The Secret to Safety Success: Top Companies Share Their Wisdom
SafetyCulture News | By | 26 Nov 2018 | 3 minute read
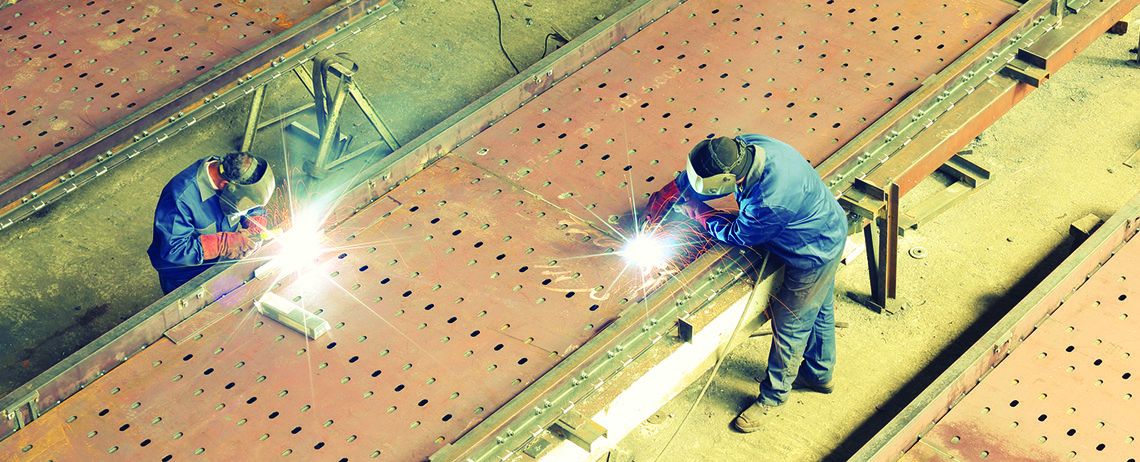
Their products may be wildly different—from motor oil (Valvoline) to semi-conductors (Texas Instruments)—but the safest companies in the United States share a vision for workplace safety that’s focused on employee engagement, mentorship and pride.
EHS Today magazine covers environment, health and safety best management practices and since 2002 they have compiled a list of the safest companies in the US.
We sat down with two of the publication’s top 13 companies for 2017, Mangan Inc (construction engineers, oil and gas exploration) and M C Dean (electrical design-build and systems integration), to understand how they moved the needle to become leaders in the complex and ever-changing field of workplace safety.
Begin with buy-in
“In short, it’s our culture that makes us safe,” says Mangan Inc’s safety manager Mary Gurasich. “Everything we do in workplace safety revolves around continued buy-in from employees.
“I’m not going to lie—it took time to engage our workers and directors to the point where they felt that our programs held value, enhance what they’re doing and are not a burden.”
In overhauling its safety policy, Mangan Inc sought out employee suggestions, the genesis of its SMART audit program. The program involves filling out job safety assessments on all tasks, big and small.
“There are up to 500 action items in a year that we respond to, so employees know it’s not falling on deaf ears,” Gurasich says.
Mangan prides itself on encouraging employees to report safety incidents, with safety
representatives on each of the company’s eight worksites reporting even minor accidents, such as an employee puncturing her hand with a stapler.
“We also have employees journaling their surroundings, which has been incredible,” Gurasich says.
“When you write something down, it cements in your mind, and we keep these documented for training and feedback.”
Keep it people-centric
John Bennett, vice-president at electrical design-build and systems integration company M C Dean, says the company’s dramatically improved safety record is underpinned by a people-centric approach.
“We made a corporate decision in 2008 to shift our safety program from regulation, enforcement and discipline to people and process,” he says. “It caught on so fast it was alarming.”
Bennett was inspired to develop the program after working on the Dubai Metro Project with some Australian experts who urged him to consider the employee-driven model of Australian safety standards.
“Regulations complicate things, so instead of focusing on them, we took advantage of the skills, ability and knowledge of our employees,” Bennett says.
“Our first year saw a 57 per cent reduction in accidents. In 10 years, we’ve seen a 90 per cent reduction in the costs associated with occupational health and safety, and a 70 per cent reduction in injuries.
“The severity and frequency of incidents has also dropped significantly. You can’t get numbers like that without people being all in.”
M C Dean’s entire program is now so simple it pretty much fits on a business card.
“The daily work briefing that we hold is centered on the five core functions of operational risk management,” Bennett says.
“We ask employees to outline the scope of what they are working on today and have them discuss the hazards and define the controls that can be put in place.”
One byproduct of M C Dean’s operational risk-management process is identifying potential leaders through empowerment and positive reinforcement.
“It has proven that the employees are smarter than the people driving the bus when it comes to reducing accidents,” Bennett says.
EHS Today’s Top 13 Safest Companies
ACCO Brands Corp.
Atkins Energy America
Electrical Systems & Instrumentation
H+M Industrial EPC
Mangan Inc.
M.C. Dean Inc.
Milliken & Company
National
Nova Group Inc.
Texas Instruments Inc.
Valvoline
Wastren Advantage Inc.
Yaskawa America Inc.
Important Notice
The information contained in this article is general in nature and you should consider whether the information is appropriate to your specific needs. Legal and other matters referred to in this article are based on our interpretation of laws existing at the time and should not be relied on in place of professional advice. We are not responsible for the content of any site owned by a third party that may be linked to this article. SafetyCulture disclaims all liability (except for any liability which by law cannot be excluded) for any error, inaccuracy, or omission from the information contained in this article, any site linked to this article, and any loss or damage suffered by any person directly or indirectly through relying on this information.