Sensors, and your workers on the frontline: a love story
Checklist Best Practices | By | 30 Jul 2020 | 3 minute read
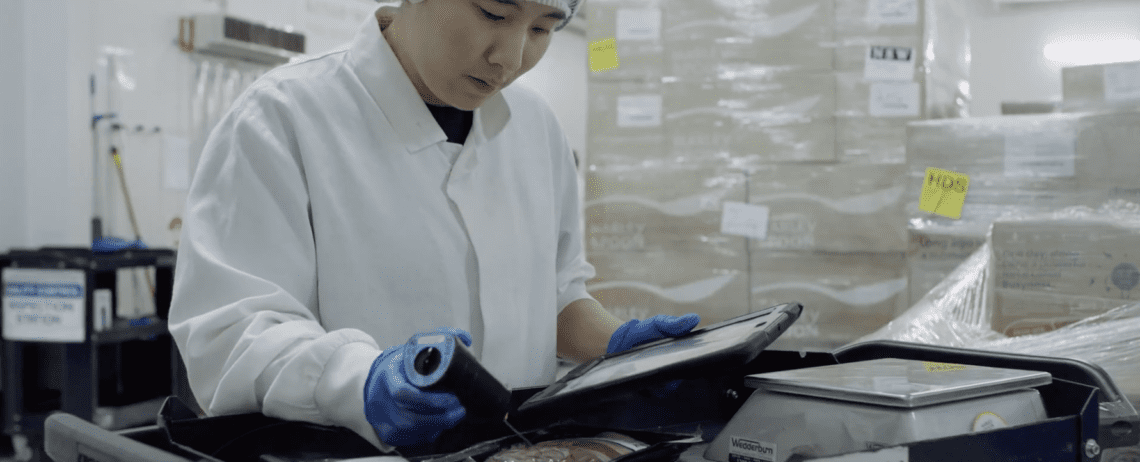
Listen for the warning signs
Right now, your equipment is sending signals to help your business avoid disaster.
Is anyone listening?
When critical assets fail, will your team notice and respond effectively?
Businesses now depend upon their equipment more than ever before. Operation-critical assets are responsible for maintaining product safety, protecting expensive inventory, and delivering essential services around the globe.
Data centers with precision temperature requirements are responsible for safely storing much of the world’s information. Cold storage locations are essential for delivering food safety and maintaining the vaccines that protect our health. Industrial processing equipment provides the link necessary for our packages to arrive daily.
Assets have never been more important, and failure can damage your brand in the blink of an eye
Equipment failure can result in catastrophic, growth stalling, customer-impacting events that won’t be quickly forgotten. Businesses that lack visibility of their operations and the tools necessary to predict failures will struggle to compete. Now is the time to address these critical process gaps before disaster strikes.
Paper is a disaster waiting to happen
It’s only a matter of time before a critical asset falls over. Developing a proactive, data-driven approach can help predict incidents before they occur and deliver a hidden competitive advantage. Reactive paper-based processes must evolve, and connected data is the first step towards building a proactive culture.
In the post-COVID-19 world, lightning-fast incident response is essential. Paper-based processes introduce delays that compound incidents by slowing detection and increasing response times. Instant visibility can help organizations to understand their operations like never before. Fast access to real-time, connected data streams can be the difference between swapping out failing components or catastrophic asset failure.
