The rise of Improvement Specialists: A new era on the frontline
Feedback From The Field | World Of Work | By | 28 Nov 2024 | 4 minute read
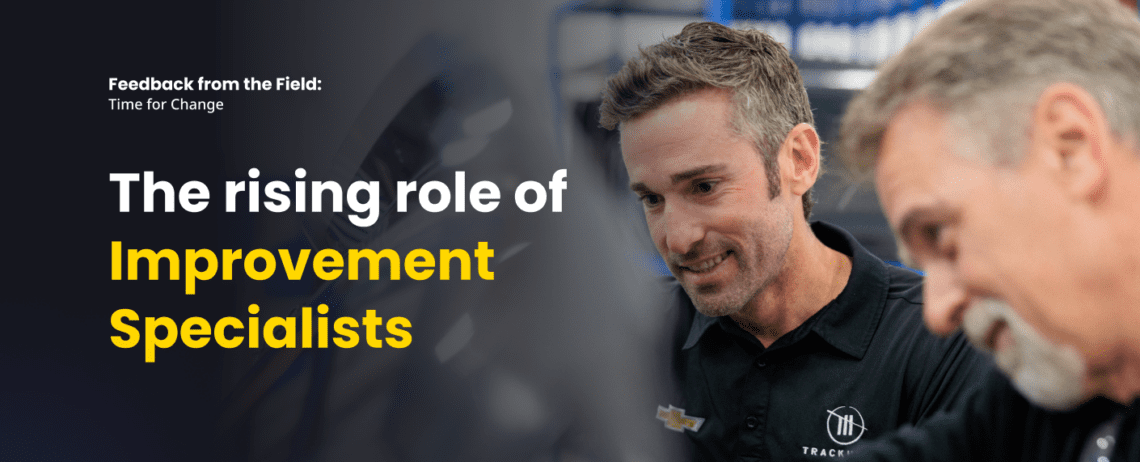
Do you notice an âus versus themâ divide at work? If so, youâre not alone. Our recent Feedback from the Field study revealed that 52% of frontline workers feel the same.
This disconnect between frontline employees and management can hurt performance and hold back progress. But thereâs good newsâa new type of workplace change-maker is emerging to bridge the gap. Enter the Improvement Specialist.
Improvement Specialists have a talent for spotting opportunities for changeâwhether by digitizing manual processes, enhancing communication, or ensuring prompt action on reported issues. They aren’t restricted to a job title or confined to Health, Safety, and Quality (HSQ) roles; being an Improvement Specialist is a mindset.
SafetyCulture Feedback from the Field Report, 2024
Whatâs blocking continuous improvement?
Alarmingly, 38% of people said that continuous improvementâwhere everyone can contribute to better processesâis discouraged in their organization. For those in HSQ roles, this number rises to 56%.
Despite companies wanting safer, more efficient workplaces, many employees donât feel supported enough to speak up or take charge. They often believe their feedback goes unheard or worry about the repercussions of sharing ideas. These barriers restrict open communication, and decision-makers are less likely to know where to focus their time and efforts.
Our Feedback from the Field report reveals a growing need for Improvement Specialists. Improvement Specialists use their experience and in-depth organizational knowledge to bridge this divide. By creating systems where teams can openly share feedback and ensuring frontline insights reach management, they foster better communication across the board.
How Improvement Specialists can drive change
To improve relationships between frontline employees and management, Improvement Specialists find ways to:
- create feedback loops
- actively develop psychological safety
- support collaboration.
Hereâs a closer look at how these strategies come to life, supported by our research and real-world examples that can apply to any industry.
