Improvement Specialists: Who They Are and Why Your Business Needs One
World Of Work | By | 14 Feb 2025 | 4 minute read
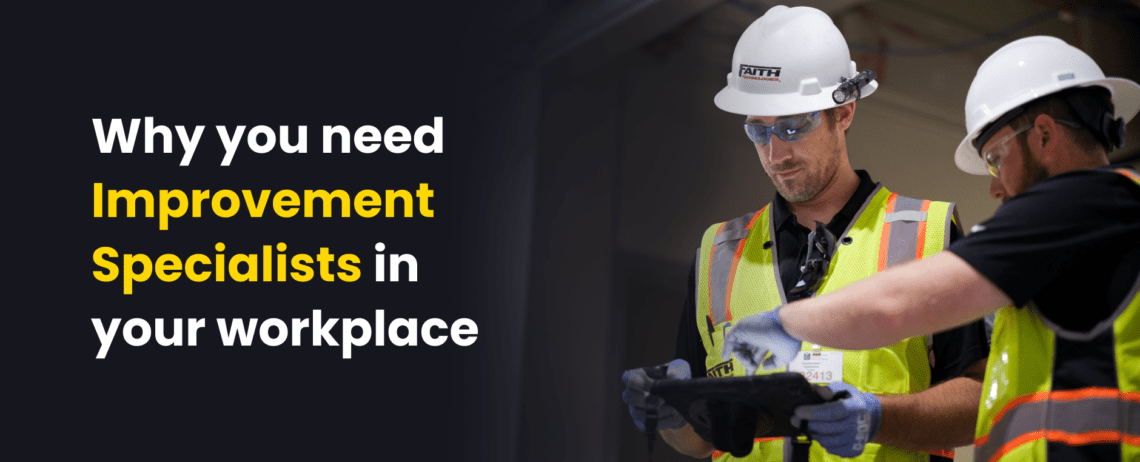
Organizations everywhere are facing a giant challenge. The world of work is evolving faster than ever, but so many companies are stuck in the mindset of “this is how we’ve always done it.”
Businesses are weighed down by rigid processes, compliance-driven routines, and a status quo begging for change.
According to our Feedback from the Field report, 78% of workers are dissatisfied with something at work, with slow response to resolving issues or risks as the leading reason. This dissatisfaction comes with a hefty price tag, costing the US economy an estimated USD $196 billion each year.
Among all of this, we’ve noticed a new type of leader emerging – the Improvement Specialist. They’re not keyboard warriors, managers, or consultants. Improvement Specialists are the passionate changemakers within your teams. They have natural skills that should be celebrated and given platforms to flex their potential.
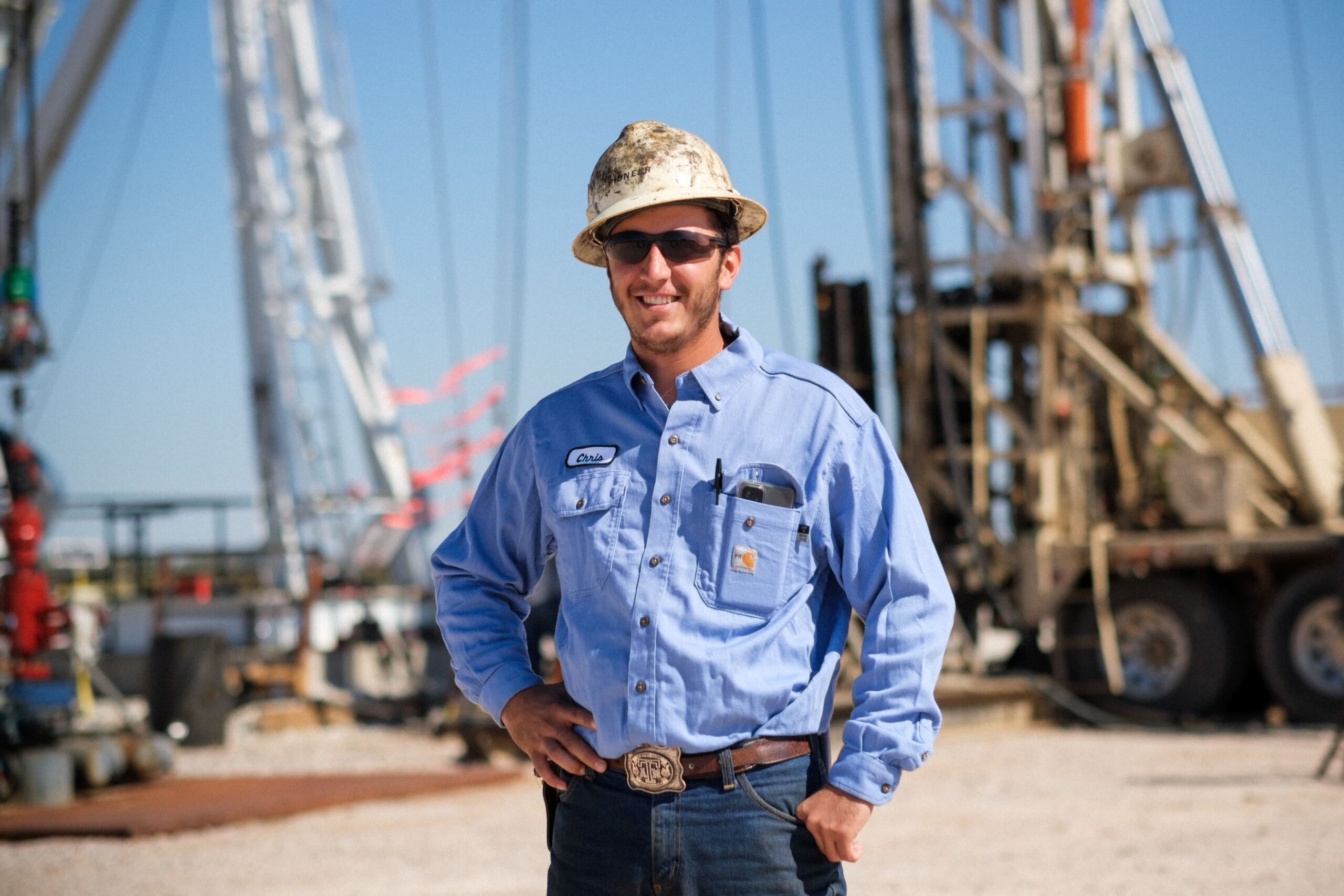
What exactly is an Improvement Specialist?
