How to speed up construction projects without sacrificing quality
World Of Work | By | 13 Sep 2024 | 5 minute read
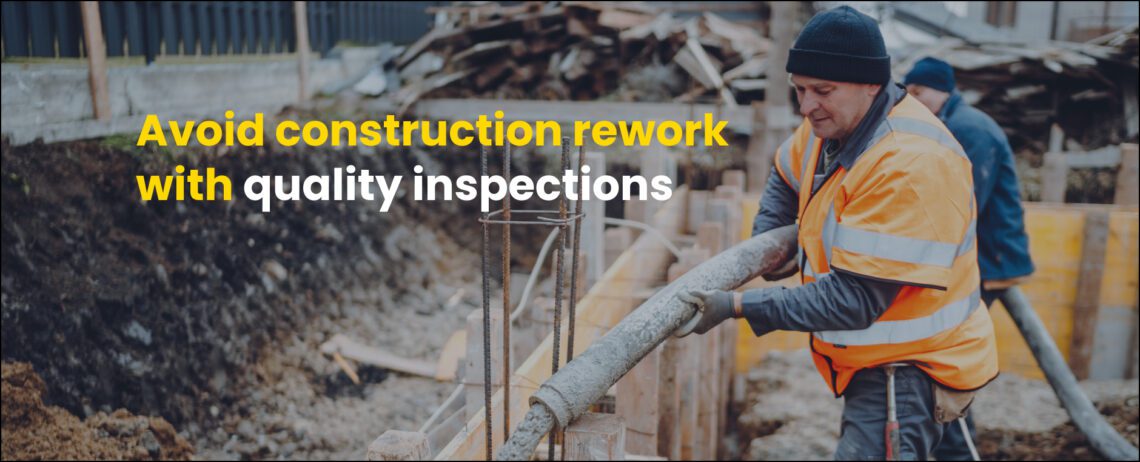
In the construction game, it doesn’t matter where youâre based or how big your company isâeveryone faces similar challenges. The pressure is always on to complete projects on time while balancing strict regulations, safety protocols, and quality standards.
This article includes practical strategies to help you meet these challenges head-on. Weâll explore how construction quality management software can boost productivity and improve worker safety to reduce incidents and downtime.
Balancing priorities on the job site
Construction projects are complex, with project managers and builders constantly balancing tight budgets and client expectations. To set a strong foundation for any project, it’s critical to create Construction Proposal documents that clearly define scope, responsibilities, and standards from the very start. Then, when the job is nearly done, a postwork inspection is conducted to make sure the finished construction project meets high standards and regulations and is ready to be occupied without problems. However, when postwork inspections don’t go according to plan, rework can be costlyâwith both time and money.
Using modern digital tools like construction quality management software can streamline your inspection process along the way. It can help you avoid costly rework, prevent accidents, and meet ISO 9001 standards, while improving profitability.
Achieve high standards and keep compliant
Old-school construction inspection methods like pen and paper or spreadsheets might have worked in the past, but they could be holding you back now. As construction projects get more complex, these methods become less and less effective.
Imagine the difference in your day if your pre-start checks, site safety walks, and 5S audits were digitized. Youâd have real-time insights, automated documentation, and information accessible from anywhere.
Digital audits and checklists remove paperwork, improve accuracy, and allow teams to attach evidence directly from mobile devices. Productivity soars as teams save time and money while building confidence and accountability. Letâs explore the benefits in more detail.
Avoid costly rework with on-the-spot digital documentation
Did you know around 30% of the work performed by construction companies is actually rework? Rework wastes time, increases safety risks, and drives up costs. Having better quality checks and access to on-the-spot digital documentation leads to better decision-making on-site and fewer mistakes.
Being able to add media, assign follow-up actions, and monitor completion in real-time can reduce the need for rework while keeping project budgets and timelines on track. Effective construction reporting also plays a key role in this process, offering real-time insights, accountability, and accurate data for better project outcomes.
