The SafetyCulture Community Is Performing 1 Million Inspections Per Month
SafetyCulture News | By | 2 Jun 2016 | 4 minute read
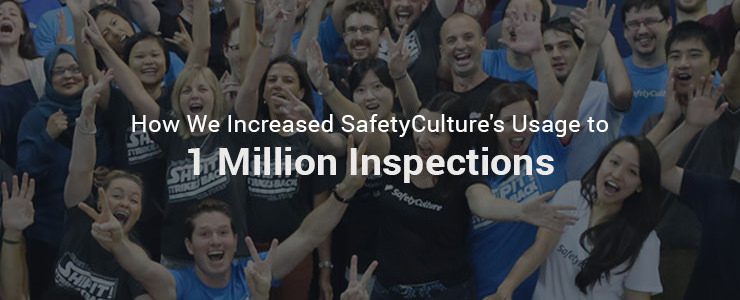
Over 1 million inspections are now performed by our awesome customers using SafetyCulture iAuditor each month. This milestone has only been possible because front line workers are driving change from the bottom up. It means that our customers are collectively one million small steps closer to safer and higher quality work. When SafetyCulture iAuditor first started in a garage four years ago, it was hard to imagine weâd be where we are today, with over seventy employees spanning three continents and committed customers who are performing one million inspections a month.
It Started as an Experiment
The safety and quality industries traditionally relied on a reactive approach to reform. After major incidents occurred, governments would draft legislation for approval, companies would then generate policies and procedures to conform to the new legislation. These translated into new safety or quality practices, and frontline workers would be told how and when to adopt those processes.
However, with the advent of the smartphone, this antiquated model was no longer the only option. SafetyCulture and SafetyCulture iAuditor aimed to make safety and quality less reactive and more proactive. This concept hinges on frontline worker engagement and communication.
Rather than a frontline employee being instructed what to do via legislation and management, they could drive change by communicating the hazards they were already aware of to other teams in the field and to the management levels of the company. Thanks to the accessibility and constant connectivity that mobile devices provided, SafetyCulture found their vehicle for proactive change.
SafetyCulture then essentially started the worldâs largest inspection experiment. 200 million questions later, the experiment is going pretty well. These 200 million questions also offer an incredible amount of data from the field, which management can then use to analyze how safety and quality programs are working, and make more informed decisions than ever before.
The Customer Commitment
The goal of SafetyCulture was for customers to leverage a low-tech solution that would allow people to pick up their phones and be able to use an auditing checklist immediately, without much training or a huge implementation rollout. They also needed to be able to conduct these inspections from anywhere, with or without wifi, to control documentation and usage, and to understand macro trends in the organizationâs safety and quality. Many of SafetyCultureâs and SafetyCulture iAuditorâs features were borne of the effort to address those needs.
Of course, every company touts their commitment to the customer. Zappos delivers better customer support than almost any other online retailer. Volvo is known for their obsession with safety and crash testing. Disney ensures that each detail within their amusement parks is intended to add to a âmagical experienceâ. SafetyCulture has made a similar commitment to integrate customer needs into every operation – from customer support to user design, all the way through to when someone first downloads the app through  to high-level company reporting.
How We Maintain Focus
Each new employee at SafetyCulture spends time in Customer Support, regardless of their new position. This allows them to understand where customers are asking questions, the varied ways theyâre using the app, and the pain points the customers felt before ever picking up the app.
Employees are also encouraged to create their own checklists. Nearly everyone makes the rookie mistake of simply digitizing a paper checklist they found online. When they sit down with an employee who is more familiar with the product, they learn the power of building logic into checklists, or how important document control can be, for example.
Once an employee is actually onboarded with SafetyCulture, they have various ways to remain âin touchâ with customers on a daily basis. We lean on our customer success folks a lot to be ambassadors for our customers. The team sends out summaries of customer visits and are pivotal in many design or development decisions, as theyâre the most familiar with the use cases and pain points of our customers. During ShipIt week we all get the opportunity to hear from real customers who have become evangelists. They give frank and open feedback on where they think SafetyCulture iAuditor should move next, and how theyâre already using it in their daily lives. There are many touchpoints like this that SafetyCulture has ingrained into everyday practices that make up the company culture. These touchpoints actually make decisions easier by providing a guide and taking subjectivity out of the decision. We love feedback, particularly if it relates to something we can improve. If our customers donât understand a feature, a marketing email, or the design within the app, it needs to be revisited or enhanced.
For example, many customers were loving the ability to conduct audits in the field from a mobile device, but were exporting information to PDFs or sending emails with file attachments. While this enhanced communication, it didnât fully take advantage of the data and information thatâs passed between auditors and managers.
Getting data effortlessly from the field to the office was the impetus for the SafetyCulture desktop platform. SafetyCulture grew from a mobile app experience, which is ideal for people on the frontline and added a team communication component that essentially elevates the knowledge of the entire organization. On the platform, managers can see analytics on where certain initiatives are underperforming or where teams are excelling. Then they know what is working well and what can be improved in real time. They can then focus their safety and quality efforts where it will have the greatest impact. Once a feedback loop was created with real-time visibility into audits, we saw huge growth. Teams in any industry, from construction to manufacturing, or aviation to restaurants, are looking for ways to communicate better amongst teams. Itâs a fundamental customer need that weâre working to address.
While our customers are preoccupied performing one million inspections each month, weâll keep working to take the SafetyCulture platform to the next level, nudged in the right direction by our customers themselves – thank you!
Important Notice
The information contained in this article is general in nature and you should consider whether the information is appropriate to your specific needs. Legal and other matters referred to in this article are based on our interpretation of laws existing at the time and should not be relied on in place of professional advice. We are not responsible for the content of any site owned by a third party that may be linked to this article. SafetyCulture disclaims all liability (except for any liability which by law cannot be excluded) for any error, inaccuracy, or omission from the information contained in this article, any site linked to this article, and any loss or damage suffered by any person directly or indirectly through relying on this information.