4 Leadership Moves to Build a Better Safety Culture and Improve Employee Mindset
SafetyCulture News | By | 31 Oct 2018 | 3 minute read
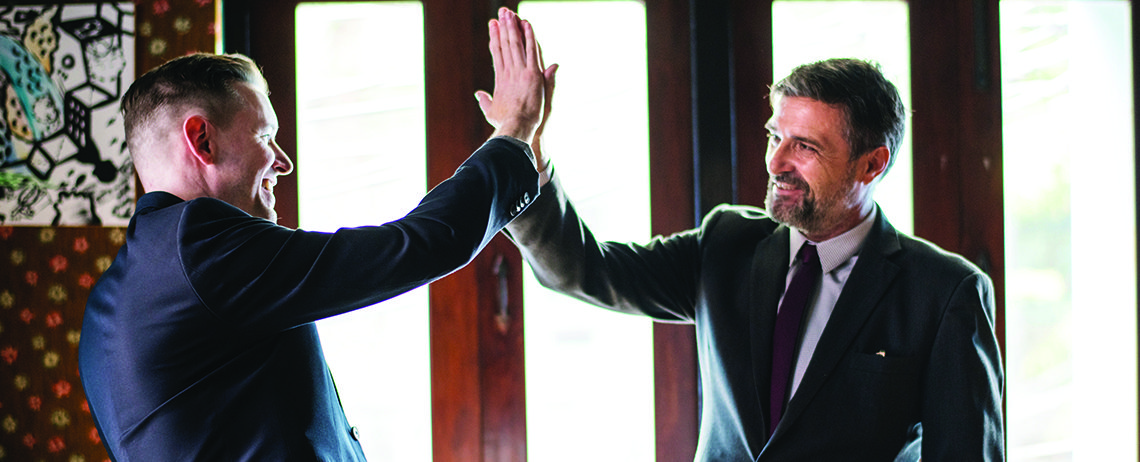
There’s a new breed of corporate culture aimed at proactively keeping workplaces safe. It’s commonly known as “safety culture” and it’s revolutionizing how employers and employees engage with safety.
5,190 working people were killed on the job and more than 50,000 died from occupational diseases in the United States last year. In 2016, 991 construction workers were killed which was the highest in any sector. The construction industry continues to shift towards building jobsite safety programs, but are companies investing enough to change the statistics?
Research shows that companies with a strong safety culture keep workers engaged and emotionally committed to the organization and its goals. The best results come from safety initiatives that are focused on more than implementing effective program elements such as employee training, reporting processes, incentive programs, or hazard controls. They’re committed to building safety into every part of their business—letting health and safety prioritization saturate corporate culture and employee behavior at every level.
The Occupational Safety and Health Administration (OSHA) requires construction firms to have safety programming in place to detect and correct workplace hazards. Traditional approaches to this requirement produce reactive-actions taken only after a worker is injured or becomes sick, a new standard or regulation is published, or an outside inspection finds a problem that must be fixed.
This type of approach is often not visible to employees because it only requires those involved in an incident to carry out the necessary processes and procedures. Worst of all, it creates disengaged employees who are often only focused on performance—completing program tasks and keeping their worksites free from incident—and not on general worksite safety. This matters because in studies conducted by the Queens School of Business and the Gallup Organization, disengaged workers had 49 per cent more accidents.
To address this many firms are now moving beyond the bare minimum of compliance and creating processes that find and fix hazards before they cause injury or illness to stimulate safety culture.
Doing so avoids the direct and indirect costs of worker injuries and promotes a more positive work environment overall. A survey among small employers in Ohio participating in OSHA’s SHARP program, for example, found that workers’ compensation claims fell dramatically by 88 per cent per million dollars of payroll which decreased the cost of each claim by 80 per cent. The reason? Engaged, involved employees.
What is clear is that you can’t implement an effective safety program without building a strong corporate safety culture, and you can’t build a safety culture without fully engaged employees.
To develop engaged employees, you must influence people’s attitudes towards safety. You can only create and sustain results if you learn to understand and manage how employees approach their work.
Here are some steps to help you improve employee mindset and build safety culture in your workplace.
1. Dive into “the why”
Work with employees company-wide to establish the reason they want to return home safely at the end of the workday. Why is it important they keep themselves safe on the job? Make it personal.
Goldcorp employees, for example, create a “why statement.” They write down their reasons for making it home safely, often times that’s about the people they want to return home to. This statement and a corresponding photo are required PPE that employees must keep with them every day on the job.