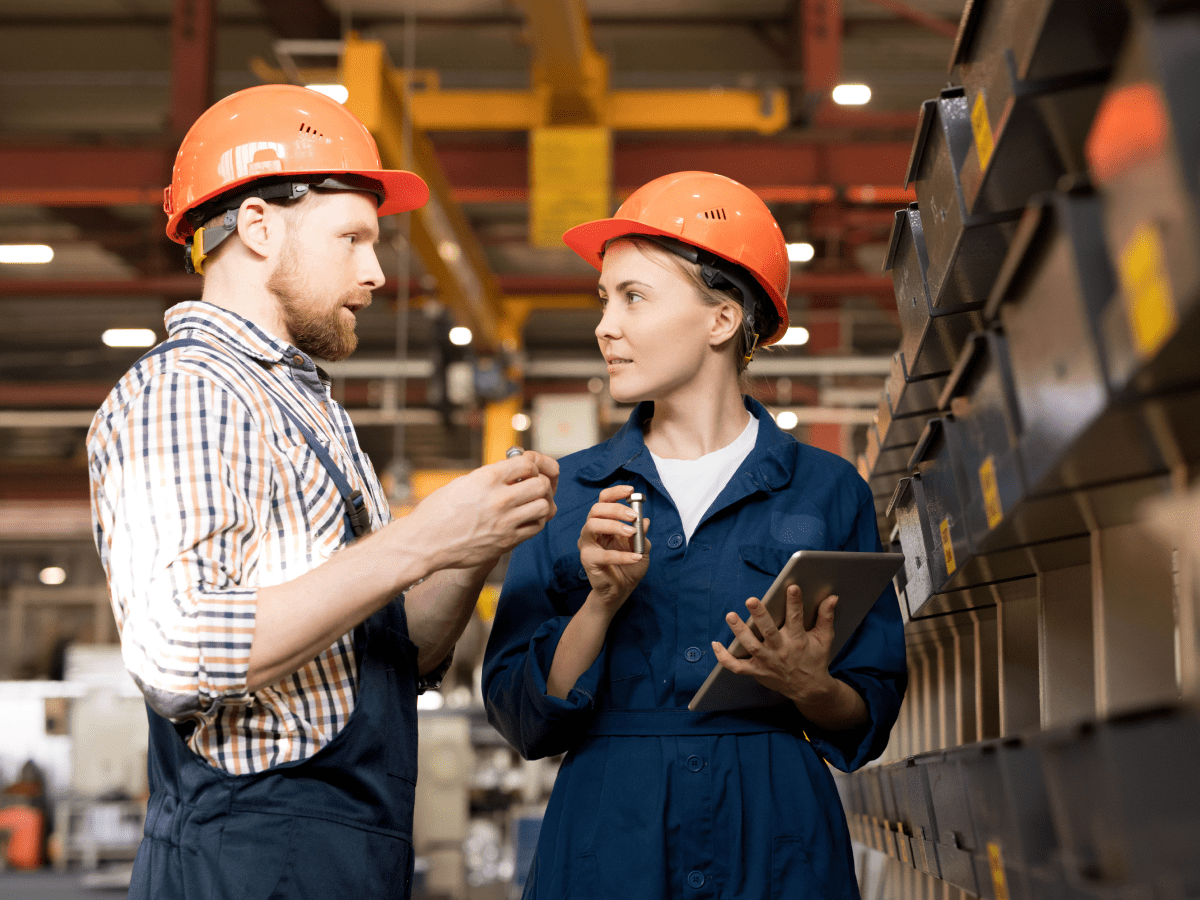
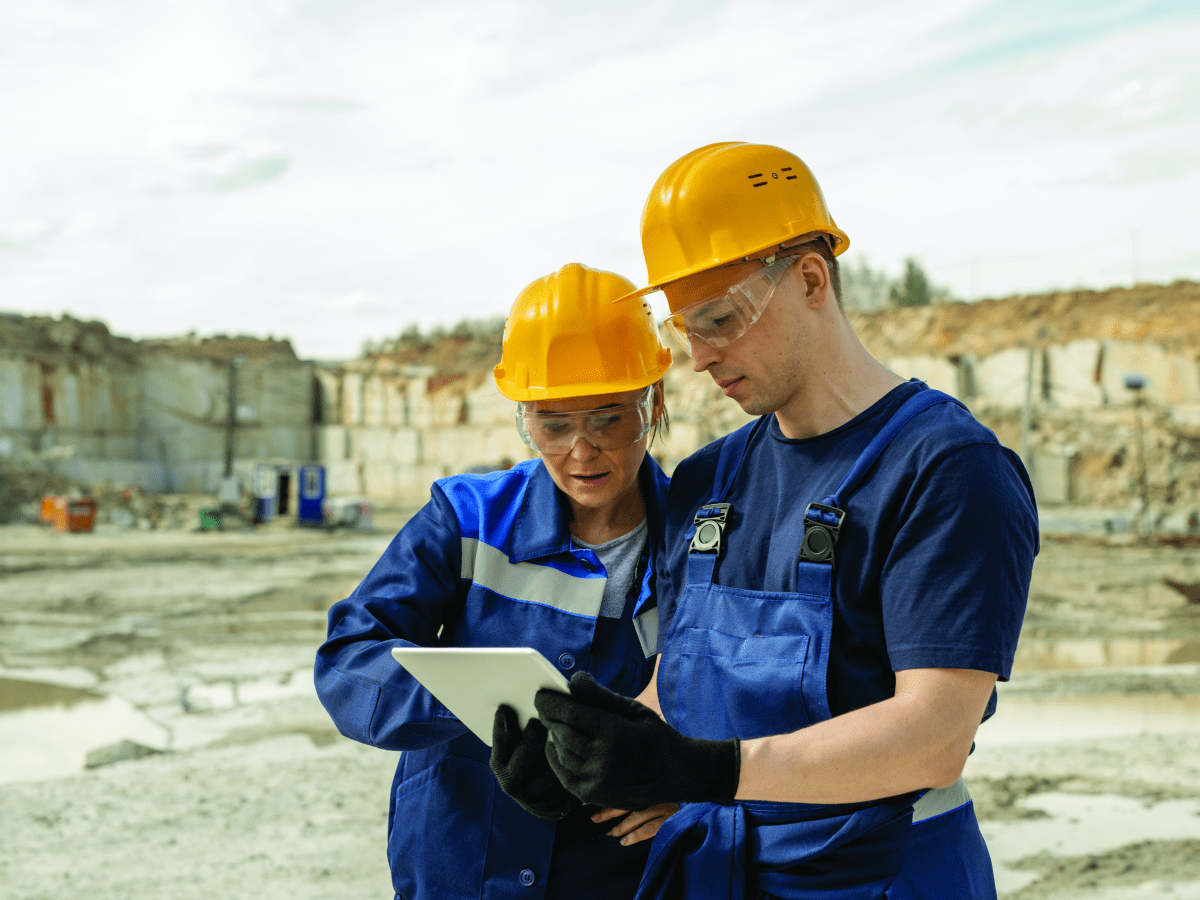
Creating feedback loops
Many frontline employees feel their insights arenât fully captured or valued.
Workers who are aware of HSQ leaders in their organization and believe they could be more valuable say this could be achieved by providing assurance that feedback will be heard and actioned (39%).
Although his formal title is Chief Risk Officer, Mark Murphy is an Improvement Specialist at Donaldson Group. He established a feedback loop using SafetyCultureâs Inspections feature. By digitizing audits, Mark enabled his construction teams to capture insights instantly so managers could address risks faster.
âFrontline colleagues can see when somethingâs not right, and usually have ideas on how to improve it,â says Mark. âIt is actually easier and quicker than paper audits. We can directly add photos and assign Actions. Before, the inspectionsâ data was analyzed between six to seven weeks later. Now, with the SafetyCulture platform, all that information gets pulled out of the audits daily. The senior management teams can simply dial in and view the dashboards with the key data.â
Improvement Specialists like Mark ensure that feedback flows seamlessly from the floor to management, bridging communication gaps and ensuring feedback is seen and actioned.
Making it safe to speak up
Psychological safety is essential for open feedback. Improvement Specialists lead the charge in building workplaces where open communication is encouraged at every level. Our research offers insight into how to make it happen.
Workers who are aware of HSQ leaders in their organization, and believe they could be more valuable, say this could be achieved by encouraging improvements through positive reinforcement rather than fear (36%), and giving assurance that feedback will be handled confidentially (32%).
DB Schenker, a global logistics leader, implemented SafetyCultureâs Heads Up feature to ensure everyone had access to important messages. At first, some frontline employees were hesitant about this new way of working, but once they experienced the tailored messages first-hand, they started openly sharing safety issues and operational insights. Implementing SafetyCulture helped build transparency and reinforced trust across the organization, making employees feel safe to voice their opinions.
