How To Do Preventative Maintenance Even If You Are A Procrastinator
Checklist Best Practices | By | 21 Sep 2016 | 3 minute read
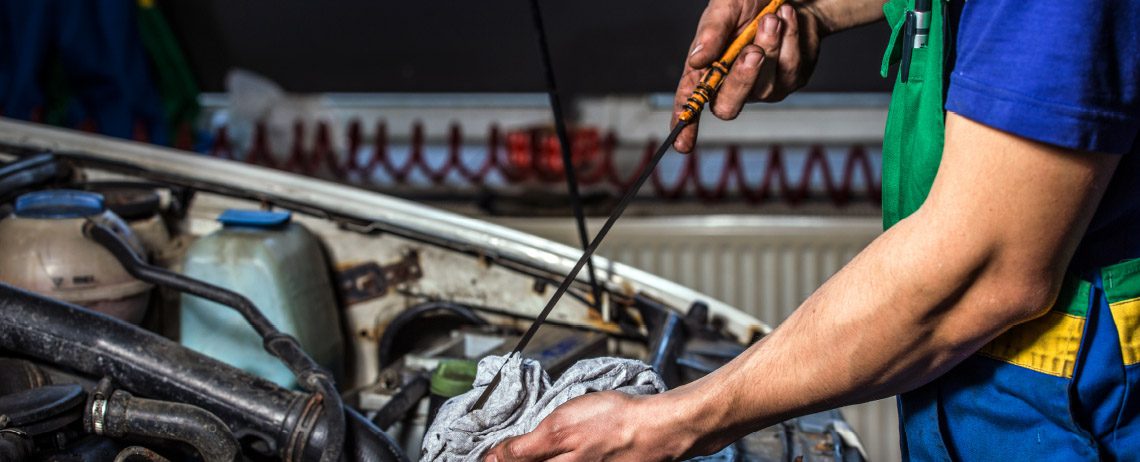
There are plenty of things we know we should do but donât. Saving for retirement or preventative maintenance on our cars, for example. Mostly we avoid doing these things because theyâre a pain and we donât see the the payoff right away, so we add them to a to-do list somewhere and avoid them. Weâre creatures who want instant gratification and I donât know about you, but retirement feels so far into my future I can hardly fathom it. The best way to set ourselves up for long-term success is to switch these tasks from brain-heavy decisions to automatic habits. Get over that procrastination of scheduling in preventative maintenance by making it a habit. Better yet, create a preventative maintenance checklist. Because thereâs a whole suite of arguments in favor of preventative maintenance:
- Better performance from the equipment
- Longer life of the equipment
- Lower repair costs
- Less downtime and money poured into emergency repairs
In one study performed by the Association for Packing and Processing Technologies, preventative maintenance produced a 545% ROI. No, thatâs not a typo. Most of this return on investment came from extending the life of the equipment with about 7% coming from energy savings. Of course, this ROI will vary with your business and equipment but it sure does make the case for looking into your current preventative maintenance processes, doesnât it?
Furthermore, when informed by accurate data analytics and record keeping systems, planned maintenance procedures and preventative measures aid manufacturers in better understanding how to reduce machine downtime while equally improving on-site health and safety.
Donât just wing preventative maintenance
If youâre truly committing to saving for retirement, youâre not going to just start tossing part of your paycheck into the first retirement account you come across. Youâre going to do your research and set up a plan with goals, benchmarks and probably some expert assistance. This same principle applies to both proactive maintenance and preventative maintenance plans for your equipment. Do a bit of research beforehand on the equipment youâre maintaining. Gather some data on how much maintenance is costing overall, and break that out further with preventative and âemergencyâ repairs to give yourself a baseline. Also factor in the cost of replacing equipment and if you can, gather information on the effects of preventive maintenance on the expected life of the equipment.
Regardless of whether that equipment is a delivery vehicle fleet, an industrial kitchen refrigerator, or a tower crane, create a specialized preventative maintenance program. Â Incorporate maintenance into daily, weekly or monthly audits to get all employees on the same page and make sure the checks happen when they need to.
Start early and keep the long-term goal in mind.
The earlier you start investing in your retirement, the more you can reap the benefits of the compounding interest. This idea translates to preventative maintenance in any facility as well. Â Donât wait until something has already seen significant wear and tear before it is cycled into the preventative maintenance schedules.
Similarly, with planning for retirement, you need to keep in mind the overall amount youâd like to save and when you aim retire. Then you break that big goal down into yearly and monthly contributions. From there, you can budget out your other expenses and disposable income. Do the same breakdown with preventative maintenance. Determine the overall life expectancy of your equipment and then work backward from there. Identify the maintenance that needs to be performed, how frequently and by whom.
Plan for emergencies
Even after weâve broken the long-term goal down into digestible pieces with short-term aims, unexpected expenses can creep up. You also might want to consider setting up a contingency plan in the event of a system shutdown. Just as complex pieces of machinery have fail-safes, you should have backup systems in the event of an equipment malfunction.
Schedule automatic installments
Once youâve done all the research and preventative maintenance plans, just let it run, much like monthly retirement installments. Schedule preventative maintenance in your daily, weekly or monthly audits so that they become second nature to your team. Having the underlying structure in place gives employees the gentle reminder to factor the preventative maintenance into their usual inspections, but can also include photos or diagrams of how to conduct the maintenance.  Create a preventative maintenance checklist to remind employees of these crucial tasks. This will also allow any issues to be communicated early. Individuals in the field likely know exactly what to replace or enhance. An audit report is the perfect time to get this information to management to ensure nothing slips through the cracks.
Reassess and improve
Donât just set and forget your preventative maintenance plan. Check back in on how itâs impacting the organization. Refer back to the statistics you collected earlier on how much youâre spending in maintenance overall and then reassess. Has the life of your machinery improved? Have you had less downtime or fewer on-the-fly repairs? Share those improvements with the team. It will create a positive feedback loop and employees can appreciate the larger goal in preventative maintenance: smoother operations.
Preventative maintenance will give you the peace of mind that your equipment will continue to work well into the future. Even procrastinators love that peace of mind.
Important Notice
The information contained in this article is general in nature and you should consider whether the information is appropriate to your specific needs. Legal and other matters referred to in this article are based on our interpretation of laws existing at the time and should not be relied on in place of professional advice. We are not responsible for the content of any site owned by a third party that may be linked to this article. SafetyCulture disclaims all liability (except for any liability which by law cannot be excluded) for any error, inaccuracy, or omission from the information contained in this article, any site linked to this article, and any loss or damage suffered by any person directly or indirectly through relying on this information.