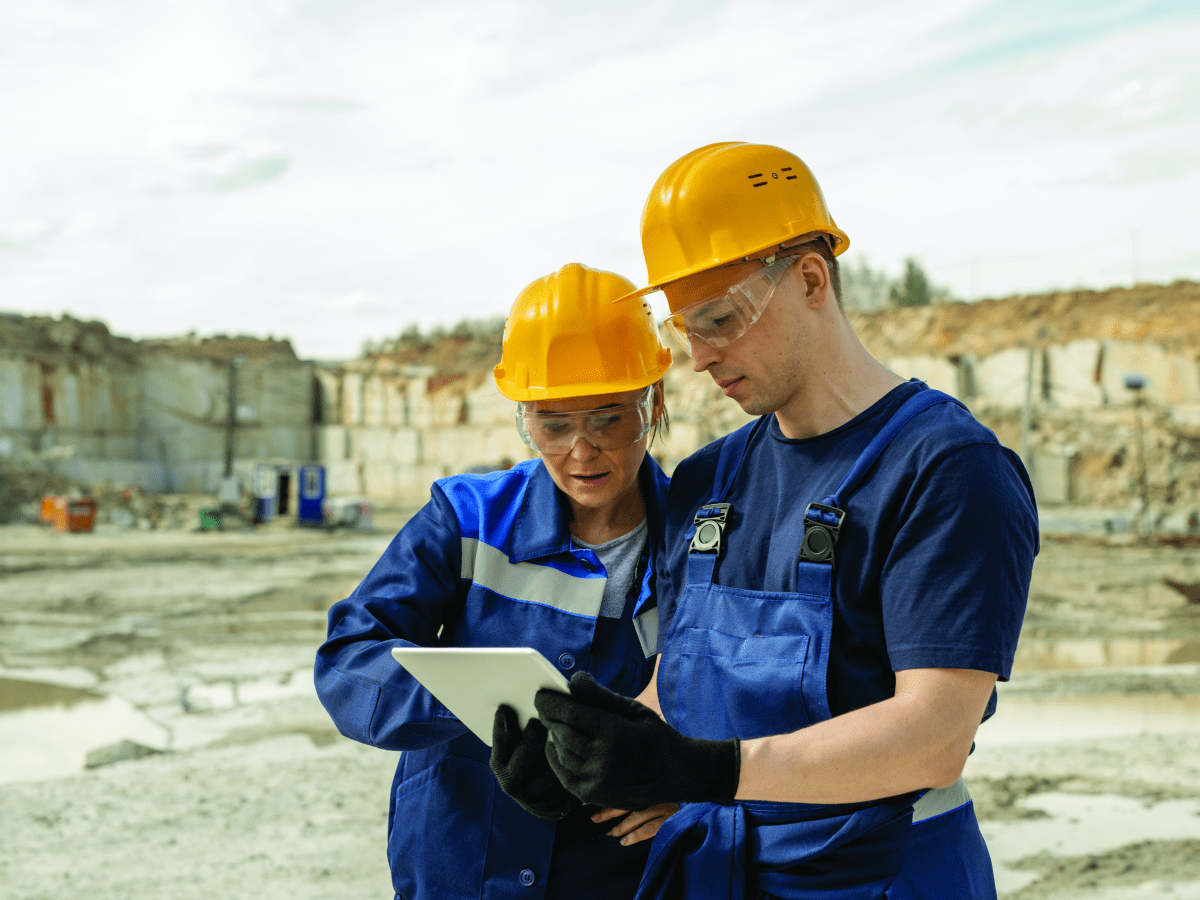
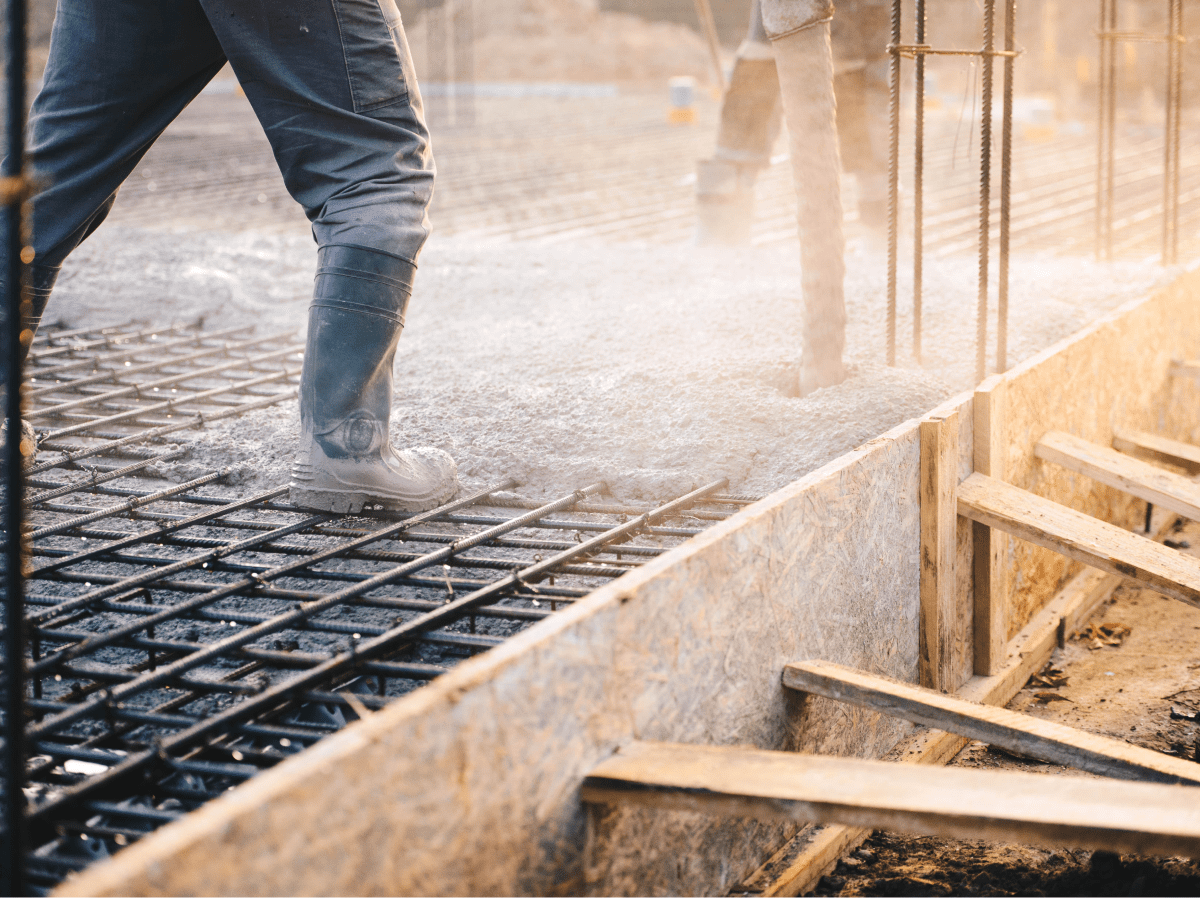
Exceed quality standards
Meeting quality standards in construction is just the beginning. Digital checklists empower you to monitor and enforce consistent quality across teams of any size. By gaining clear insights from your data, you can identify certain trades or skills your team struggles with. With additional training, you can help your team lift what theyâre capable of, every day.
This means less time spent on rework and more time focused on delivering high-quality projects that meet client expectations, increasing the chance of more projects in the future.
Boosting safety with easy-to-use digital tools
