Safety on Tap: Q&A With Australia’s Leading Safety Experts
Feedback From The Field | Industry Trends | By | 5 May 2017 | 5 minute read
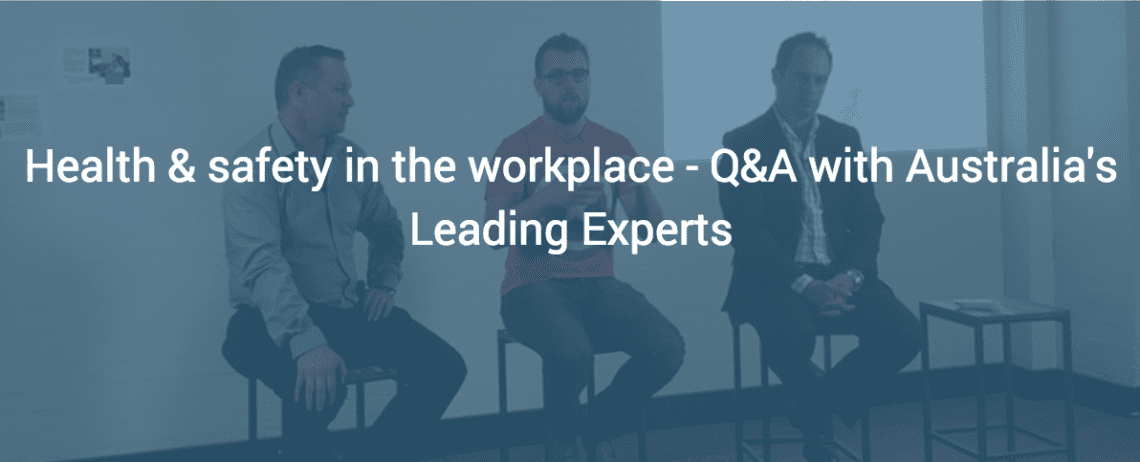
SafetyCulture recently held a panel with three experts in the safety industry; Andrew Barrett, founder of the podcast Safety on Tap, Mick Paton, a Senior Health and Safety on major projects, and Kobi Simmat, CEO of Best Practice Certification. Following is a Q&A session with these safety leaders. For the full video, hop to the bottom of the written Q&A.
The barriers to better health and safety practices
At the outset of the presentation, Andrew outlined what he sees as the two major barriers to better health and safety practices. The first of which is the somewhat antiquated idea that the people on a jobsite are the variable that needs to be constrained and controlled. Andrew is of the opinion that rather than trying to control individuals, safety professionals should focus on human capabilities in creating, relating to one another, and applying critical thinking to existing safety procedures. None of this is to say that humans are infallible. However, if technology is used as a support rather than a constraint, we can maximize some of the potential that people on a jobsite offer.
The second barrier in advancing health and safety is a focus on accidents, or what goes wrong on a jobsite, rather than on a vast knowledge of whatâs been going right. The threat of an incident keeps business owners awake at night, but the truth is that the vast majority of the time, health and safety initiatives go well. Andrew says âIn learning how to improve health and safety, if we focus only on what goes wrong, we only see a fraction of the time so we miss a huge opportunity to learn. What if we focused on how to boost existing procedures or replicated and shared things that are working really well?â
âTry to focus on when things go right as opposed to obsessing about when things go wrong. Itâll give you more information to work with.â Andrew Barrett, founder of Safety on Tap podcast
How do you measure progress against safety outcomes?
Kobi Simmat: We frequently see clients tracking metrics like:
- Fatalities
- Major injuries
- Minor injuries
- Lost time
Better metrics to track progress are leading indicators:
- Number of inspections
- As an example, Kobi worked at a company previously where they performed over 16,000 Take 5 checks per year. When they had 2.5 pre-starts per person per shift, they saw a clear run of production for about 4 weeks. When it dropped below 2.5 audits per person per shift, they had about two weeks to a major incident.
Andrew: Few businesses have that visibility into their safety procedures, though they absolutely should. Companies should track health and safety not just after an incident, but consider the predictive nature of doing the right things and how it connects with positive outcomes. The vast majority of businesses donât make the connection between positive acts and positive outcomes.