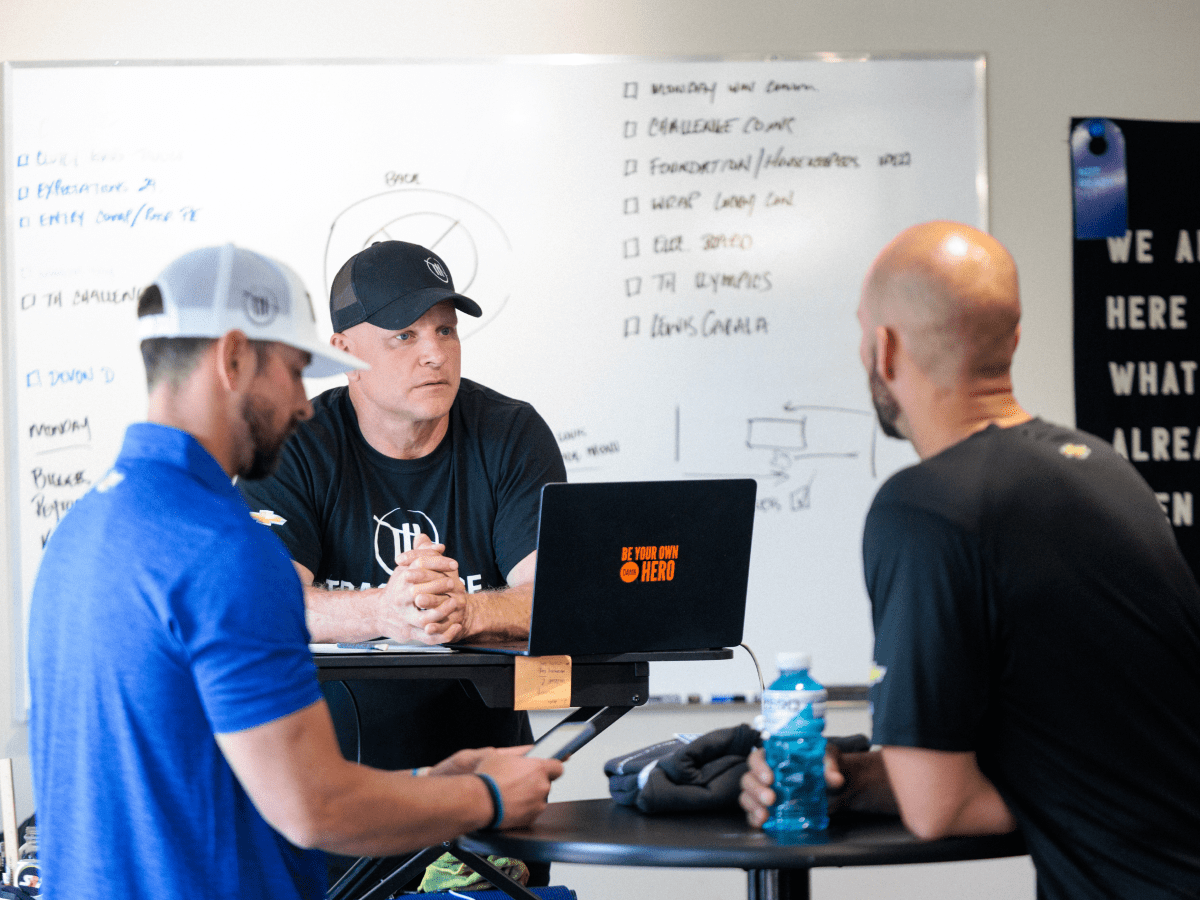
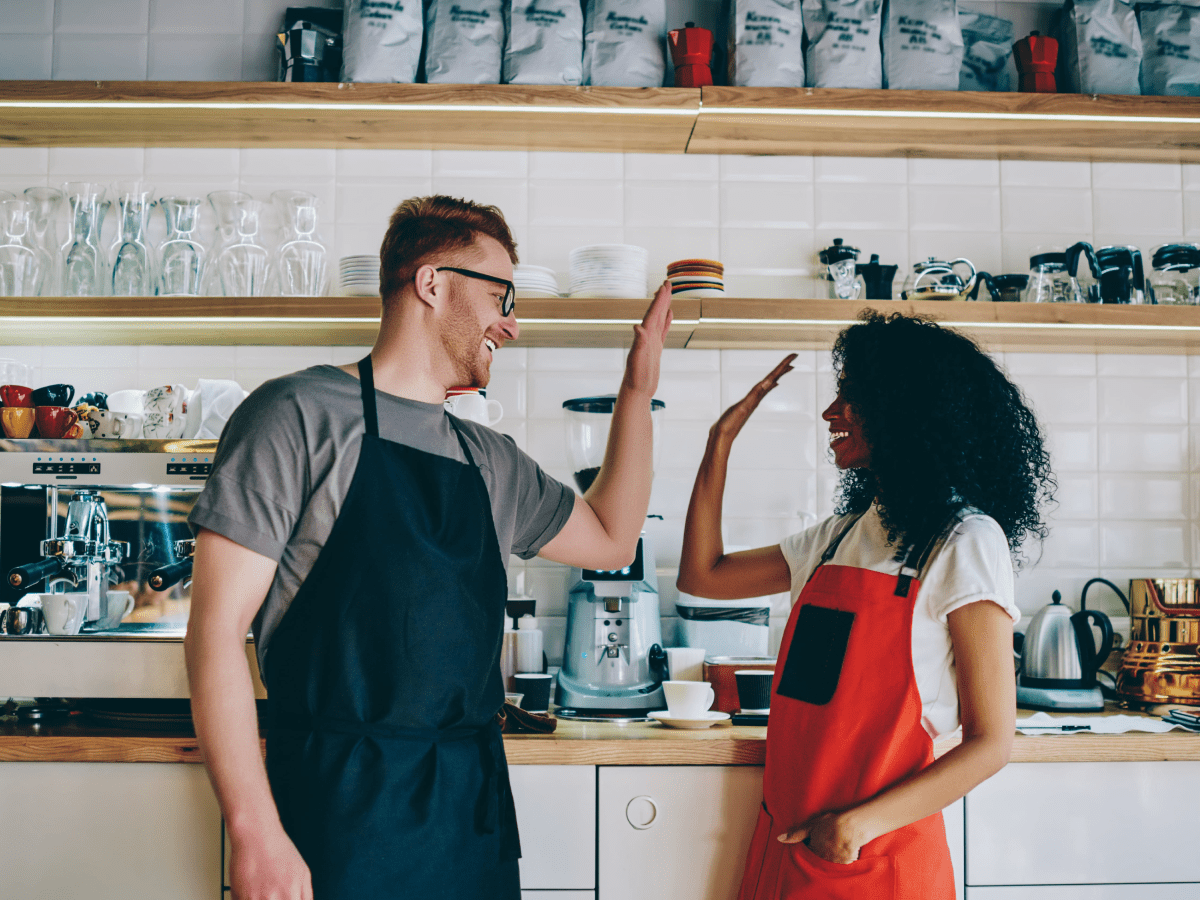
Strengthening team collaboration
Improvement Specialists can bridge communication gaps between management and frontline workers by creating and championing better ways of working.
93% of workers believe the relationship between frontline employees and managers could be improved, with 46% saying more regular communication could help.
Anna Giusti is an Improvement Specialist at MOWI. She customized SafetyCultureâs Inspection template to match production line processes. Anna sought detailed feedback from frontline workers and management before rolling out the new system. The result? Streamlined inspections that saved hours each week and a team who felt proud of their contribution to the better way of working.
âI didn’t stop testing until everybody was happy with the template. Sometimes things get lost in translation between managers and the frontline, so itâs important to keep the end user in mind,â Anna shares.
âEveryone was really happy with the level of detail and could see how much time it could save.â Her experience shows how better communication between frontline workers and management can lead to lasting improvements and a collaborative team culture.
Boosting the visibility of Improvement Specialists
Cultural shifts can take time. Improvement Specialists may need to build networks of like-minded industry leaders, so they have new avenues to educate others about how they can help. Visibility and engagement are key to gaining support and making a difference. Here are a few tips for emerging Improvement Specialists:
- Engage with frontline teams: Build trust by participating in team huddles, safety meetings, and training sessions.
- Encourage feedback loops: Hold regular sessions with workers and managers to ensure new processes work for everyone.
Use data to communicate progress and results: Platforms like SafetyCulture track metrics like inspection rates and reported issues, making it easy to highlight the positive impact of improvements. Sharing real-time dashboards or reports showcases results and builds support.