An Improvement Specialist is a proactive team member who drives efficiency, solves problems, and inspires others to achieve sustainable progress.
In many businesses, Improvement Specialists are the spark that ignites progress. Here’s what sets them apart:
- Deep operational insight: Improvement Specialists understand their organization inside and out, from systems and tools to team dynamics and customer needs.
- Proactive problem-solvers: Improvement Specialists are relentless in turning challenges into actionable solutions. They take ownership, rally teams, and embed sustainable change. Technology-first mindsets are especially valuable in industries facing high complexity and rapid change. For example, embracing cloud-based tools can transform how teams collaborate, track compliance, and manage project workflows. There are specialised digital solutions designed specifically for construction companies to streamline complex operations and enable real-time updates across project sites.
- Natural leaders: Improvement Specialists don’t wait for a promotion to make a difference. They lead by example, motivate their co-workers to improve, and take ownership and action. They bring out the best in teams, turning ideas into group achievements.
- Technology-first: Improvement Specialists use technology to establish a flow of information that connects teams. They stay current on the latest tools and platforms and how they can be used to improve ways of working consistently.
These are the skills that build a blueprint for how to transform improvements from an idea into a repeatable, scalable improvement process.
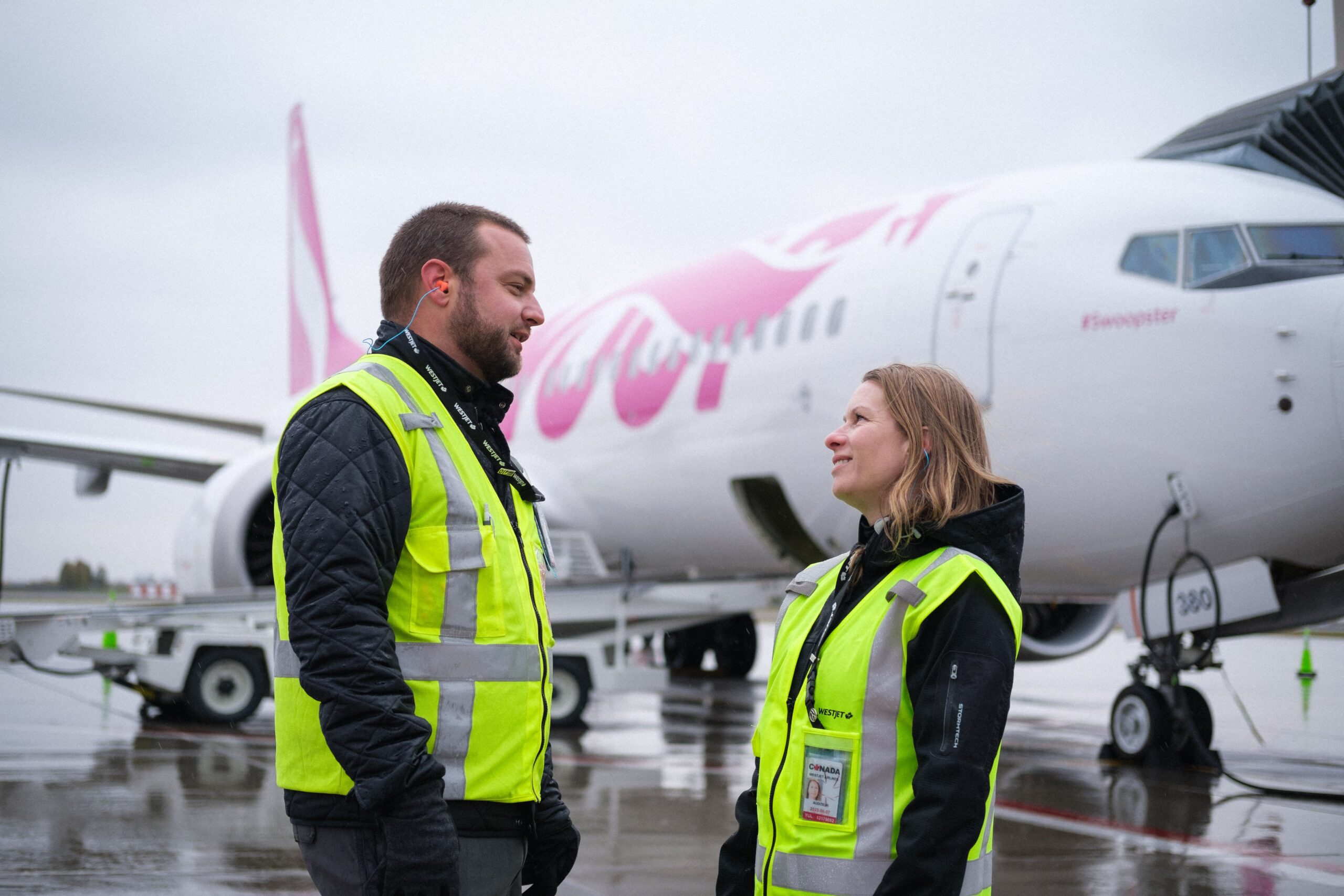
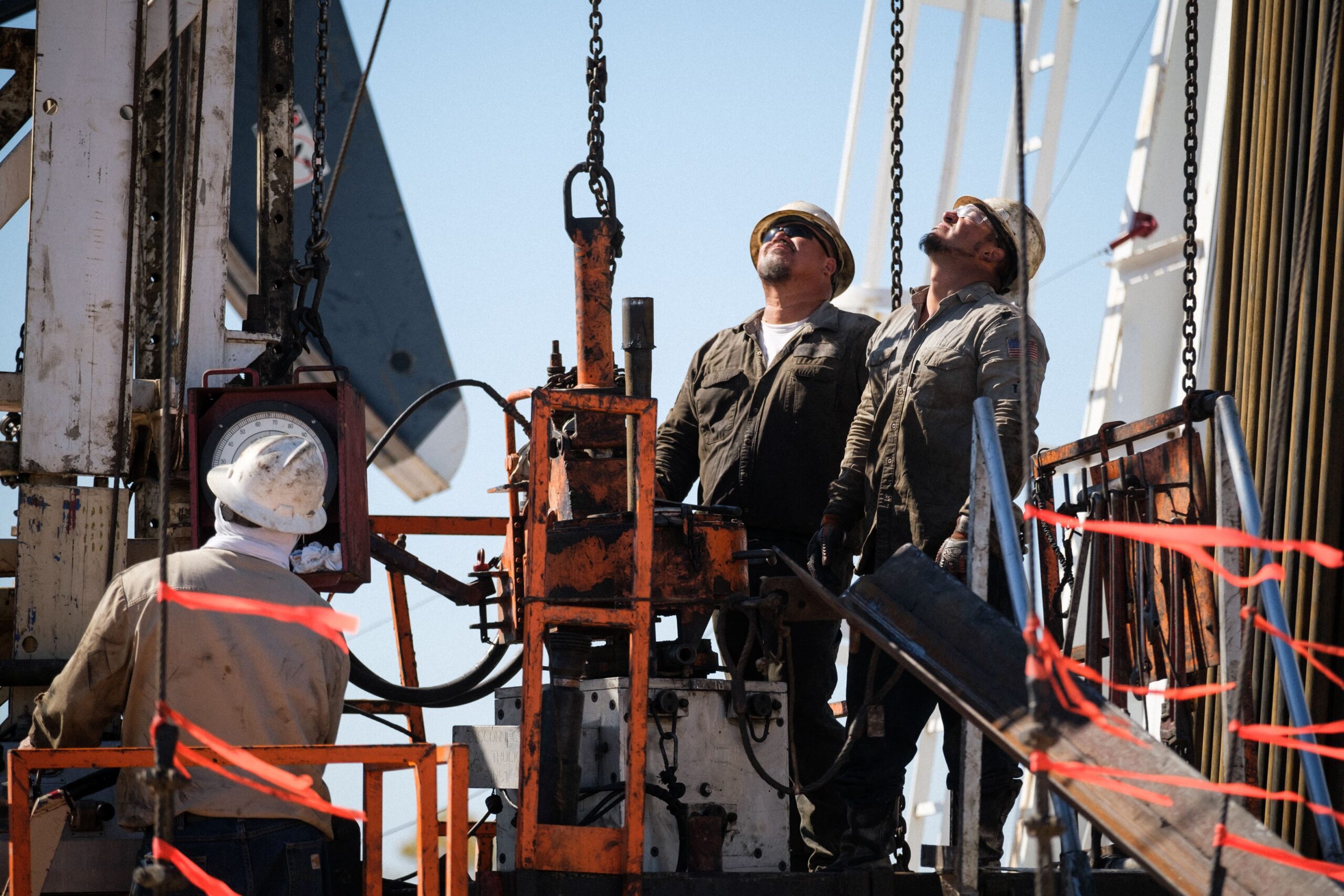
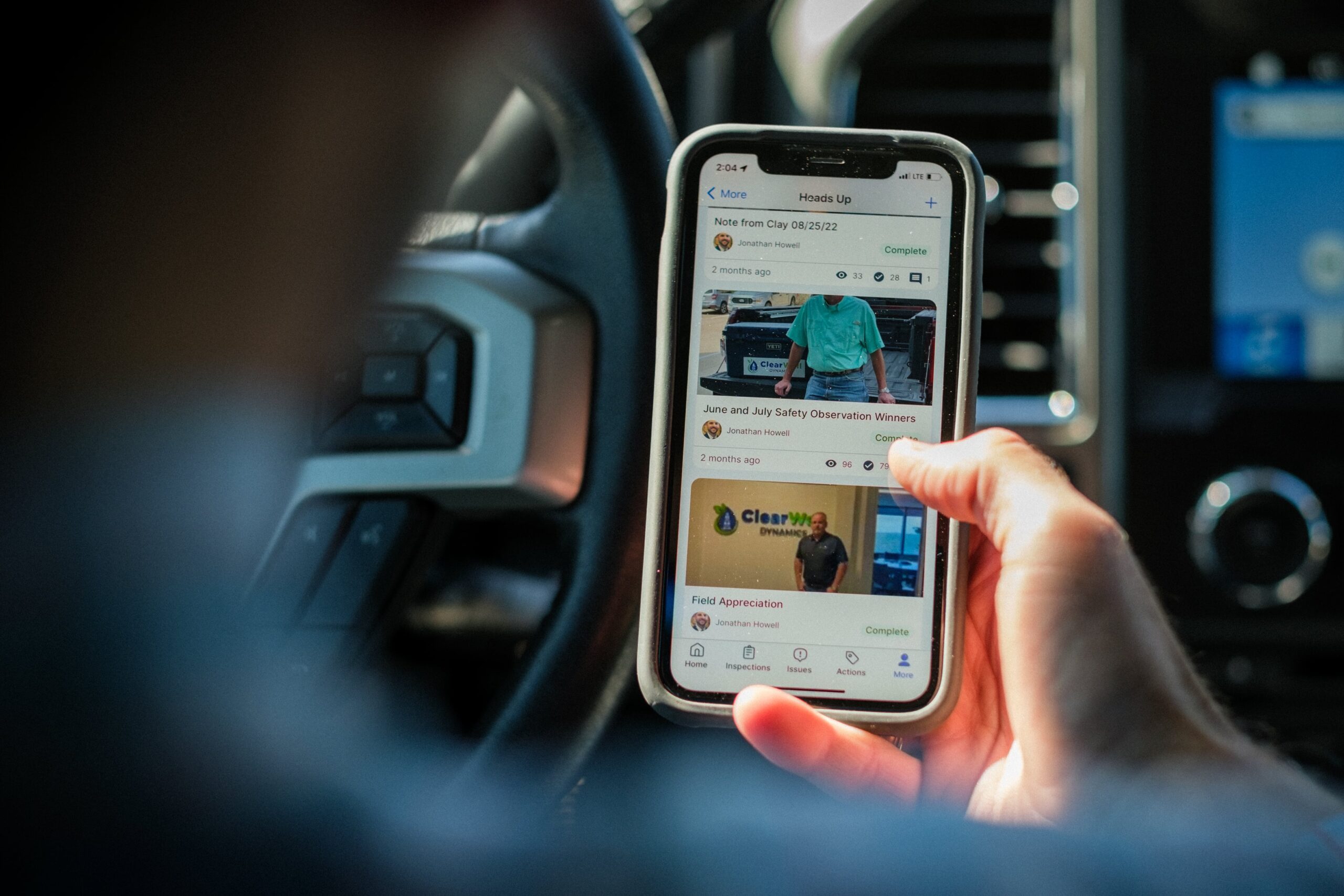
Why every organization needs Improvement Specialists
Why do Improvement Specialists matter so much? Because traditional, top-down processes don’t foster the kind of change that moves organizations forward. What sets thriving companies apart is a culture where improvement happens naturally every single day.
Take Tremco Roofing as an example. Before Ro Lewis stepped up, safety checks were supervisor-led and not collaborative. “In the past, we were pencil whipping the guys, looking for the mistakes,” says Joseph Lee, Tremco’s US Gulf states manager. “One of the biggest things I learned was how aware our guys were, but how afraid they were to say anything.”
