Quality is an investment, not a cost
Ask The Experts | Feedback From The Field | By | 9 Sep 2022 | 6 minute read
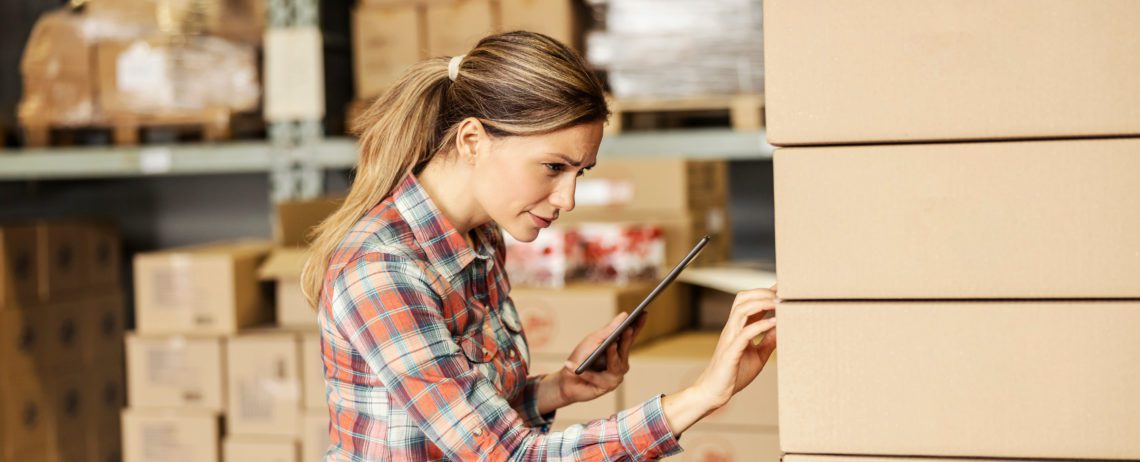
There are a few universal phrases in this world that will instinctively cause people to flinch or scatter the moment they are uttered. Yell “Heads up” to a group of parents at a kid’s softball game and watch them duck and cover. Similarly, anyone who grew up playing in the street with their friends as I did would bolt for the sidewalk as soon as someone exclaimed, “Car!”
Unfortunately, such is the case on a jobsite when you hear the dreaded words, “The Quality Inspector is here.” In fact, people tend to both flinch and scatter. Questions race through their minds such as:
- “Am I wearing my PPE?
- “Is the jobsite neat and clean?”
- “Am I doing what I’m supposed to be doing?”
- “Where are my prints?”
This Pavlovian response is not totally without justification as it has been conditioned into them over years of scrutiny and interrogation.
Perception is reality: Perspectives on quality management
During the years I have spent in the quality space, particularly in construction, I have met every type of quality professional there is.
There’s the young engineer fresh out of college, afraid they will not be taken seriously because of their lack of practical experience. Then, there’s the former field worker whose knees and back cannot handle the grind anymore and, instead, has switched to mentoring and teaching the next generation of workers. Lastly, you’ll have the certified quality professional with a bunch of letters after their name in their email signature. The list goes on.
None of these are inherently good or bad on their own. After all, each of them is quickly recognized by the frontline workers when in the field. Once they get over the mild panic of having them show up on the job site, their next thought is usually something about how much time is about to be wasted fixing something that is not really broken or explaining why things were done the way they were.
This primarily happens because of the common perception that the quality professional’s job is to find something wrong. Let’s face it, If they cannot find any defect or weakness, what do we need them for?
I had a colleague working in a township that had an inspector who, without exception, had to find a defect on every inspection. This person would not leave until there was something to report.
Once my colleague figured this out, upon the inspector’s arrival, he would place a ladder under a ceiling tile that just happened to have a cable with a loose connection above it. The inspector would climb the ladder, pop the tile, jiggle the connection, and write up the deficiency. Then, my colleague would tighten the connection, replace the tile, and everyone was happy.
Was it productive? No.
Helpful? Nope.
Normal? Unfortunately.
Quality management in practice: from policing to support
In my first job as a project-assigned quality manager, I had little appreciation for the situation I was about to get myself into. There were a couple of things working against me:
- I did not have any experience with the type of work they were performing. How was I supposed to know if things were being done right if I did not know what right was?
- I did not know any of the people, so I had no one to lean on for support and guidance. At least I had a bunch of letters in my email signature that impressed a total of nobody on the project team.
Needless to say, I was more than a little nervous. I knew the “fake it until you make it” approach would not fool anyone, and I needed to prove my worth to the team and the customer.
