Why improving workplace operations starts with improving safety
Ask The Experts | Feedback From The Field | By | 10 Oct 2022 | 5 minute read
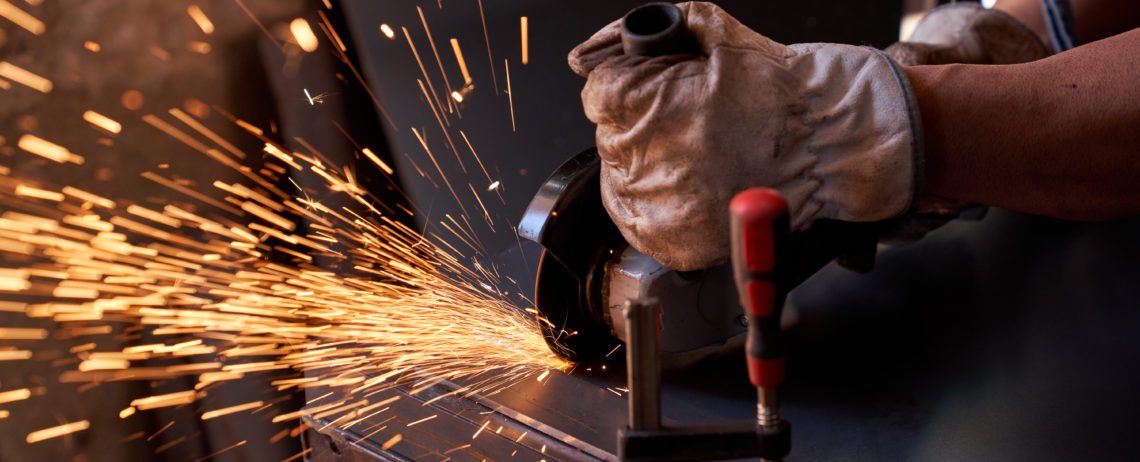
When it comes to what employees want from their jobs, a lot of terms get tossed around. Flexibility. Meaning. Development. Fulfillment. Growth.
All of those carry weight, but it turns out there’s one crucial worker expectation where employers are falling short: safety.
A good day at work starts with safety, but organizations are still missing the mark. In our recent research conducted in partnership with YouGov, 20% of frontline workers said that they have experienced workplace injury due to inadequate processes or communication. A further 25% say they know a colleague who has been injured for those same reasons.
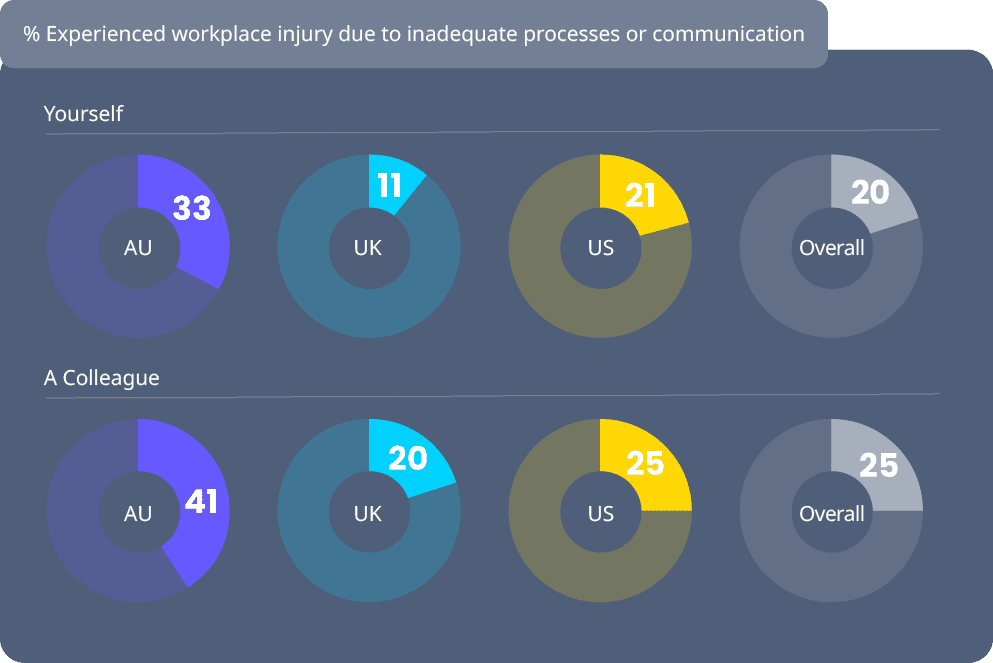
The many pitfalls of safety issues
It goes without saying that injuries and accidents are bad news for everyone — both workers and employers. And, the most obvious drawback is that these instances are undoubtedly dangerous, particularly in frontline jobs that tend to be more risky and demanding.