“I was frankly tired of the antiquated way we captured information. We absolutely needed to become better,” says Ro. He knew he needed buy-in from the frontline, so he went looking for a tool that was so easy, that people would actually enjoy using it.
Ro started by enabling everyone to participate in daily task analyses (DTAs). Workers were no longer passive recipients of directives—they were active participants, sharing real-time observations and contributing to safer, more efficient workflows. “Once we started preaching that message to them that this is an empowerment tool, it just caught like wildfire,” says Ro.
Within days management became aware that workers were manually carrying 25-pound (11.5 kg) buckets up ladders. It prompted Mardee Billingsly, Vice President Tremco WTI Global Operations, to issue a company-wide statement saying that they were sorry, they had no idea that was happening, you don’t ever have to do that again, and stay tuned for new equipment and new training.
One team member even stated, “This is the first company I worked for where I know they’ve got my back. I know they listened to what we have to say.”
The result? A cycle of continuous improvement where visibility leads to action, and action leads to trust. Compliance became more than a box-ticking exercise—it evolved into a culture where every voice mattered.
“People are very smart. They will improve a process if there is a mechanism for it.” Steve Jobs
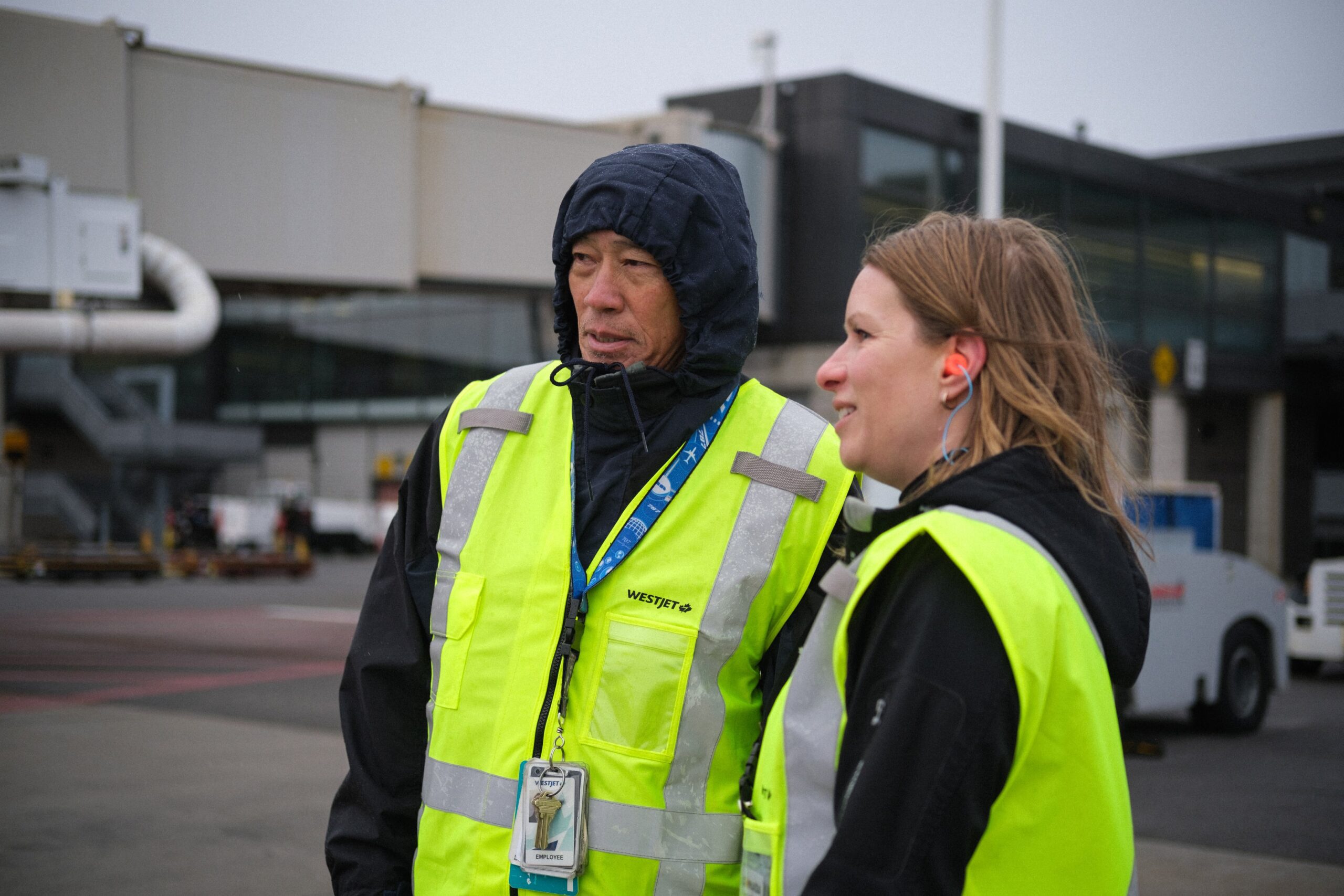
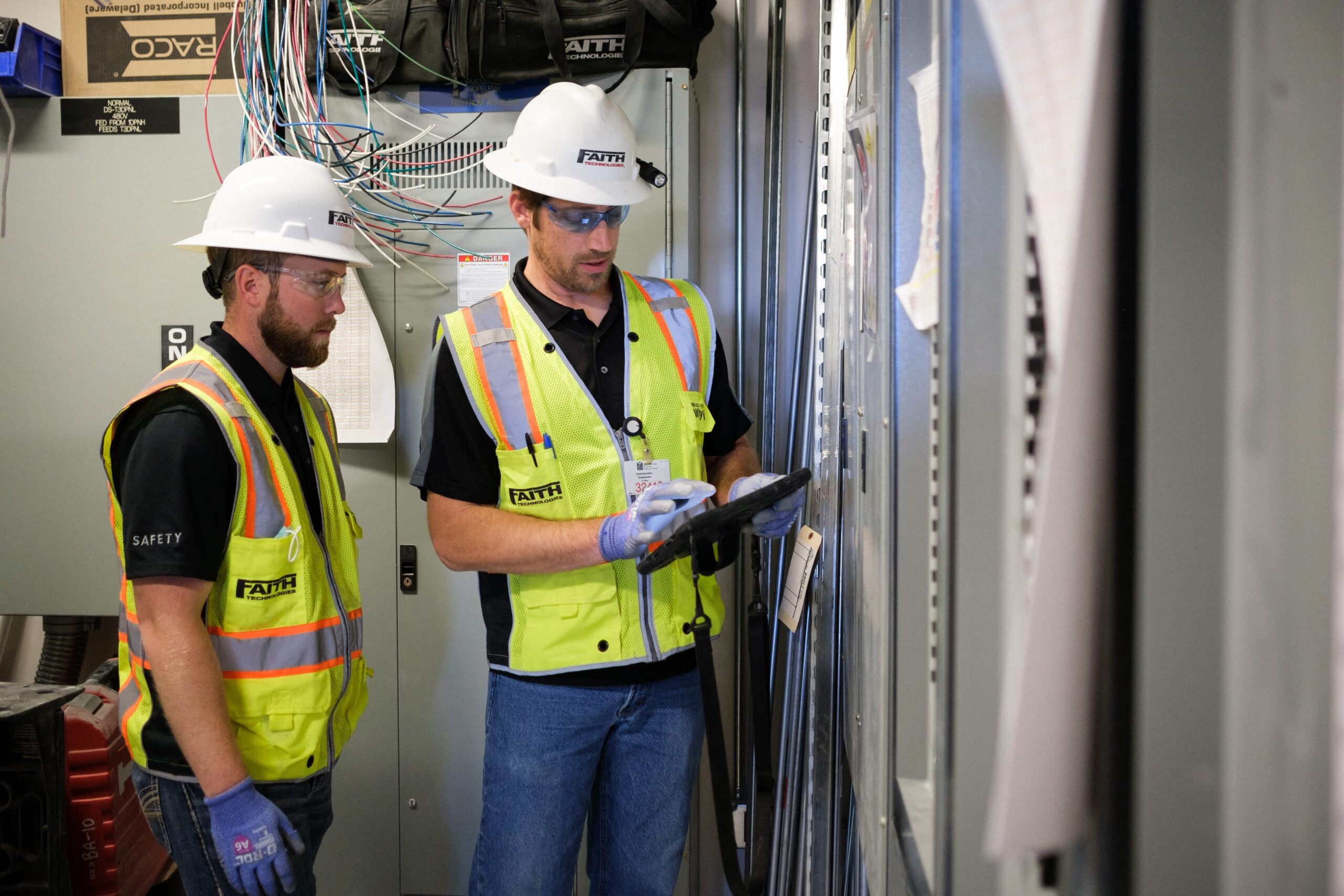
How SafetyCulture supports a new career path
The journey to becoming an Improvement Specialist benefits companies and people. Stepping up to lead change often results in personal and professional growth.
Anna’s journey from production line worker to office leader is a prime example. Frustrated by inefficient top-down processes at Mowi, she took the initiative to implement SafetyCulture and create her own templates.
When she presented her work to her manager, her career took off. No longer working in the factory freezer, Anna now enjoys a role that allows her more time with her family and the ability to pursue her passions.
Graham at Thermosash is another excellent example. Coming from a highly structured aviation industry background, Graham joined Woods Glass and quickly noticed they were “world-class scramblers and firefighters.” He led the rollout of SafetyCulture, and the change was dramatic. Frontline workers engaged more, issues were tracked and addressed, and the company saw a huge reduction in recurring problems. Graham’s passion propelled him from operations development to general management.
