World Day for Safety and Health at Work 2021
Feedback From The Field | Industry Trends | By | 27 Apr 2017 | 5 minute read
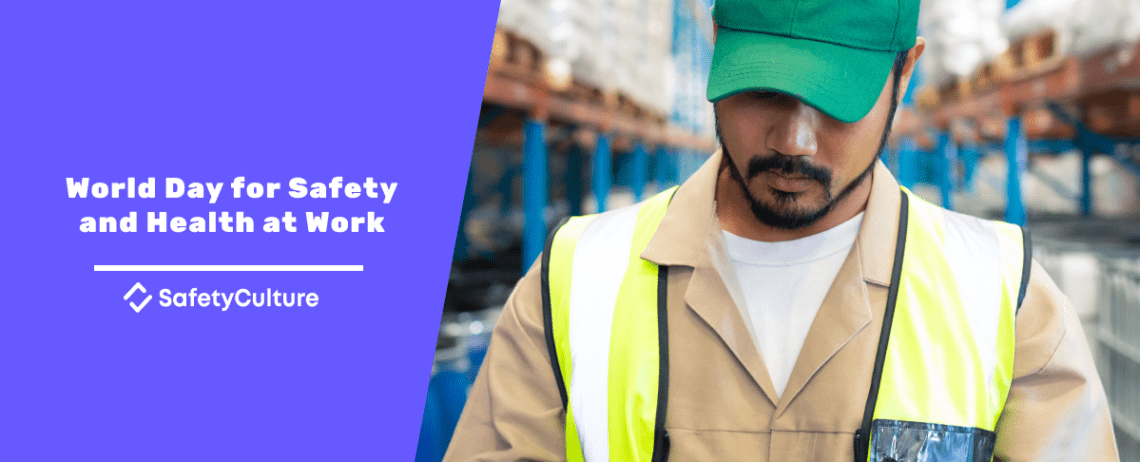
On April 28th of each year, the UN highlights the importance of Safety and Health at Work. The World Day for Safety and Health at Work was established as a result of a 2030 Agenda for Sustainable Development. The plan has specific targets such as: ending poverty, protecting the planet and ensuring prosperity for all. Part of ensuring prosperity for all is outlined as the âprotection of labor rights and promotion of safe and secure working environments for all workers, including migrant workers, in particular women migrants, and those in precarious employment.â
Now more than ever, itâs no longer important to just spot issues as they occur – we need to be one step ahead.
This means when it comes to our health and safety, we need to future-proof our operations by utilizing robust methods to mitigate risks, and improve our inspections and checks for the future. Weâre out of âfire-fightingâ territory, and now into re-building a safer, more solid future. With World Day for Health & Safety at Work and International Workers Day on the horizon, weâre all looking for more information as to how to conduct safe practices in our workplaces.Â
Very often, how we manage safety protocols come from a place of compliance. But this year, everyone has had a new job – and we all need to keep each other safe. Shifting towards a safety culture comes from a place of empathy, which means doing the right thing by the right people.
As workers on the front line, in our living rooms, and in workplaces around the world, we can do that, one check at a time.
Identifying problem areas in safety data
In order to track the safety of these workers, countries report on frequency rates of fatal and non-fatal occupational injuries by sex and migrant status. One of the major barriers in implementing successful safety programs is education around how to elevate safety standards. Without a formal system in place to track where incidents occur, we canât learn from past mistakes. A focus on data collection creates a dataset at a company and national level and provides the opportunity to learn at a high level where issues in safety are. For example, the Centre for Corporate Accountability in the UK published data findings that migrant workers are twice as likely to suffer fatalities on a construction site than a UK-born worker. Once we have this essential information, legislative bodies and organizations can begin discussions around how to improve workplaces for everyone.
The International Labour Organization cites the following barriers in reporting incidents:
- Complex reporting and notification procedures
- Varied reporting procedures across organizations
- Late reporting of injuries and diseases
- Reluctance to report immediately or use of private physicians
- Difference between what is compensable and what is recordable
- Discrepancy between recorded claims and compensation claims
An essential theme throughout the ILOâs data analysis is the need for preventative measures. At an organizational level, that means companies should work with governmental institutions on the prevention of incidents and serious injuries as well as the early detection and treatment of work-related diseases. Hazardous sectors like mining, construction and agriculture need to incorporate the prevention of occupational diseases directly into their health surveillance programs to keep it front of mind.