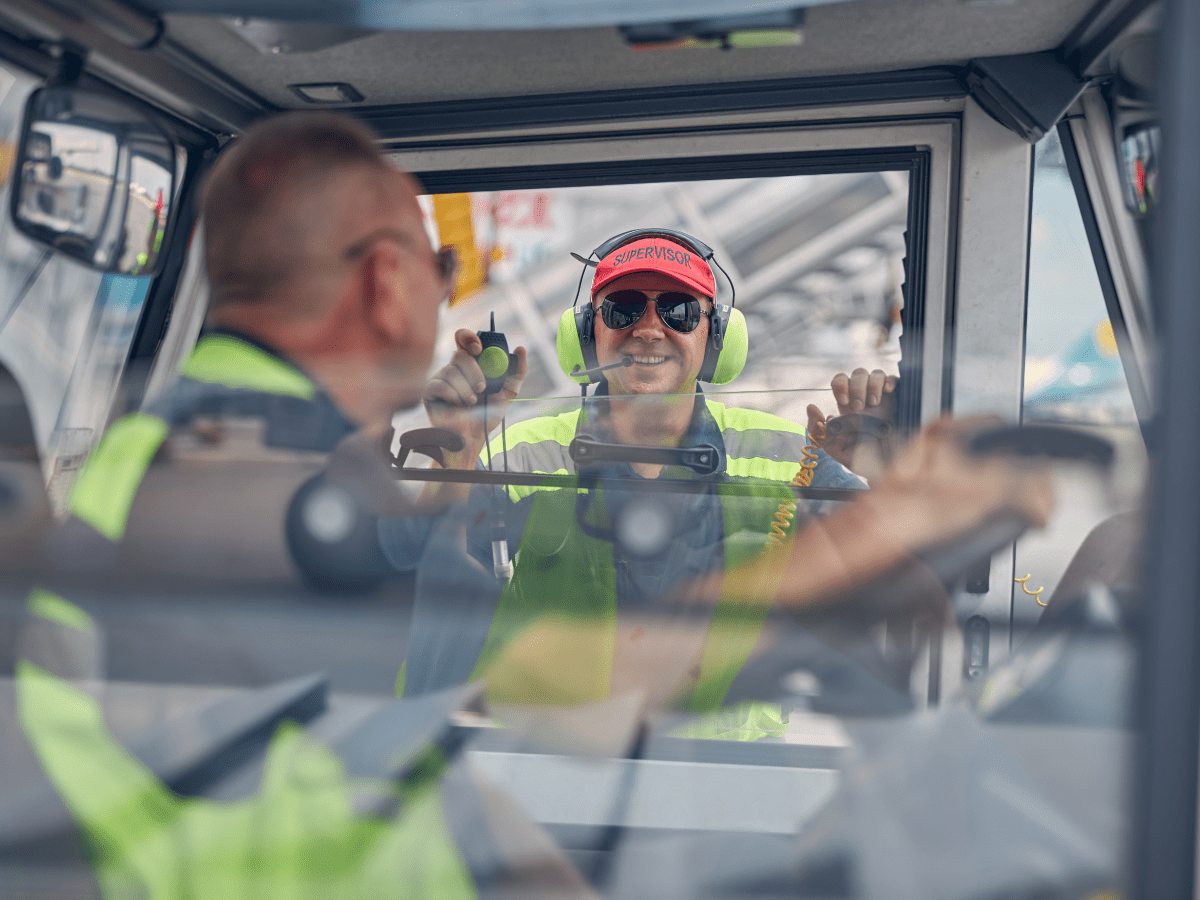
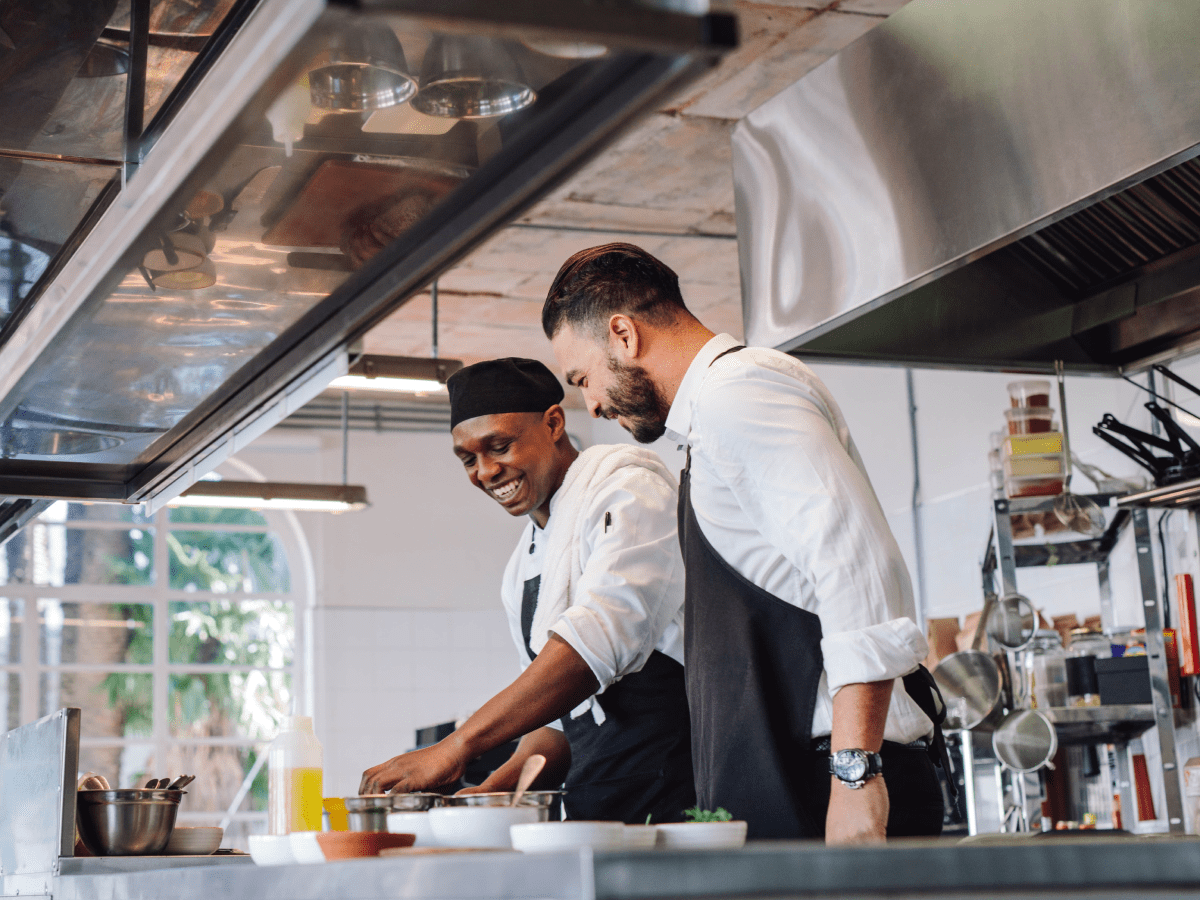
A new era in workplace improvements
Our global frontline worker survey uncovered an emerging role thatâs paving the way for more cohesive, efficient, and engaged workplaces. The rise of the Improvement Specialist reflects a new era in frontline leadershipâone where every worker feels heard, valued, and empowered to contribute to a culture of improvement for meaningful, lasting progress.
If youâd like to give your team the tools to become Improvement Specialists and create a culture of continuous improvement, book a SafetyCulture demo today. See how our platform can help your organization capture feedback, boost collaboration, and achieve lasting improvements.
About the research
Feedback from the Field is an annual report that aims to give businesses deeper insights into their workforce and help uncover opportunities for operational improvement. All figures, unless otherwise stated, are from YouGov. The total sample size was 10,121 adults (2023 UK, 2087 US, 2010 Australia, 2003 Germany, 1504 France, 501 Ireland). Fieldwork was undertaken from July to August 2024. The survey was carried out online.
Read more Feedback from the Field articles
- How to improve employee-manager relationships: Pay, recognition and communication
- Speaking up and taking action: How to empower frontline workers
- Insights from our global frontline worker survey on productivity, AI, and workforce challenges
Important Notice
The information contained in this article is general in nature and you should consider whether the information is appropriate to your specific needs. Legal and other matters referred to in this article are based on our interpretation of laws existing at the time and should not be relied on in place of professional advice. We are not responsible for the content of any site owned by a third party that may be linked to this article. SafetyCulture disclaims all liability (except for any liability which by law cannot be excluded) for any error, inaccuracy, or omission from the information contained in this article, any site linked to this article, and any loss or damage suffered by any person directly or indirectly through relying on this information.