These stories show how Improvement Specialist mindsets can elevate teams, businesses, and careers.
Cultivating Improvement Specialists in your organization
Every organization has potential Improvement Specialists. The key is to recognize and nurture them. Here’s how:
- Identify the changemakers: Look for the employees who aren’t satisfied with “good enough” and are always finding ways to make things better.
- Offer training and certification: SafetyCulture’s free Certification Program helps employees build the skills they need to lead improvement initiatives.
- Empower through autonomy: Allow these individuals the space to experiment and take charge.
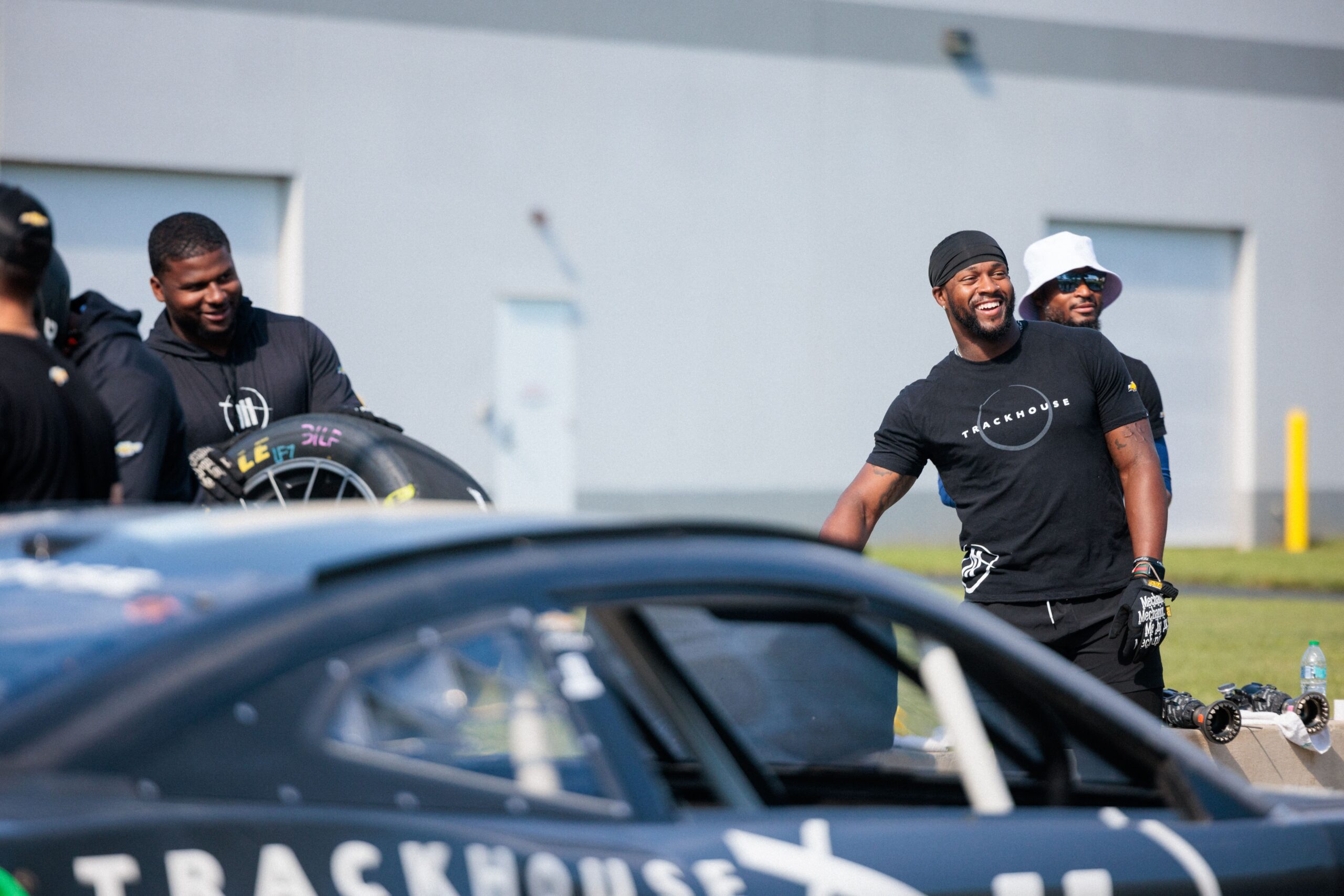
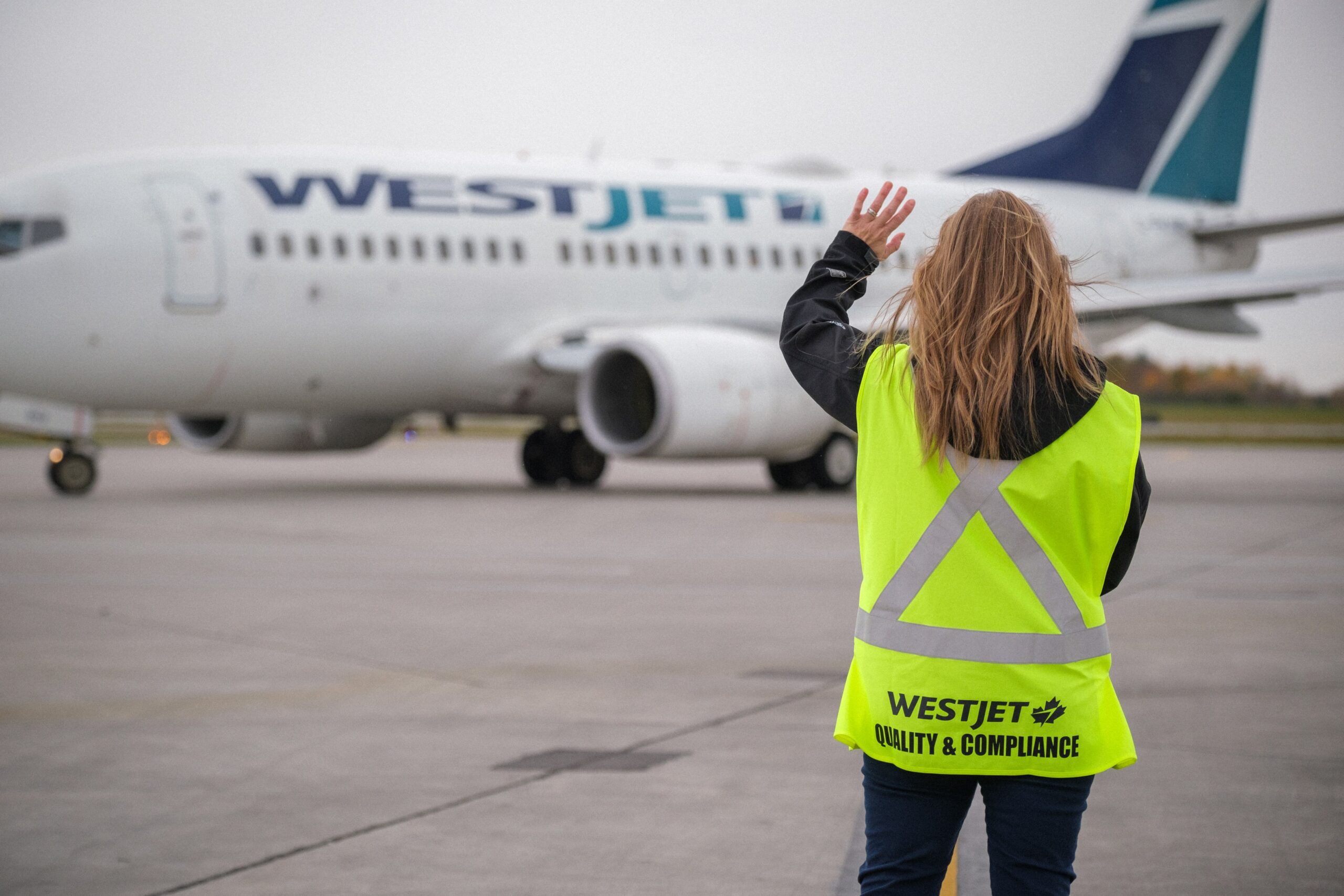
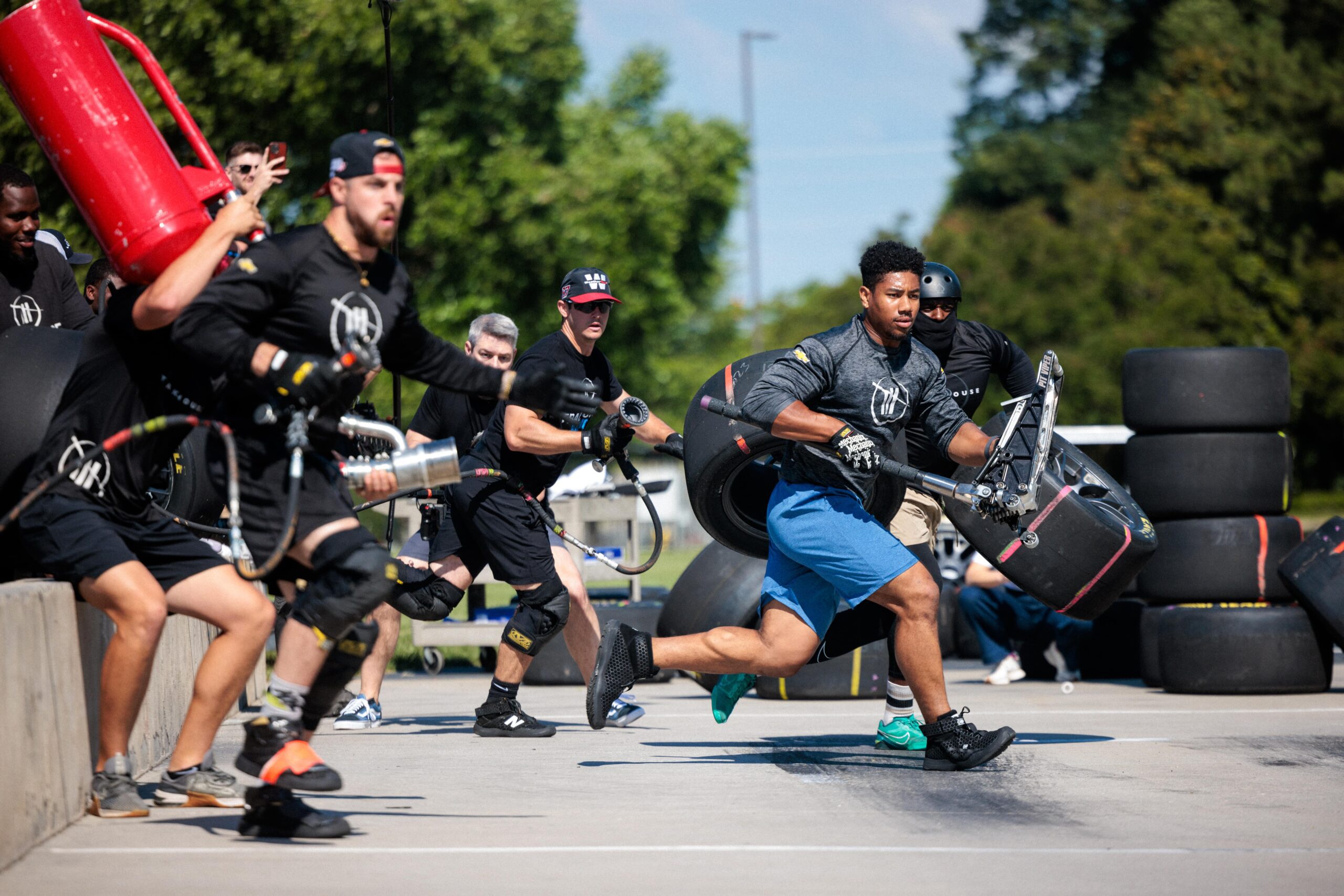
The future of continuous improvement
Continuous improvement offers a powerful framework for optimizing processes, but many initiatives can fail when it comes to execution.
