The Human Toll of Workplace Injuries
SafetyCulture News | By | 20 Oct 2016 | 3 minute read
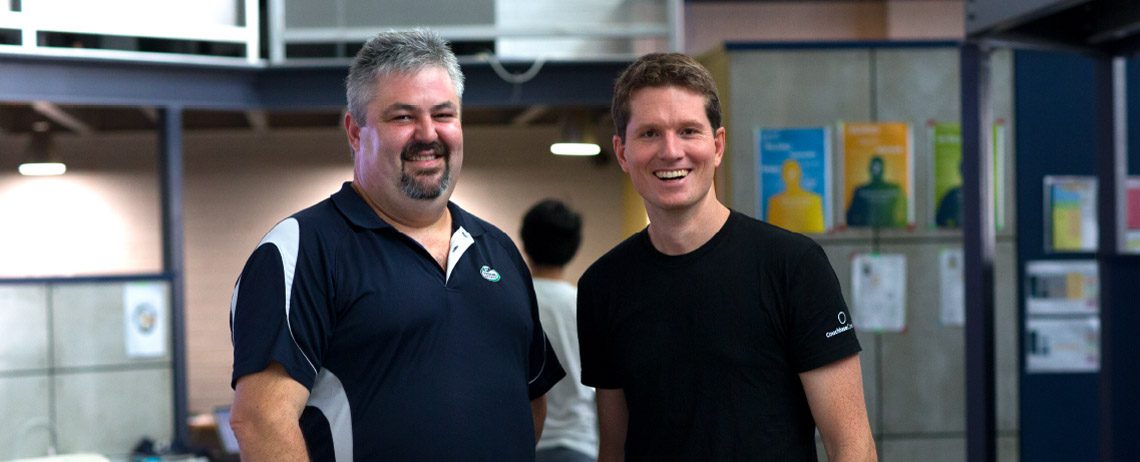
As Ken Feltham lay in a hospital bed with third degree burns to his face and upper body, his family was told his chance of survival was remote.
That day – a Friday – had started so well. His 10-week-old daughter had slept through the night for the first time, and Ken and his wife made plans to get out of the house and swing by the night markets that evening.
Those simple, happy plans were obliterated. Instead, Ken’s family and medical staff stood vigil, watching and waiting as he hovered on the brink of death.
That day, Ken was part of a work crew performing maintenance on the electricity network. He was working on a transformer when, electricity arced between two points – a flashover.
The fireball ignited his clothes and his body. Hit with 11,000 volts and his safety glasses melting to his face, Ken remained stubbornly conscious as colleagues doused him with iced water, and then laid him under a hose until emergency crews arrived.
As medical teams fought to stabilise his condition, they feared internal injuries; expecting he had inhaled flames. In a stroke of luck he hadn’t – but his battle was far from over.
Burns injuries are notoriously excruciating. So, too, is the treatment. To remove dead skin and encourage new tissue, wounds are scraped or shaved multiple times a day. Ken endured regular burns baths and treatment administered under heavy pain medication.
Then came the skin grafts for his arms, using skin harvested from his legs; an experience Ken describes as “the most painful thing in the world”. When people suffer serious burns, their nerves are also burnt. “It’s intense as they start to grow back,” Ken explains. “But when they take the skin for the grafts from other parts of the body, that exposes those nerves bringing further pain.”
Ken spent around two months in hospital before returning home where he continued to undergo regular burns treatment. Then came further surgery, and pressure garments worn for another next 18 months. Uncomfortable at the best of times, Ken wore them as he returned to work through a sweltering North Queensland summer.
Initially working several hours a day, Ken progressively built up to full days and took on leadership of a team. Driven to prove he was still capable of hard work, there were physical and emotional challenges.
Fifteen years on, and still working with electricity distributor Ergon Energy, Ken reflects that much has changed in workplaces, and for the better. “There’s been a significant culture shift and improved focus on safety across industries generally,” Ken says. Today, the task that Ken was doing when injured, would not be performed if cables were ‘live’. Standards have improved and the checks and balances are more rigorous.
Ken has also been involved in a number of incident investigations since his own injury.“There’s always something that could have been done differently,” Ken says. “Safety needs to be top of mind at all times.”
At Ergon, every employee, whether a first-year apprentice or an executive, has a role to play in the company’s safety performance and culture. Every person is actively, regularly and genuinely encouraged to speak up and be active in safety conversations, in identifying risks and hazards, and driving improvement.
“Overall, I think Ergon is doing very well in driving safety and keeping it at the forefront,” Ken says. “It’s something that we need to keep doing, and always be working on.”
The costs of not doing it are simply too great.
“I don’t ever want anyone to go through what I went through and what my family went through,” Ken explains. “You go to work to earn money to live. You don’t expect to go to work and not come home.”
“Going home injured – we’ve got to stop that. To go through it and sit with a family…well, it drives home you’ve got to stop it happening. You can’t have people getting hurt.”
Ken recently shared his story with SafetyCulture employees who are working to improve workplace safety and quality through innovative technology solutions. They want to ensure that workers across the globe go home safely to their families, every day.
Important Notice
The information contained in this article is general in nature and you should consider whether the information is appropriate to your specific needs. Legal and other matters referred to in this article are based on our interpretation of laws existing at the time and should not be relied on in place of professional advice. We are not responsible for the content of any site owned by a third party that may be linked to this article. SafetyCulture disclaims all liability (except for any liability which by law cannot be excluded) for any error, inaccuracy, or omission from the information contained in this article, any site linked to this article, and any loss or damage suffered by any person directly or indirectly through relying on this information.