So how can we continue to raise our game when it comes to managing risk and ensuring safety compliance? Itâs all about trusting one reliable tool we have at our disposal – technology.
Staying one check ahead
We can use technology to replace old paper-based habits to foster more collaborative communication, improve cohesion between auditing, tracking issues, and to gain access to a more reliable set of H&S data. Try adopting these software-based practices:
Implement digital checklists
You can digitize every part of your occupational health and safety protocols. Even something like keeping bathrooms sanitized can be digitized, through an app such as iAuditor. This way, you can have a Whatsapp-style chat about what needs to be fixed or actioned, and you can attach photos of the issue, as well as assigning tasks to members of your team.
Utilize the latest technology
Keeping everyone safe is easier when you have technology to help you. For spotting health and safety issues like a broken fridge, using sensor devices that can monitor ongoing issues of compliance can mean you can have peace of mind. These wireless monitor systems can allow you to keep an eye on variables such as capturing temperature, humidity, air pressure, air quality, and gas concentrations, all from the comfort of your own home.
Upskill your teams through online learning portals
Staying one check ahead isnât possible unless you know exactly what compliance looks like. With a micro-learning platform like EdApp, your entire team can be upskilled on how to spot and resolve health and safety issues. The engaging learning software conducted in bitesize lessons means that your teams are much more likely to adopt best practices.
Address complex reporting
From an organizational perspective, one of the most important ways to track data is to ensure that employees are not reprimanded in any way for reporting incidents. The point of incident reporting is to learn, not to make reporters a target. For reference, this organization uses safety audits and reporting to reward their employees, rather than look for âgotchaâ moments.
If youâre not sure where to get started on identifying potential issues in your organization, use this 6-step guide as a reference for what questions you should be asking of your auditing data. See how your organization ranks in workplace safety with World Day for Safety and Health at Work quiz.
Continuous safety, redefined
Luxottica is one of the worldâs largest eyewear businesses, operating across more than 430 retail stores in Australia and New Zealand. Luxottica created daily and weekly COVID-19 checks, and digitizing these checks has meant that the time spent on these tasks has been reduced through the use of inspection software.
These checks helped to reinforce standards across the stores, which had an immensely beneficial result on their health and safety culture overall:
âCustomers respond well because people who had a need could actually get to a store while still feeling like they had a safe experienceâ – Luxottica
Software company RFP360 never thought theyâd be faced with a global pandemic. Suddenly, all their standard health and safety processes were quickly replaced with a set of new ones. Technology helped them make that quick shift. In times like these, software can provide a valuable safety net when a crisis arises. iAuditor gave them safety suggestions they hadnât even considered, and they soon found it to be a seamless way of conducting checks and inspections:
âWe saw the benefit not just in terms of risk reduction from a legal perspective, but for the health and safety of those who make it possible.â – RFP360
Use technology to create a true safety culture
Technology can really help us at a time when many businesses are pivoting their health and safety practices.
For workplaces that require hands-on training, staff should access as much digital training as possible prior to returning to work. This not only helps the business quickly restore its operations but also reassures staff that their workplace is safe and is taking appropriate steps to protect them through bitesize learning.
Digital checklists are not only more hygienic but can be an incredible tool to future proof businesses from risks, and gather important data on how many recurring issues happen over a period of time. By utilizing sensors, monitoring has never been easier. Being able to track valuable data across distributed teams means that less time is wasted in manually performing checks and inspections.
Above all, tech can help ease the mental load. It can also help us âbuild back betterâ – a perfect opportunity to implement a true âsafety cultureâ, and empower our teams to feel confident that health and safety procedures are handled effectively.
Join in the dialogue and find out how you can stay one check ahead.
Important Notice
The information contained in this article is general in nature and you should consider whether the information is appropriate to your specific needs. Legal and other matters referred to in this article are based on our interpretation of laws existing at the time and should not be relied on in place of professional advice. We are not responsible for the content of any site owned by a third party that may be linked to this article. SafetyCulture disclaims all liability (except for any liability which by law cannot be excluded) for any error, inaccuracy, or omission from the information contained in this article, any site linked to this article, and any loss or damage suffered by any person directly or indirectly through relying on this information.