Organizations often face three key challenges: lack of stakeholder support, resistance to a culture of improvement, and tools or systems that don’t evolve alongside changing needs. Even when initiatives gain momentum, they can stall due to change fatigue, low employee engagement, or a status quo mindset.
That’s why Improvement Specialists will drive the future of work. Improvement Specialists are the champions who turn daily work into extraordinary results. And their true superpower? Rallying teams around improvement, embedding change into the fabric of company culture, and ensuring progress isn’t just a one-off effort, but a continuous journey.
Imagine a workplace where every employee wakes up and asks, “What’s the most important thing I could improve today?” The answer to that question could change everything.
Ready to empower your team of Improvement Specialists?
Join our community of Improvement Specialists and learn how SafetyCulture can help your organization become an engine of continuous improvement.
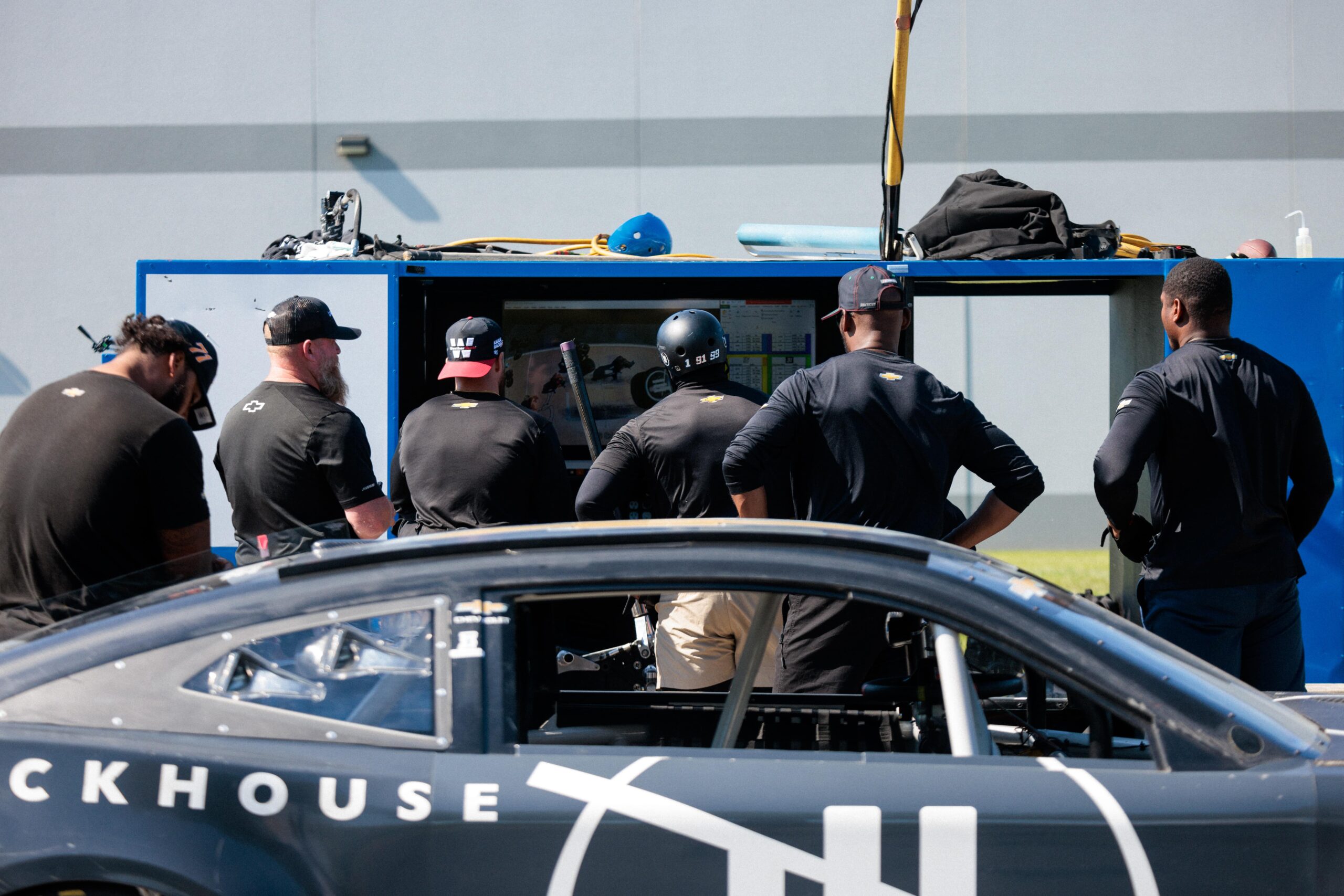
Read more about Improvement Specialists
- How Improvement Specialists are reshaping frontline industries
- How a seafood manufacturer in the UK has reduced nearly 90% of their paper-based records
- How US Roofing Company Tremco efficiently manages their workers on dangerous projects
Important Notice
The information contained in this article is general in nature and you should consider whether the information is appropriate to your specific needs. Legal and other matters referred to in this article are based on our interpretation of laws existing at the time and should not be relied on in place of professional advice. We are not responsible for the content of any site owned by a third party that may be linked to this article. SafetyCulture disclaims all liability (except for any liability which by law cannot be excluded) for any error, inaccuracy, or omission from the information contained in this article, any site linked to this article, and any loss or damage suffered by any person directly or indirectly through relying on this information.