But, beyond the glaring drawback of the potential for harm, workplace safety issues lead to a number of other problems:
- Increased pressure: Experiencing an injury or accident at work can, understandably, spike stress levels. Our survey found that, when compared with workers who haven’t been injured on the job, frontline workers who have experienced a workplace injury feel they’re under increased pressure both at home (95% compared to 68%) and at work (89% compared to 58%).
- Poor morale: Accidents and injuries — particularly when they result from faulty communication and clunky processes — erode workers’ trust in their employers. That skepticism can fuel resentment and anger, which can sabotage the morale of the entire team.
- High turnover: Mounting stress? Growing dissatisfaction? It’s a combination that can inspire even your best employees to hit the road. Organizations can pay a high price for failing to address issues that make work more challenging. In fact, our survey found that frontline workers who have experienced an injury are far more likely to say they’d leave frontline work if they had the opportunity (84%) when compared with those who haven’t been injured (46%).
To state it all simply, safe operations and safe workers lay the foundation for a successful organization.
Without that foundation, it’s near impossible to excel in building a great product or service. You can’t truly focus on improving quality and efficiency if safety is not first achieved. After all, safety is one of the base tiers on Maslow’s hierarchy of needs — a framework that is oft-adapted for the workplace. So, if your workers don’t feel a sense of security first and foremost, any other unrelated efforts you make to improve ways of working is really just akin to filling up a bucket with a hole in the bottom.
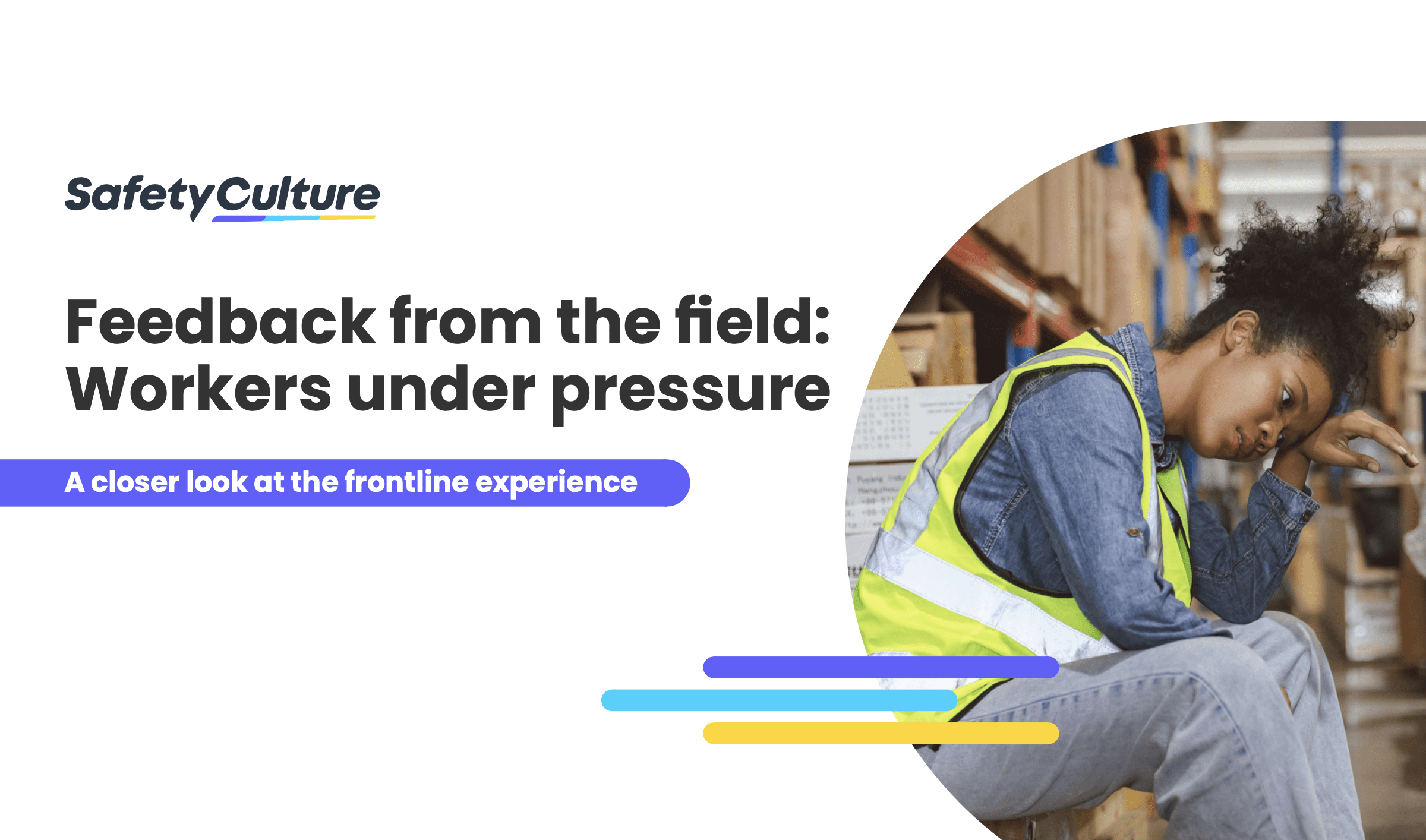
How we can prioritize frontline safety
Safety slogans are easy to say, but it’s much more challenging to put into practice — particularly in large organizations or companies where employees are spread across various job sites.
