Why Digital Checklists Beat Paper Every Single Time
SafetyCulture News | By | 19 Nov 2018 | 2 minute read
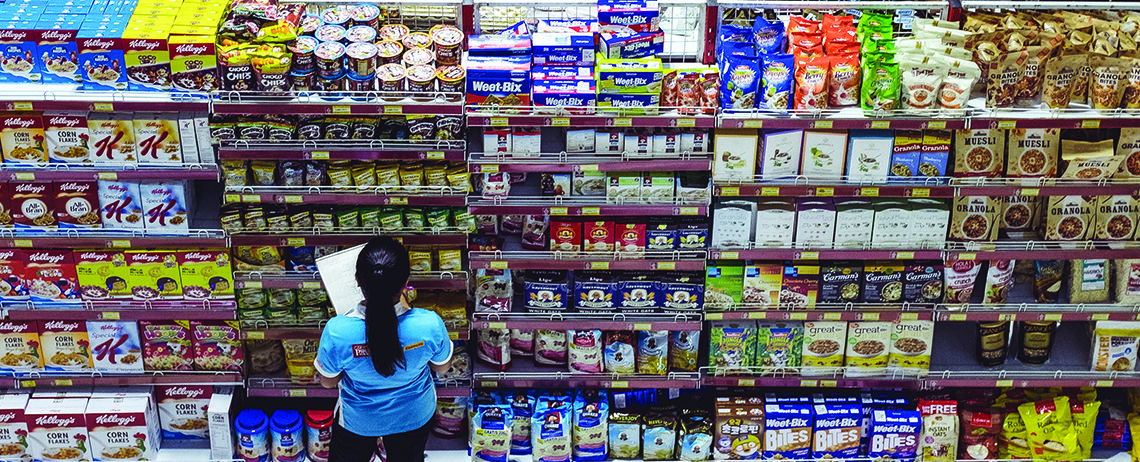
A high school in Australia made history in November by allowing final year students to take their English literature exam digitally for the first time. It’s a sign of just how entrenched digital processes and actions have become in our everyday life.
Since working electronically became the norm, reports, documents and correspondence are rarely handwritten. So why are you still filling out checklists using pen and paper?
A well-designed checklist application can be a vital tool in compliance and quality control. It gives employees more scope in reporting, which can boost the overall level of service and standards. It also cuts time spent filling out paperwork and negotiating the resulting paper trail, with multiple benefits in terms of cost and process efficiencies.
Digital forms increase the quantity, consistency and quality of feedback
A study released earlier this year by the University of Aberdeen compared a two year period of feedback given to final-year medical students across paper-scoring sheets and iPads. It found that a greater number of comments were likely to be given by iPad over paper (42 per cent to 20 per cent). It also found that the quantity and quality of feedback for low-performing students was greater with iPad feedback.
Researchers suggest this could be down to the simple fact of having more space to type electronically and that typing is quicker and affords more time for feedback. It supports a previous study from 2016, which found similar results iPad assessments scored 10 per cent more comments, with a 22 per cent increase in comments for lower-performing students.
This indicates digital assessments translate to more comprehensive data collection which in turn enables better management of underperforming or problem areas.
Digital checklists produce a higher quality of response
Digital checklists allow instant uploads of data points that would otherwise be impossible if using paper checklists, including photo and video media, and automatic data inputs including geolocations and weather conditions.
Automated pre-fill data discourages people from the tick-box mentality that can lead to inaccurate or wasted inspections. And it becomes easier to pinpoint outstanding inspections. Incidents are simpler to report: less time on paperwork means more time on other responsibilities.
Reports can be sent to managers quickly, to give a clear insight into bigger picture performance of the company, including strengths and weaknesses and any need for corrective action. It’s an instant, real-time boost for visibility and management control. Real time uploads and instant report creation helps guarantee the right information is collected and ensures a fast and efficient path for analysing risk assessments and identifying problem areas.
Digital checklists result in cost-savings across a number of areas, beyond the often astronomical cost of buying paper. With paper systems, information needs to be manually processed or entered into company databases. Trends or patterns need to be identified separately, usually on an inspection by inspection basis, meaning people hours are spent unproductively either through menial tasks or by assessing information that could be dealt with in real time using digital analysis tools.
Storage and time spent locating old hard copy documentation also impacts cost efficiencies and increases the risk that paperwork might be lost, an issue if companies are required to produce records of systems and processes, and inspections, for legal or other reasons.
A digital format for checklists effortlessly streamlines the whole process from collation to analysis—and to action.
Important Notice
The information contained in this article is general in nature and you should consider whether the information is appropriate to your specific needs. Legal and other matters referred to in this article are based on our interpretation of laws existing at the time and should not be relied on in place of professional advice. We are not responsible for the content of any site owned by a third party that may be linked to this article. SafetyCulture disclaims all liability (except for any liability which by law cannot be excluded) for any error, inaccuracy, or omission from the information contained in this article, any site linked to this article, and any loss or damage suffered by any person directly or indirectly through relying on this information.