Construction quality management software streamlines compliance and safety processes on every job site while enhancing overall safety. Every worker can easily stay connected using any device and any language.
Even if you have lone workers in remote areas, SafetyCultureâs offline capabilities ensure safety even in the most isolated environments. Get total peace of mind with automated alerts and easy access to workers’ whereabouts to keep them safe.
Empower your team with insights at their fingertips
Giving your frontline workers a tool that can be accessed on mobile, tablet or computer enables them to spot safety and quality blindspots as they work before they become problems. You can track everything in one place and automate everyday tasks so that your team can act on issues immediately. Itâs about encouraging accountability for quality and safety at every step.
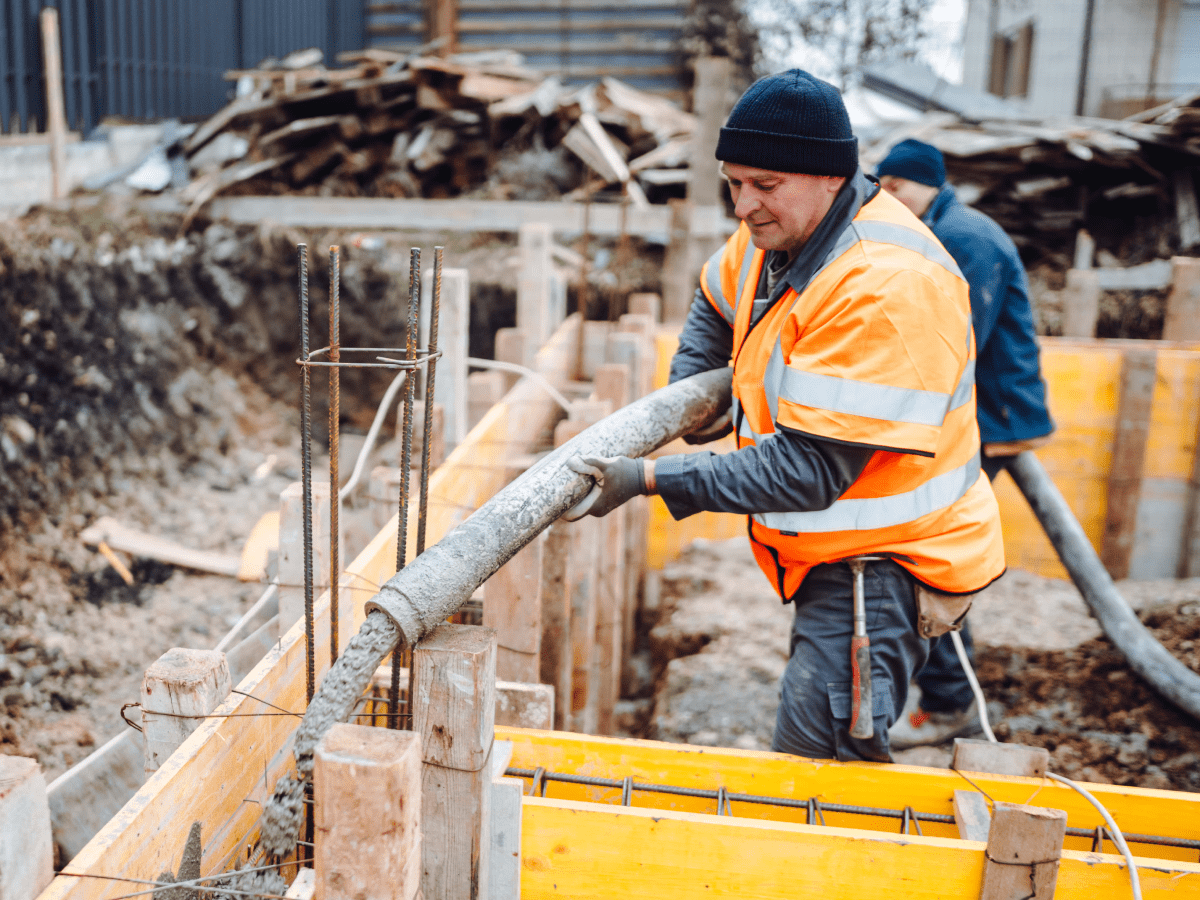
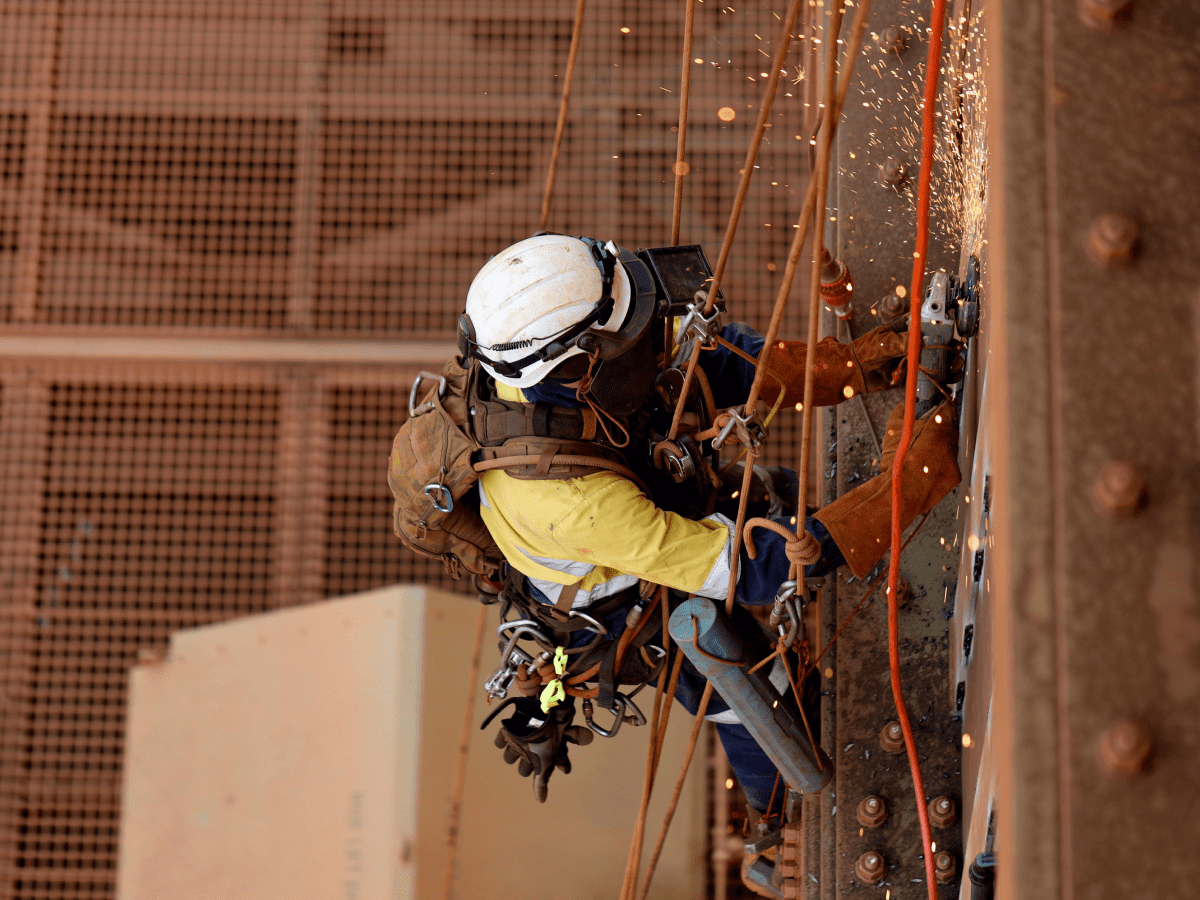
Five ways to get the most out of your quality checks and inspections
Fine-tune your construction quality processes with these steps:
- Go digital: Ditch the paper trail and transition to digital checklists to streamline your inspections. This allows for easier updates, real-time data capture, and better tracking of issues. Start by transitioning from paper-based checklists to digital ones. Invest in user-friendly software that integrates easily with your existing processes. Begin with a pilot project to familiarize your team with the tools, and gradually expand to cover all inspection tasks.
