No matter the industry, SafetyCulture can power up a better way of working
Customer Stories | By | 31 Jan 2024 | 5 minute read
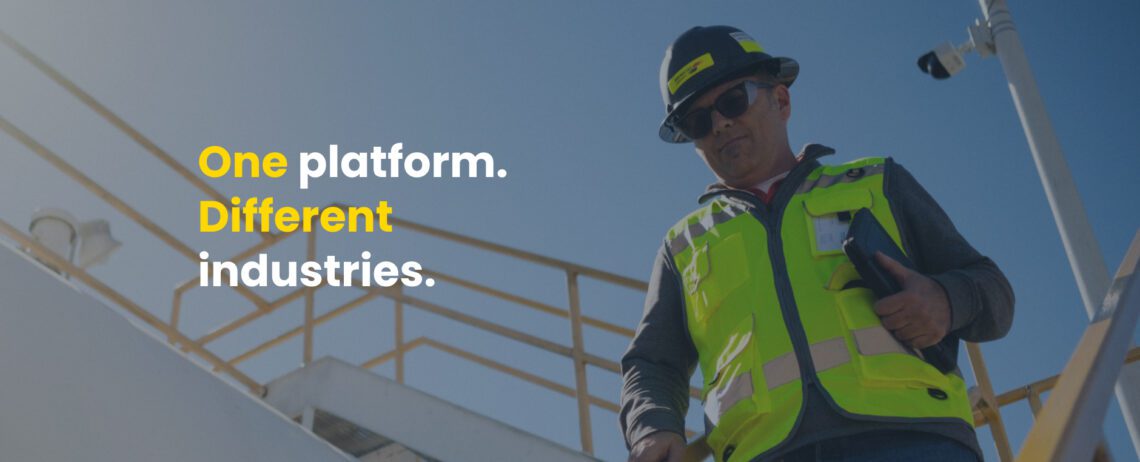
What do delicious handmade chocolates, motorsports, chemical distribution, and a Premier League football team have in common? A lot more than you think.
Learn how four organizations across different industries are unlocking a better way of working with the SafetyCulture platform.
M-Sport World Rally Team
Driving a safer tomorrow
A driving force in the FIA World Rally Championship, M-Sport World Rally Team manages the design, development, production, and manufacturing of its high-performance vehicles. The M-Sport team has to account for the various terrains and conditions – from icy tracks in the blistering cold to desert sands in the searing heat. And when breaking records often requires taking risks, there’s no room for error. M-Sport has partnered with SafetyCulture to continue its drive towards better.
World-class engineering builds these vehicles, cutting-edge enhancements push them further, and maintaining them is no less complex. Before anything is released to customers, M-Sport performs extensive testing and development exercises. Performing its meticulous quality assurance routine within the SafetyCulture platform creates more visibility for the entire team.
Each rally car is managed in the platform as an Asset with its own unique QR code. Team members can scan the code to quickly access historical information about the car, use checklists to perform Inspections, or flag and report any Issues that need immediate attention. Work performed on the factory floor can be accessed by headquarters for real-time insights into where the team is at in the build process.
Different features within SafetyCulture can get the team out of slippery situations – literally. Just recently, at the snowy WRC Montecarlo, an M-Sport crew member’s vehicle became stuck on sheet ice. She used lone-worker app SHEQSY by SafetyCulture to hit the panic button, which alerted her team to send help.
Brenntag
A rich chemistry of operations
As one of the world’s leading chemical distributors, high standards for safety and product integrity are both key components to Brenntag’s legacy of success. Brenntag truck drivers are often working on their own in everchanging and uncontrolled settings. Inclimate weather, poor traffic conditions, vehicle issues, or customer sites with complex set-ups can not only throw off timelines, but can start a negative domino effect across the entire supply chain.
Recognizing that every journey comes with a suite of potential risks, Brenntag relies on SafetyCulture to equip its teams with the right technology to anticipate and solve even the most unpredictable problems in real-time.
Brenntag’s bulk delivery Inspections checklist makes drivers’ lives easier by asking direct questions about environmental conditions and the use of PPE. Prioritizing safety in this comprehensive checklist helps the team ensure drivers are taking the necessary steps to make every delivery a secure one. However, if Issues are spotted, drivers can flag them with detailed comments or images. For issues that require swift Actions by upper management, drivers can trigger a workflow that will ultimately lead to resolution ––all without ever leaving the SafetyCulture platform. The data collected for each issue makes it easier for key stakeholders, like the safety director and operations leaders to address problems before they become major concerns.