Mick: Some leading indicators, like number of audits, can encourage the wrong behavior, so implement them carefully. Look for quality in inspections vs. quantity. Making the auditing system simple and easy to use will encourage employees to actually fit the process into their everyday work lives. âTheyâll [follow safety procedures] not just because itâs a KPI, but because they want to do it.â
Similar to tracking the right KPIs, we want to be sure that when incidents are reported, that reporters are not blamed or ostracized. KPIs could drive under-reporting of incidents, especially if theyâre tied to bonuses or promotions. By measuring KPIs that weâd assume are predictive of health and safety, they could have the opposite effect. This is not to say that we shouldnât track health and safety KPIs, but you need to implement them with care and encourage the right behaviors, similar to how this retail chain coaches as they audit.
How can companies create a cultural shift from seeing people as something to constrain versus being an asset?
Mick: Get supervisors and managers who are the most important to the construction part of the business – if they donât work then nothing works. Theyâre the ones who inform the workers to build what needs to be built. I spend most of my time on a project speaking with supervisors. We have a meeting every morning to discuss the dayâs activities and weâre going to deal with them.
Kobi: We try to focus the most on motivation. If you have motivated employees, you donât need to remind them over and over what to do or how to do it. âIf you donât want to be here, donât be here, I will find a spot for you somewhere else,â he says. When employees are motivated and have bought into the vision, theyâre more likely to comply. You donât have to rely so much on documents and procedures.
Mick: I consider it my job to make my CEO comfortable at night. I work with the supervisors to say: you guys develop a plan. Iâll give you some help and tools, but youâve got the brain, letâs use it and have you get into why weâre doing this.
Andrew: What we absolutely donât want is forcing safety checks because some supervisor is coming to tell everyone how to do their jobs. It doesnât make any sense. The best way to go about doing this âpeople are the solutionsâ bit is to shut their mouths and listen. Just ask some questions: âWhatâs working well today? Whatâs not working well? Whatâs a challenge youâre facing? What would you do differently tomorrow than you did today?â
How do you see technology advancing health and safety on worksites?
Andrew: Eventually sensors and the internet of things will change how we manage risk a ton on the jobsite. Weâll be able to implant sensors that can detect heat stress or even mental stress. Itâll help us focus on people as a solution, not the problem. Sometimes we can see robots as dehumanizing but we need balance of letting tech do the work on what might go wrong so that we can focus on the people, on what goes right.
Mick sees technology enhancing communication in the organization. If you relay a message on paper, it can easily miss some workers on the site. With sensors and more advanced forms of communication, workers can be alerted to site hazards immediately. âThere are critical pieces of information on the site, for example that thereâs gas in the tunnels today. One day weâll have some way of instantly alerting people to that danger.â
Kobi says there are already a lot of technological advancements that are improving safety. In the near term for example, trucking companies are already using glasses that track driversâ blinks. If drivers start to show fatigue, they get alerts to pull over and rest. Similarly, robotic jack hammers are employed on potentially dangerous sites, but are operated by nearby employees who are out of harmâs way. These advancements require fewer inspections and checks, but need advanced analytics and reporting on the progress.
How important is education and awareness as a part of safety?
All three panelists weighed in on the importance of not just preaching about safety initiatives to team members. Of course, education is a foundation for safety, but educating employees isnât as simple as holding more meetings around safety.
Andrew cited the 70/20/10 model. Youâll learn about 10% of the information presented in a formal instruction. You learn about 20% when you learn via social interactions and 70% when you learn on the job, through your own experience. Kobi mentioned that students learn much better when they know theyâll be tested on the information theyâre learning. Taking this a step further, if employees are presenting on the information, they learn at an even more effective rate.
In the UK, Mick says that legislators are looking at accreditation programs around scaffolding. After fatalities in scaffolding, the UK is now considering not just classroom learning, but an apprenticeship to help students absorb and retain the information more effectively.
Andrew hosts the podcast, Safety on Tap, and focuses on new ways to get different results in health and safety. He actively recruits guests on the show who try to think outside the box to solve the current barriers in health and safety. The mission is to help leaders who want to grow themselves and drastically help improve health and safety along the way. SafetyCultureâs CEO, Luke Anear, will be interviewed on Safety on Tap, the episode will be available soon. Check out the podcast here for more info. Â
Important Notice
The information contained in this article is general in nature and you should consider whether the information is appropriate to your specific needs. Legal and other matters referred to in this article are based on our interpretation of laws existing at the time and should not be relied on in place of professional advice. We are not responsible for the content of any site owned by a third party that may be linked to this article. SafetyCulture disclaims all liability (except for any liability which by law cannot be excluded) for any error, inaccuracy, or omission from the information contained in this article, any site linked to this article, and any loss or damage suffered by any person directly or indirectly through relying on this information.