- Centralize your data: Choose a centralized digital platform that stores all inspection data in one place. Encourage your team to log every observation and issue in this system, fostering transparency and collaboration. Regularly review the data to spot trends and make informed decisions.
- Empower your teams with training: Offer hands-on training sessions so everyone can confidently use the new digital tools. Pair less tech-savvy team members with digital natives to create a supportive learning environment. Reinforce training with ongoing support to address and overcome any resistance to the new technology. You can also record sessions and use Happy Scribeâs video to text converter to create transcripts, making it easier for employees to revisit key points and stay on track.
- Leverage automation: Identify repetitive tasks in your inspection process, like report generation or issue tracking, that can be automated. Use your digital platformâs automation features to set up these workflows, freeing up your team to focus on more critical tasks.
- Use real-time reporting: Implement tools that provide instant updates and notifications. Encourage your team to report issues as soon as they arise. Set up alerts for critical issues to ensure they are addressed promptly, reducing the risk of delays or costly rework.
These tips will set you up for success, but what happens when companies put them into practice?
Leading by example
Construction companies that have embraced these strategies are seeing impressive results. By optimizing inspections with digital tools, theyâve sped up processes, reduced rework, and delivered higher-quality projects.
CBRE gained $10.92M in operational improvements thanks to SafetyCultureâs intuitive interface, collaboration features, and real-time communication. Automated alerts and centralized communication have slashed issue resolution times, resulting in a 6-month payback period and 266,000 hours saved with automated tasks and inspections. Safety and compliance features alone saved them hundreds of thousands of dollars.
Level 10 Construction improved safety and quality in real-time by adopting custom pre-task digital checklists, allowing managers to view and act on hazards immediately. Their team achieved 2.5 million man-hours without a single lost time injury. âSafetyCulture allows us to achieve that,â says Project Executive Steve DeWees. âYou donât work 2.5 million hours and just be lucky.â Discover how Level 10 uses SafetyCulture to level up their quality here.
Schindler empowered employees to report unsafe conditions and quickly rectify them. Before their digital transformation, they recorded only 20 hazards a year. Now, they log around 1,200 hazards annually, contributing to their safest years on record. Read how SafetyCulture is elevating Schindler’s safety game here.
Thermosash uses SafetyCulture to deliver engaging training courses in each employeeâs native language. Overcoming the language barrier has significantly increased the quality of work and prevented recurring issues like poor-quality window seals. Check out how Thermosash has clear quality processes, covered in their case study here.
Ready to construct your path to better quality?
Set a new standard for your workforce and lift the load of paperwork and documentation.
Read more to get the blueprint for process improvement:
- Tremco uses inspections to protect teams working on dangerous projects
- ArcelorMittal Construction saved 5,000 hours using SafetyCulture
- Donaldson Group standardized operational processes
Important Notice
The information contained in this article is general in nature and you should consider whether the information is appropriate to your specific needs. Legal and other matters referred to in this article are based on our interpretation of laws existing at the time and should not be relied on in place of professional advice. We are not responsible for the content of any site owned by a third party that may be linked to this article. SafetyCulture disclaims all liability (except for any liability which by law cannot be excluded) for any error, inaccuracy, or omission from the information contained in this article, any site linked to this article, and any loss or damage suffered by any person directly or indirectly through relying on this information.