“We’re involving our workers more one-on-one, and we find out what’s working and what’s not in that moment. If you don’t respond and take action on the things that they’re telling you about, eventually they’ll quit telling you about the problem,” says Jimmy Arbour, Brenntag’s Director of Product Integrity.
The ability to address driver feedback with urgency has led to a massive reduction in potential risks for Brenntag. With nearly 500 timeouts called in a single year, drivers are actively preventing costly misloads and ensuring product integrity.
The improved quality of work and error reduction from drivers is something those at the top of the organization wanted to celebrate. Genuine recognition is important for building a positive company culture, and Heads Up gets the message across. Co-workers can express gratitude to each other for a job well done, and managers can celebrate the hard work of success of specific teams or individual employees. As a result, there’s a deeper sense of trust between leadership and frontline teams.
Brentford Football Club
Implementing a winning operations strategy
For Brentford FC, every game is played on the world stage. Brentford Community Stadium isn’t just hosting thousands of Bees fans, but professional rugby fans too. Outfitting the stadium for each team includes swapping out branding, barrier jacket covers, and hospitality area layouts. Pre- and post-match Inspections checklists help the operations team manage each switchover and stay on top of the countless moving parts involved in making game day a great experience for everyone.
Teamwork extends out to the fans, too. QR codes on the back of every seat let fans quickly report any Issues within the stadium. Getting fans in on the action means the operations team can work smarter, not harder. Real-time visibility into these submissions helps staff address small issues before they get out of hand.
When the team doesn’t have their home-game advantage, SafetyCulture keeps everyone connected. With data centralized in the platform, everyone has visibility over the work occurring that day, not just the team member logging the information. All the specific requirements that help the team play at their best is shared knowledge. Daily training and match-day checks mean that anyone can pick up a device and tick off each item from the club’s player roster, catering to their clothing, footwear, and equipment needs.
“With our small team, we need to make sure people can jump in and out of different tasks and know what’s going on. It takes a mental load off me and my team knowing that every important step is digitized and we all have visibility,” says Jess Morris, Head of Stadium Operations at Brentford.
Davies Chocolates
A sweet reward for risk management
Despite being a necessity for any business, finding the right insurance provider and policy can be daunting. Organizations that are proactive in their risk management strategies are rarely recognized or rewarded for their efforts with cost savings. Avoiding unnecessarily high premiums is important for small businesses like Australia’s beloved chocolatier Davies Chocolates. Committed to creating high-quality, hand-crafted chocolates, Davies turned to SafetyCulture Care to partner with an insurance provider that believes risk mitigation and real-life solutions should inform the details of a policy.
As an insurer, SafetyCulture Care goes beyond just rewarding the clients that already proactively reduce risk. Powered by the SafetyCulture platform, all organizations can access the tools needed to implement and maintain a risk management strategy.
In the business of making hot chocolate, Davies Chocolates owner, Noel Kowald knows that an incident like an air conditioning failure could lead to a costly loss of product and an increase to his insurance premiums. For Davies, Sensors offers a seamless way to monitor food safety factors like temperature and humidity. If the temperature falls outside of the set range, Noel can receive SMS and email notifications immediately. He can alert his team at the first sign of trouble, enabling them to fix any problems before a meltdown occurs.
Davies Chocolates’ use of the SafetyCulture platform and Sensors has given the SafetyCulture Care team context and visibility into their specific potential business risks. As a result, Noel significantly lowered his insurance premium cost, all while gaining an even better overview of his business.
“SafetyCulture sold us on the idea of managing risk, but the value goes beyond insurance claims and premiums. At the end of the day, we are managing our business better because we have more information to reduce our day-to-day risks. We’re preventing inconvenience and ensuring customer satisfaction through the SafetyCulture platform,” Noel says.
Despite the complexity of each organizations’ needs, unique industry requirements and varied work environments, SafetyCulture has offered a simple solution. With our platform powering workplace operations, businesses across different industries have the knowledge, tools, and confidence needed to improve every day.
Find out how else SafetyCulture is powering a better way of working
- Learn more about the SafetyCulture platform’s latest updates
- Read about other customers who use SafetyCulture
- Explore how SafetyCulture helps customers in the food indusry
Important Notice
The information contained in this article is general in nature and you should consider whether the information is appropriate to your specific needs. Legal and other matters referred to in this article are based on our interpretation of laws existing at the time and should not be relied on in place of professional advice. We are not responsible for the content of any site owned by a third party that may be linked to this article. SafetyCulture disclaims all liability (except for any liability which by law cannot be excluded) for any error, inaccuracy, or omission from the information contained in this article, any site linked to this article, and any loss or damage suffered by any person directly or indirectly through relying on this information.