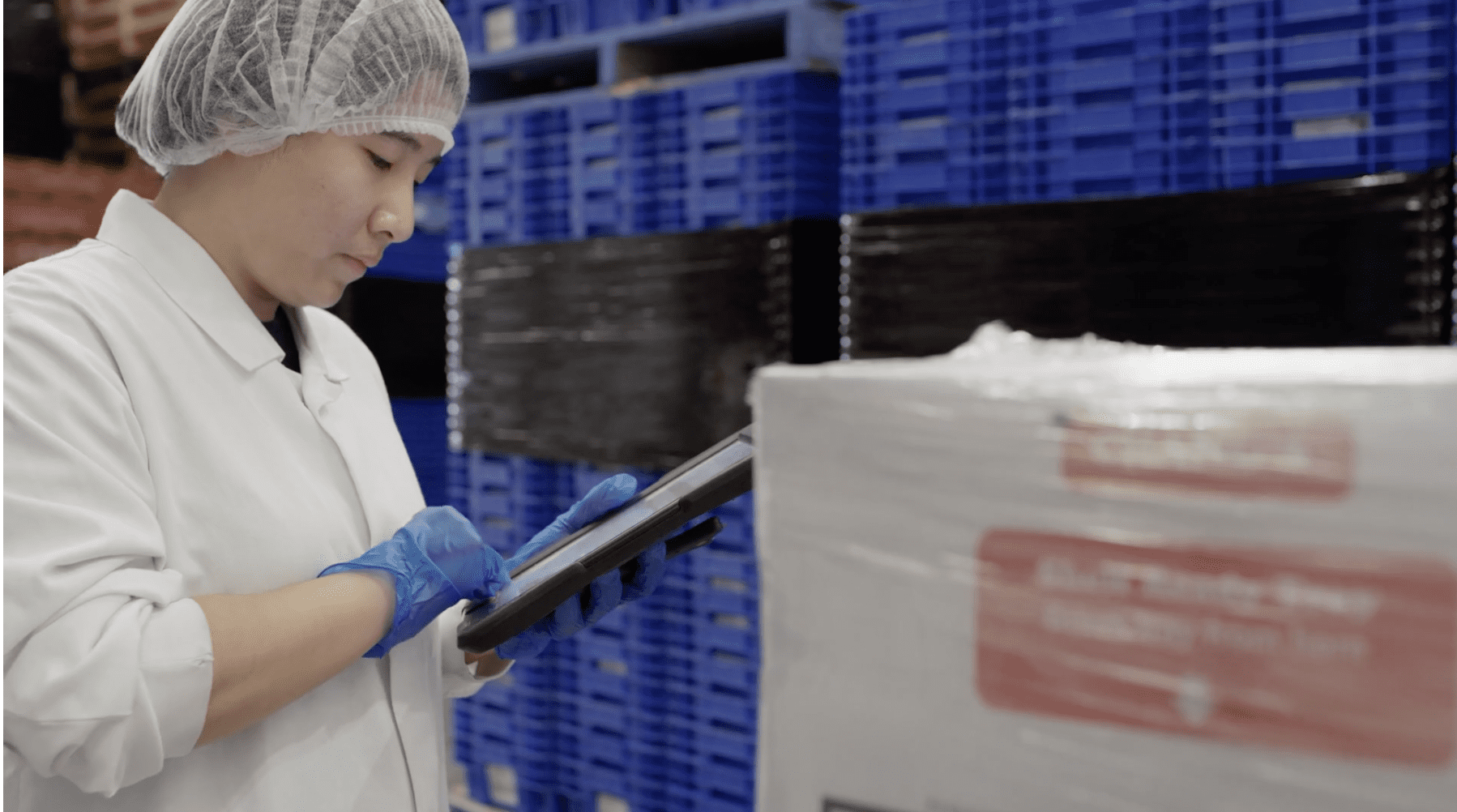
Keep your finger on the pulse with sensors
Completely automate your asset monitoring process with sensors. Outsource the burden of unexpected asset failures using real-time visibility and instant notifications. Operational information is continually collected by sensors attached to your equipment. The incoming data from these sensors is then tracked by iAuditor with any unusual activity triggering an alert. Once an alert is triggered, notifications are forwarded to a predefined list of stakeholders who can quickly respond with a resolution. Protect your brand and achieve peace of mind with complete visibility of your business using sensors from SafetyCulture.
Sensors saved Marley Spoon, twice
Meal delivery service, Marley Spoon, faces the challenge of maintaining food quality and customer satisfaction for thousands of meals delivered to Australian homes each week. For Marley Spoon, the risk of inventory loss from equipment failure or environmental conditions is exceptionally high at $200,000 to $300,000 for a single day of production.
Marley Spoon turned to sensors to ensure maximum safety for their customers and mitigate the risk of recalls or other brand-damaging events. In the past, manual paper-based cold room checks were completed to monitor temperature levels. Now, Marley Spoon has enhanced its operations with real-time visibility of temperature information using integrated sensors. Sensor data is sent to iAuditor, which completely automates the monitoring process, preventing failure and stopping inventory loss before it happens.
Cold room disaster averted
One weekend, a cold room door wasn’t closed properly in the Marley Spoon production facility. Temperatures started rising, and iAuditor triggered an alert using the data from the temperature sensors. The team sent someone to the facility to immediately close the door.
If the problem had been discovered on Monday – it would have been too late. The inventory would have spoiled, representing a significant financial loss for the Marley Spoon team.
