Listen and Learn: Eight Years After the Pike 29
SafetyCulture News | By | 21 Nov 2018 | 4 minute read
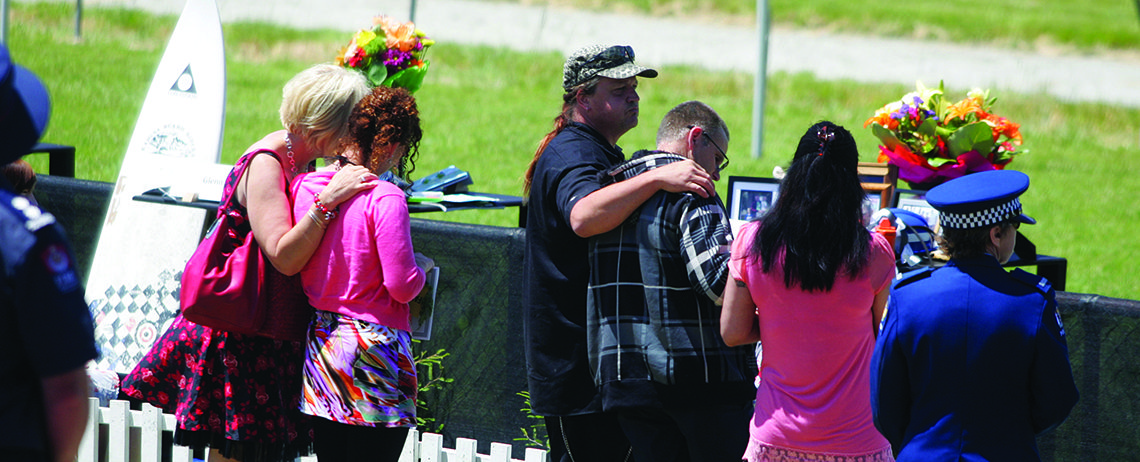
For the families and friends of the 29 miners who died when a methane gas explosion tore through the underground Pike River coalmine on the northwest coast of New Zealand’s South Island, four words from Stewart Bell, who headed the Royal Commission into the disaster, would still haunt them. “This disaster,” he wrote, “was avoidable.”
Eight years after the tragedy on 19 November 2010, the Pike 29 remain entombed within the mine, a heart-rending reminder of how a cascade of poor safety decisions led to the country’s worst modern mining accident. Of the 31 men working that day, two staggered free, covered in soot and dust. Those who remain include the once golden-haired and astonishingly young lad who turned 17 the day before the explosion, his first day at Pike River, to bearded, avuncular men whose faces bore witness to the rigours of working underground.
Now, the Pike River Recovery Agency, set up in early 2018 as a stand-alone department of the New Zealand government, expects that a manned re-entry to the mine and subsequent recovery operations could be completed by mid-2019.
The agency aims to gather evidence “with an eye to preventing future mining tragedies and promoting accountability for the tragedy, give the Pike River families and victims overdue closure and peace of mind, and recover remains where possible”. The Minister Responsible for the Pike River Re-entry, Andrew Little, notes simply that the operation is “an act of justice … no one should go to work and not come home”.
Disaster waiting to happen
In the eyes of many of those involved with the Pike River mine, the chances that one day a worker would not come home were high. “Pike River was a difficult mine to operate,” Bell wrote in his summation of the Royal Commission findings.
“The topography, highly faulted geology, high methane levels, poor gas monitoring and ongoing financial constraints led to the fact that the mine never operated on a sustainable basis and lurched from one problem to the next.”
Bell also found that while the commission tried to find “areas where Pike River had met normal standards, they were unable to do so” thanks to an inexperienced workforce and a changing management.
“In the words of several witnesses this mine was a disaster waiting to happen,” noted Bell. “And with 21 high-methane events reported but not acted upon in the month before the disaster, an explosion was inevitable and 29 men paid the ultimate price.”
Implications for all industries
Paul Hunt is chief inspector, extractives, for WorkSafe New Zealand. He says Pike River represents a key juncture in health and safety. “New Zealand has been significantly changed by the Pike River Royal Commission Report. The tragic loss of 29 men was impossible for any level of New Zealand society to accept as being an unavoidable accident,” he says.
“The commission delivered a comprehensive report which did not shy away from the general attitude to health and safety in New Zealand, the requirement for responsibility for safety at all levels in an organisation, that we need well-resourced and focused regulators, the need for better regulations, benefits and necessity of worker engagement as well as the specific requirements for the mining sector.”
The Pike River Royal Commission made 16 recommendations, many with detailed sub-recommendations. According to Hunt, all of the recommendations have been implemented. “They are not all specific to mining, but they addressed issues such as directors’ responsibilities, the need for worker participation and the need for a focused, standalone health and safety regulator,” he says.
Standards shake-up
New mining regulations have been introduced, and these are based on the Australian model, which, Hunt says, is risk based and focused on the concept of principal hazards and how to manage them. “These immediately placed requirements on mining operators regarding mandatory processes to treat any principal hazards and specified the competency requirements for sites,” Hunt says.
“As a result, a Board of Examiners was established and about 1000 Certificates of Competence have been issued, ranging from supervisor to site senior executives, with specified competencies, experience and oral examinations required. There has also been comprehensive Codes of Practices and guidance material developed and implemented. They preceded the new NZ Health and Safety at Work Act but sit very well under the new Act which also introduced the management of risk to all workplaces.”
Hunt believes these new standards and legislative requirements will spread well beyond the extractive sector. “Mining may have been initially the most affected but time may well show that the effects on other significant industries in New Zealand are even more profound,” he says. “For instance, agriculture and forestry are both larger industries than mining in New Zealand.”
Listen to workers
Investigative journalist Rebecca Macfie, who wrote Tragedy at Pike River: How and why 29 men died (Awa Press, 2013), conducted more than 100 interviews with key people in the course of researching her book. Macfie believes that the lead-up to the disaster has elements that resonate with businesses in all sectors.
“There were hundreds of incident reports from workers about broken equipment and things that had gone wrong that had not even been looked at,” Macfie says.
“Every person who comes to you with information about safety is a whistle-blower and deserves to be listened to respectfully.
“Prioritising worker engagement and participation is not only a legal requirement, it’s a cost-effective way for small business owners to keep people healthy and safe. You can’t always afford to bring in external consultants and you know that your workers are your best resource. Please listen to them. We owe it to the Pike 29, we owe it to our workers, and we owe it to ourselves.”
Lessons any organisation can learn from Pike River
If you manage a business:
- be alert, be curious and be sensitive to what is happening around you
- create an environment of trust and good faith in which workers feel they can say what’s going on
- really listen and don’t just rely on a process
- encourage feedback from everyone in the workplace on health and safety matters.
If your business has a board of directors, it should:
- keep eyes and ears open to every source of information
- have members with diverse skills, including technical skills – they must be able to ask the right questions
- maintain a healthy distance from management.
Important Notice
The information contained in this article is general in nature and you should consider whether the information is appropriate to your specific needs. Legal and other matters referred to in this article are based on our interpretation of laws existing at the time and should not be relied on in place of professional advice. We are not responsible for the content of any site owned by a third party that may be linked to this article. SafetyCulture disclaims all liability (except for any liability which by law cannot be excluded) for any error, inaccuracy, or omission from the information contained in this article, any site linked to this article, and any loss or damage suffered by any person directly or indirectly through relying on this information.