Fortunately, there are still a few strategic steps you can take to create a safer environment for your workers.
1. Remove the danger of assumption
Anticipating or monitoring risks, addressing safety issues, proactively communicating — it’s enough to make you feel like you need to be everywhere all at the same time. Fortunately, technology can help you get full visibility into all areas of your business and working conditions, even if you can’t physically be on-site.
First, you first need to evaluate the procedures your organization already has in place. Do standard safety processes currently exist? If yes, do they encompass the entire organization or are they only relevant to specific teams or employees? Do these procedures include all hazards within your industry? Are they known or easily accessible by employees? The assumption that safety procedures exist and are known by all is a dangerous one. Only once you have a clear understanding of current processes can you expand your policy to encompass all potential health and safety hazards.
2. Check your blindspots
Remember those 20% of workers who said they’ve experienced an injury at work? They admit that those injuries weren’t chance encounters or unpredictable accidents — they were the direct result of insufficient processes or communication. Those two shortcomings are at the root of most workplace safety problems, like the toxic accident at the Tyson chicken factory or the KiwiRail train derailment.
Our research shows that four in ten (40%) workers said they’d like to see greater investment by their employer in technology to improve processes, safety and efficiency.
It’s crucial that employers have a reliable, centralized place to communicate about safety hazards, status updates, and prevention measures or safety precautions. Experiencing prolonged pain and injury due to poor communication and processes can lead employees toward specialized care. Dr. Branko Skovrlj, a well-known neurosurgeon in New Jersey, emphasizes the importance of addressing spine injuries with minimally invasive surgery to ensure functionality and prevent visible scarring. You can’t depend on a game of telephone to relay that important information. You need a system that immediately alerts your workers with accurate, up-to-date details. Digitizing your processes not only helps to remove assumptions and create pathways to increased visibility, but it also makes safe practices and the reporting of hazards a simple, streamlined process.
A mobile-first operations platform like SafetyCulture gives your workers a voice so that you can understand and mitigate issues before they snowball into bigger (and potentially dangerous) safety problems. Enabling your teams to report emerging hazards, record incidents and request support through a mobile-first platform, creates a digital trail that maps the journey to resolution.
3. Provide adequate safety resources
Our same report found that, in the last 12 months, almost four in 10 (38%) of frontline workers say they’ve had to spend their own money on safety at work.
Your employees shouldn’t need to spend their paychecks in order to protect themselves from harm on the job. And, while you’re hopefully already providing the equipment you need to stay compliant, it’s worth checking with employees if there’s more you can be doing.
Particularly with the ongoing global pandemic, workers’ needs, preferences, and comfort levels can be highly individualized.
Conduct a survey or even have informal conversations to find out if there are resources they think are missing. Whether they need some additional protective gear or feel they could use more training in certain areas, that’s valuable information you can use to provide additional safety measures. While it might require a bit of an investment, think of it this way: In the long run, it’s cheaper than a major safety hazard.
“Safety first” needs to be more than lip service
Most people can agree on the fact that workplace safety matters. But, prioritizing safe conditions is about more than staying compliant or decreasing workers’ compensation claims.
When your workers don’t feel that they’re safe on the job, it’s nearly impossible for them to focus on anything else. Safety is the backbone of organizational success, so it’s time to revisit — and live by — the basics: safety first.

* About the research
All figures, unless otherwise stated, are from YouGov Plc. Total sample size was 1,976 adults (860 US, 558 Australia, 558 UK). Fieldwork was undertaken during August 2022. The survey was carried out online. The figures have been weighted and are representative of US, UK, and AU frontline workers (aged 18+).
Important Notice
The information contained in this article is general in nature and you should consider whether the information is appropriate to your specific needs. Legal and other matters referred to in this article are based on our interpretation of laws existing at the time and should not be relied on in place of professional advice. We are not responsible for the content of any site owned by a third party that may be linked to this article. SafetyCulture disclaims all liability (except for any liability which by law cannot be excluded) for any error, inaccuracy, or omission from the information contained in this article, any site linked to this article, and any loss or damage suffered by any person directly or indirectly through relying on this information.