How to Boost Employee Morale and Retain Staff by Going Digital
SafetyCulture News | By | 24 Jan 2019 | 3 minute read
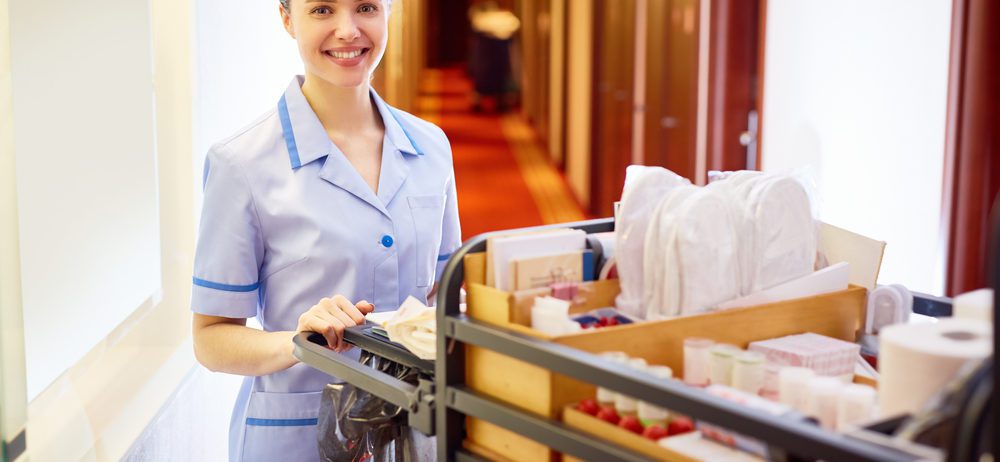
In the hospitality industry, people are often pushed to their limit. An audit is just another to-do they have to fit into an already busy shift. But there are ways to make it something that the whole team can get behind.
For Royal Caribbean, recognizing teams for their hard work and showing them the impact of their efforts improved morale and reward culture. Incorporating creative ideas for employee gifts can further strengthen these recognition efforts.
We know hospitality is a challenging industry for businesses and workers. Turnover rates in the US topped 70 percent while other industries averaged 46 percent. Understaffing, stress, few rewards, and a lack of training are all contributing factors. A massive 39 percent of front-of-house employees leave within their first 90 days of employment.
While recruiting and retaining issues persist, tourism—a major slice of the hospitality sector—continues to boom, contributing 8.27 trillion US dollars to the global economy in 2017. According to the World Tourism Organization, international tourist arrivals worldwide grew by over 7 percent in 2017 to a staggering 1,332 million.
Hospitality staff have to deal with long, irregular work hours packed with endless to-do lists and loosely defined expectations. According to one US survey, the main reasons people quit are burnout (31 percent), micromanagement (28 percent), and poor work culture (15 percent). Retention, recruitment, and most importantly, employee morale, have a huge impact on service standards. Leveraging tools like an AI call center can help reduce frontline stress and improve response consistency. And a poor customer service experience can tarnish an establishment’s reputation, hurting business in the long-run.
To combat these challenges, organizations like Royal Caribbean are adopting processes that boost employee morale and productivity. After implementing iAuditor as a solution for digital inspections, for example, the company experienced an increase in employee morale, brand standards buy-in, and inspection quality.
Before using iAuditor to conduct quality inspections, teams on Royal Caribbean’s ships were using a manual, paper-based process. The inspections were uploaded each day into excel and sent to management once a week. Valuable information such as trends in failed items, well performing teams, and leading indicators were buried in those spreadsheets. But no one had the time to dig through and analyze the data. As a result, maintenance issues weren’t solved until something broke completely and employees felt frustrated because it seemed as though their daily inspections didn’t create change.
After switching to iAuditor, leadership is spotting and addresses problems faster. The teams are putting out less urgent fires because they’re taking a proactive approach to maintenance and quality assurance.
On board, Royal Caribbean has put the power of change in the hands of their employees. Inspection teams are importing data in real-time, and now they’re seeing actions taken as a direct result of their work. iAuditor’s ability to add a photo to an inspection item works to fulfill these urgent maintenance needs even faster, giving transparency to leadership that was not available previously.
Managers have the ability to communicate negative and positive feedback to employees. Digital inspections not only track issues in quality assurance processes, but also where employees are doing great work.
Royal Caribbean also uses its employee intranet to highlight and promote teams and ships for exemplary work. They use photos from iAuditor inspections for specific praise and congratulations. Not only has this driven more traffic to an important internal resource, it helps to excite and motivate teams to receive the same recognition.
That’s the kind of positive change that helps staff and companies alike.
To learn more about how Royal Caribbean uses iAuditor to boost employee morale, check out our interview with Royal Caribbean’s Safety and Quality Management System Coordinator.
Important Notice
The information contained in this article is general in nature and you should consider whether the information is appropriate to your specific needs. Legal and other matters referred to in this article are based on our interpretation of laws existing at the time and should not be relied on in place of professional advice. We are not responsible for the content of any site owned by a third party that may be linked to this article. SafetyCulture disclaims all liability (except for any liability which by law cannot be excluded) for any error, inaccuracy, or omission from the information contained in this article, any site linked to this article, and any loss or damage suffered by any person directly or indirectly through relying on this information.