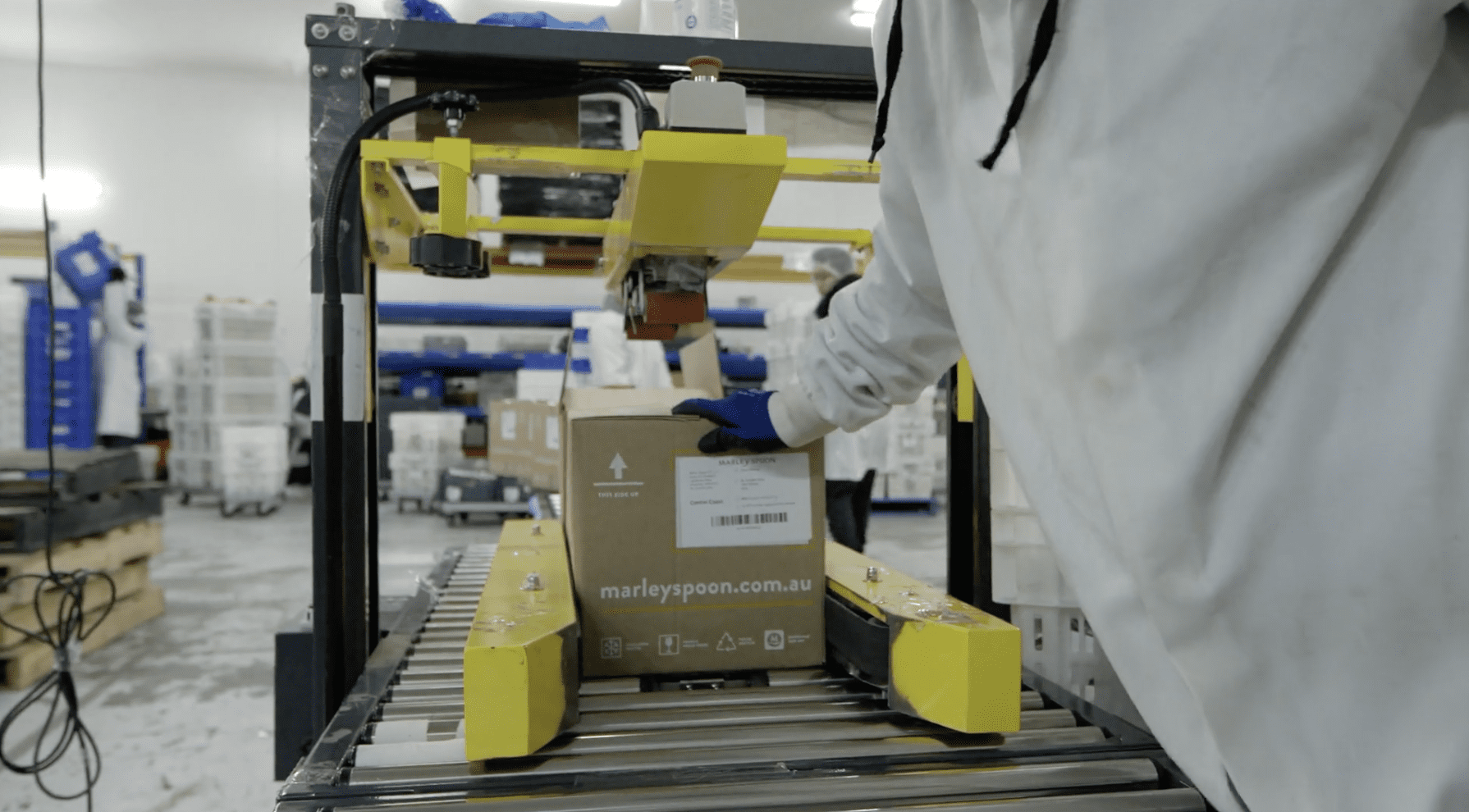
Hidden electrical faults exposed
A few weeks after Marley Spoon implemented sensors, the manager at a manufacturing facility called SafetyCulture to report an error. The manager noticed that the sensors were producing erratic values that weren’t reflected on the fridge’s own temperature display. After replacing the sensors multiple times, the problem persisted. Eventually, this prompted Marley Spoon to bring in a maintenance crew to look at their cold storage. The maintenance crew, which specialised in electrical installations for industrial business, quickly discovered an undetected electrical fault inside the refrigeration unit. Left unchecked, this issue could have resulted in total system failure, risking product loss and costly downtime.
The critical fault would never have been discovered without Marley Spoon’s new sensor system from SafetyCulture. iAuditor and sensors saved Marley Spoon thousands in potential inventory loss and protected their brand from irreparable damage.
Data alone isn’t sufficient
Sensor data alone won’t enhance operational resilience. The data provided by sensors must be linked with tools that automate incident detection, manage workflows, and deliver meaningful insights. iAuditor manages the flow of connected data from sensors and notifies relevant team members immediately when events occur so that issues can be resolved fast.
Sensors are enabling businesses everywhere
Sensors are helping businesses in every industry to protect their assets and avoid disasters before they happen from temperature-controlled aviation parts to carefully chilled medical samples. The food that you eat, the vaccines that protect your health, and the planes that you fly on, all require precise temperature control to maximize safety. Enhanced visibility of this data is critical for businesses of all sizes, and automating this process has never been easier.
Learn more about how sensors can help empower your team, automate your incident response, and turn data into action TODAY.
Important Notice
The information contained in this article is general in nature and you should consider whether the information is appropriate to your specific needs. Legal and other matters referred to in this article are based on our interpretation of laws existing at the time and should not be relied on in place of professional advice. We are not responsible for the content of any site owned by a third party that may be linked to this article. SafetyCulture disclaims all liability (except for any liability which by law cannot be excluded) for any error, inaccuracy, or omission from the information contained in this article, any site linked to this article, and any loss or damage suffered by any person directly or indirectly through relying on this information.