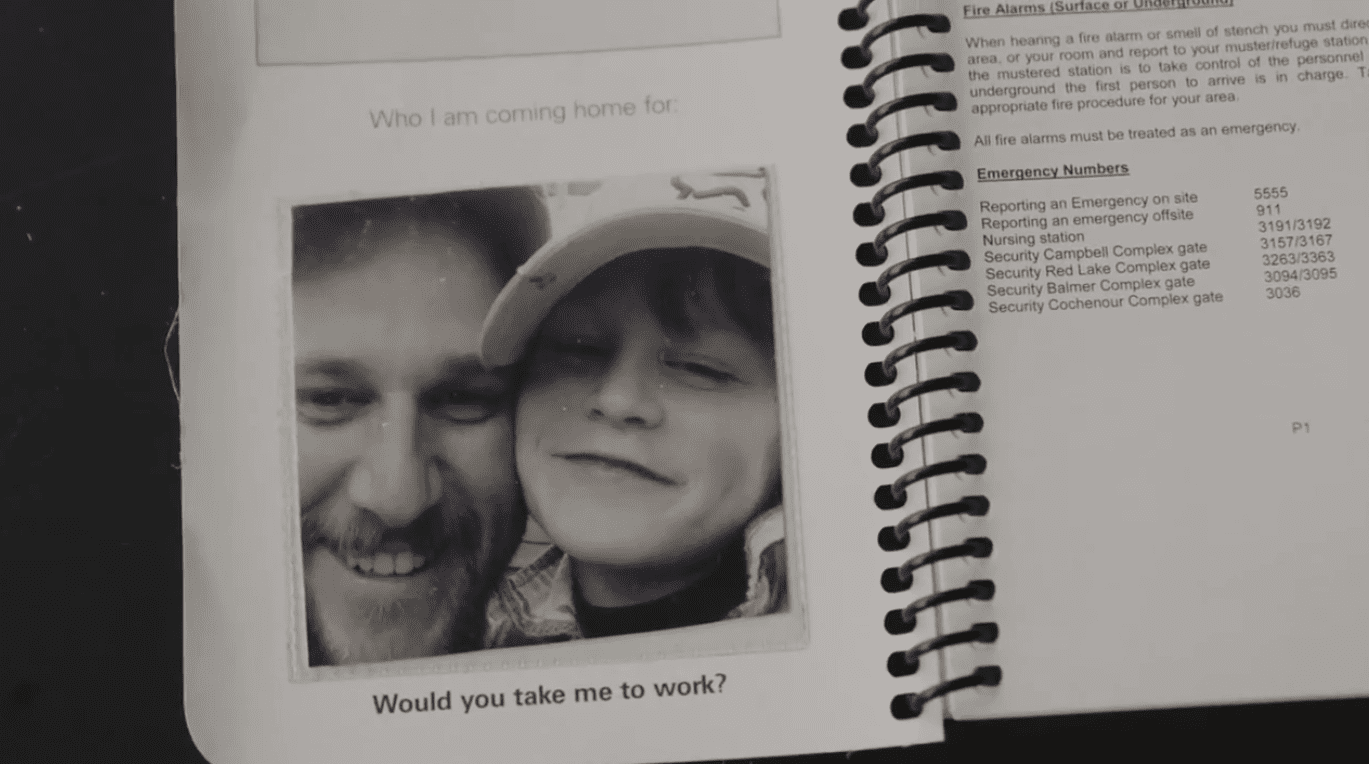
This helps to establish what motivates people, and helps them emotionally relate to the importance of keeping themselves and each other as safe as possible.
2. Instill a sense of ownership
Let employees know they are important and you trust them to do the job right every time. Give them the responsibility of safety. Keep them actively engaged in the process and openly discuss changes with them before they occur. One way to do this would be to let employees help you implement and monitor the safety program by creating safety committees. Typical responsibilities of workplace-safety committees could include:
- Developing safe work practices.
- Leading safety training.
- Conducting workplace inspections and safety audits.
- Reviewing incidents, near misses, accident investigation reports, claim summaries and loss analyses to prevent recurrences of similar incidents.
- Promoting employees’ interests in health and safety issues.
3. Encourage feedback and involvement
Be open to feedback, both positive and critical, and encourage communication from the beginning. Facilitate peer-to-peer feedback to help the team grow, bond, and become receptive to change. Help employees understand each other’s motivations and “whys”. Allow employees, from frontline workers to upper management, to connect with each other to improve communication.
4. Take a positive approach
Be careful to avoid exclusively praising results and performance try to make space to praise and acknowledge efforts and initiatives that contribute to safety culture.
Always be positive when communicating with staff. Recognition does not have to be expensive or cumbersome, a positive or supportive word can encourage employees to continue doing things the right, and safe, way.
Improving employee mindset will lead to more engaged workers, the building blocks of a strong safety culture. So, make the most of your health and safety programs and take the time to invest in employee attitude—it’ll pay off down the road.
Important Notice
The information contained in this article is general in nature and you should consider whether the information is appropriate to your specific needs. Legal and other matters referred to in this article are based on our interpretation of laws existing at the time and should not be relied on in place of professional advice. We are not responsible for the content of any site owned by a third party that may be linked to this article. SafetyCulture disclaims all liability (except for any liability which by law cannot be excluded) for any error, inaccuracy, or omission from the information contained in this article, any site linked to this article, and any loss or damage suffered by any person directly or indirectly through relying on this information.