mobile device.
Since switching to iAuditor, BOS workers can now share incident data including photos instantly. Then, within hours of the event, an investigation can be completed with full visibility of the steps that occurred throughout the investigation. Finally, iAuditor captures the resolution to ensure that the same issue won’t occur again.
iAuditor has allowed BOS to empower employees and develop a culture of safety and accountability throughout their business that results in faster incident response.
Prevent failures before they happen with continuous data
Understand your business like never before with continuous data collection. Capture streams of data from sensors on your equipment and throughout your environment to develop a baseline for normal operations. Then, set up automatic alerts to quickly notify team members when anything falls outside of the set range. Prevent revenue-impacting, critical failures before they occur by listening to the early warning signals. SafetyCulture Sensors will let you know when something isn’t right and allow you the time to address it.
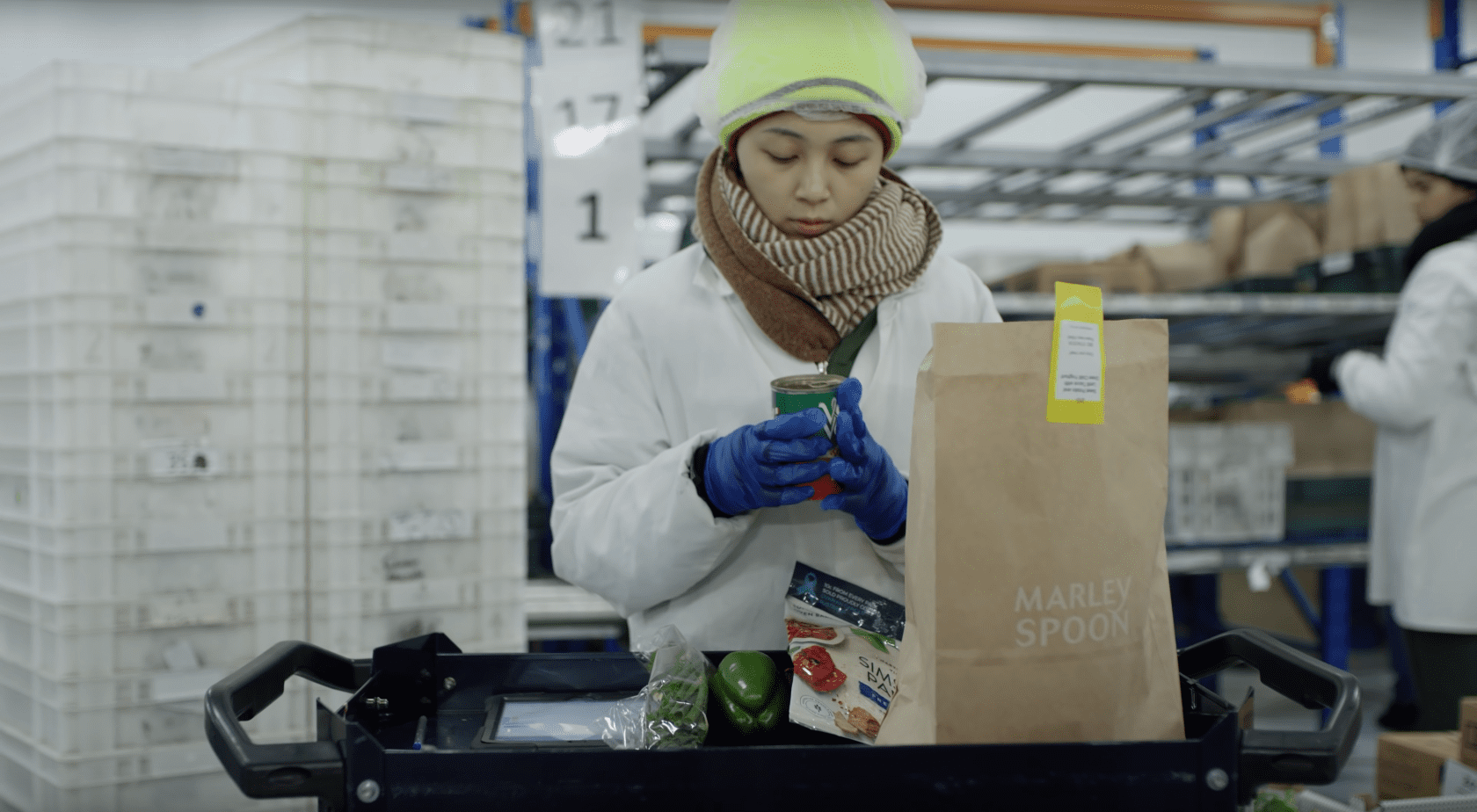
How continuous data saved Marley Spoon
Meal delivery service, Marley Spoon, faces the immense challenge of maintaining food quality and customer satisfaction for thousands of meals delivered to Australian homes every week. The risk of inventory loss from equipment failure or environmental conditions is extremely high at $200,000 to $300,000 for a single day of production.
In the past, manual routine cold room checks were completed to monitor temperature levels. Now, Marley Spoon has integrated SafetyCulture Sensors to automate the monitoring process and prevent failure and inventory loss before it happens.
One weekend, a cold room door wasn’t closed properly in the Marley Spoon production facility. Temperatures started rising and the SafetyCulture Sensors triggered an instant alert. The team sent someone to the facility to immediately close the door. If the problem had been discovered on Monday – it would have been too late. The inventory would have spoiled, resulting in a significant loss.
SafetyCulture Sensors have helped Marley Spoon deliver exceptional quality to their customers, while reducing staff hours, and providing the team with increased peace of mind.
Is your data driving action or sitting in silos?
Connected data alone isn’t enough to allow organizations to quickly respond to incidents, take decisive action, and prevent catastrophic failure. The competitive advantage delivered by enhanced visibility is entirely dependent upon the way that data is used. Organizations need tools that drive action to automate their response and workflow once incidents occur. When a hazard is reported or a change in operating temperature detected, relevant team members must be notified immediately, so that issue can be resolved fast.Learn more about how iAuditor can help empower your team with digital inspections, automate your incident response, and turn your sensors data into action today.
Important Notice
The information contained in this article is general in nature and you should consider whether the information is appropriate to your specific needs. Legal and other matters referred to in this article are based on our interpretation of laws existing at the time and should not be relied on in place of professional advice. We are not responsible for the content of any site owned by a third party that may be linked to this article. SafetyCulture disclaims all liability (except for any liability which by law cannot be excluded) for any error, inaccuracy, or omission from the information contained in this article, any site linked to this article, and any loss or damage suffered by any person directly or indirectly through relying on this information.