I did have a few things working in my favor, though. It has been said that your greatest strength is also your greatest weakness. Well, it turns out the opposite can be true as well. My greatest weaknesses turned out to set me up for success.
Lucky for me, the bar was pretty low for quality managers on this job, and people did not expect much to begin with. The quality manager I was replacing had more of a quality cop approach than a supportive role, so in the eyes of the project team, at least I was not that guy. And the fact that I did not know the work, or the people, caused me to be humble, ask a lot of questions and work hard to build relationships.
It forced me out of my comfort zone but paid off tremendously in the end because, as luck would have it, the people on the team loved sharing their knowledge and experience with anyone who would listen. They saw me as someone eager to learn, interested in what they had to say, and, most importantly, as a part of the team—not the quality cop.
Key learnings in quality management for continuous improvement
It is important to note that the certificate I earned that enabled me to add all those cool letters to my email signature taught me some indispensable lessons about customer value, process flow, waste, and respect for people. Through this experience, I have learned the following things:
On approaching defects
First, quality should not depend on inspections to find defects, like our friend with the ceiling tile. Deficiencies need to be prevented so that production can continue to flow and deliver value to the customer without having to stop to do rework.
On inspections
If you must rely on inspections, they should be performed as soon as possible after the work is completed to avoid any repetition of defects.
On the role of quality inspectors
The quality inspector can add value to the project team by working with them to reduce rework, avoid go-backs and eliminate defects. They can do this by preventing them from happening in the first place, not by catching them after the fact.
Fighting false narratives: quality as a worthwhile investment
There is a difference between data and information. Data are just numbers, like dollar amounts and project hours. On the other hand, information uses data to tell a story. That story is used to draw conclusions.
Sometimes we have poor quality data and tell the wrong story. Other times, we have good data and draw the wrong conclusions. To illustrate this, consider the following scenarios:
Scenario 1
There was $100,000 worth of rework on this project (data). Since the quality inspector did an excellent job by catching it (information), it means that we need more quality inspectors (conclusion).
Scenario 2
There was only $2,000 worth of rework on this project (data), which is more than we paid our quality inspector to find the defects that caused it in the first place (information). For this reason, we have concluded that the quality manager wasn’t worth the cost (conclusion).
The logic in both these cases is severely flawed. Imagine if we were talking about safety and said, “No one got hurt on this job; therefore, we did not need the safety manager.”
No one would ever say that, yet quality personnel is still perceived as a cost, not an investment. As a result, they feel the need to find problems in order to justify their role, and the vicious cycle continues.
Lessons not learned: The challenge for quality improvement
Upon looking at the previous section, one thing remains clear: to tell the right story and draw logical conclusions, there needs to be good data. Everything relies on accurate, efficient, and unbiased data collection. The right questions need to be asked and answered in a manner that allows for effective root cause analysis.
Once the actual cause-and-effect relationship is established, action needs to be taken to prevent the problem from happening again. This action needs to take place in as close to real-time as possible. However, this sense of urgency doesn’t reflect in practice.
Too often, teams wait until a project is completed to perform a “Lessons Learned” session on what went well and what did not. With proper quality improvement tools, data quality checks, and processes, this can be performed frequently throughout the lifecycle of a project. This way, the job can benefit from lessons learned as you go, instead of waiting until the next job to do something about it. “
How often have you had conversations like, “Well, on the last three jobs, we had this problem, so let’s do XYZ to prevent it this time?” But to turn this topic on its head, my question would be, “If the problem has persisted for so long, was the lesson ever really learned?”
Too much time passes, project teams break up, and new jobs are starting too fast to take the time to look back at what happened. Given these fast-paced changes, this all needs to be done in real-time to effect any meaningful change.
Changing the narrative: A new outlook on quality in organizations
My experience as a quality manager on that job was far from perfect. I do not want to give the impression that I showed up on the project and everything was magically better. We still had rework, and some of it was expensive and avoidable. But we got better as the project progressed, for we learned from our mistakes and did our best not to repeat them.
By working as a team to avoid defects, celebrating our relatively low percentage of rework costs, and using that data to tell the right story to management, we began to shift the perception from quality as a cost and started to see it for what it truly is—an investment with extremely high returns.
Important Notice
The information contained in this article is general in nature and you should consider whether the information is appropriate to your specific needs. Legal and other matters referred to in this article are based on our interpretation of laws existing at the time and should not be relied on in place of professional advice. We are not responsible for the content of any site owned by a third party that may be linked to this article. SafetyCulture disclaims all liability (except for any liability which by law cannot be excluded) for any error, inaccuracy, or omission from the information contained in this article, any site linked to this article, and any loss or damage suffered by any person directly or indirectly through relying on this information.