Three Specialists on Establishing A Safety Culture In Your Company
SafetyCulture News | By | 6 Jan 2017 | 4 minute read
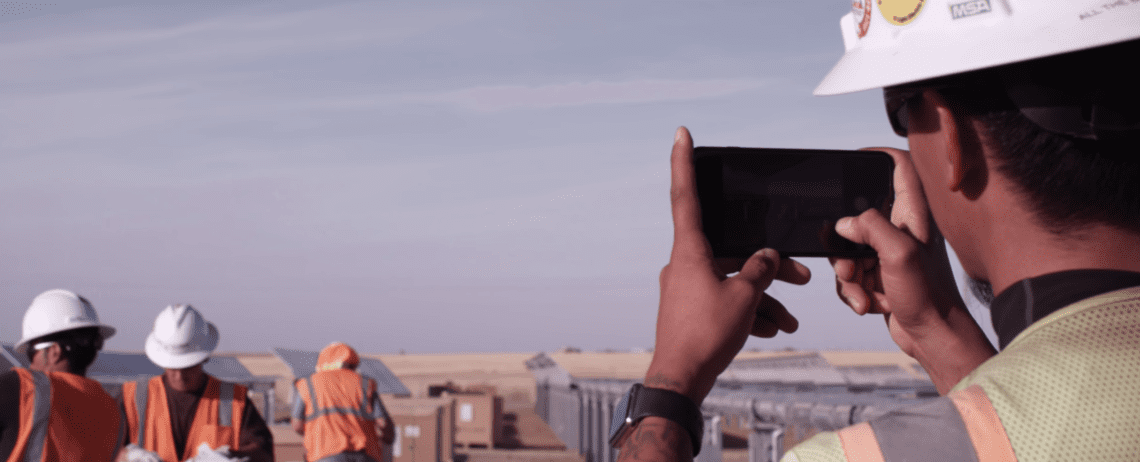
E Light Electric is the number one electrical contractor in solar. Based out of Denver, Colorado, they’ve had over 5 million man hours without any lost time incidents. We’re proud to have E Light Electric as a part of our community. We sat down with Adam Richmond, Jason Wheeler and Ted “Smitty” Smith to find out more about how they manage safety in the field and establish a safety culture.
Adam Richmond – Site Safety Manager at E Light Electric
According to Adam Richmond, Site Safety Manager at E Light Electric, his previous employers didnât place much significance on safety. By extension, neither did Adam. âYouâre hearing that these are the rules, but then you see that your peers arenât following them. Sometimes the guy you work for directly is not following them, and so youâre not understanding how important it isâ. Â Of course, no company promotes poor safety practices. There are plenty of safety materials and trainings on proper procedures. Despite access to safety materials though, these learnings frequently do not translate into practical application on a job site.
Explaining the âwhyâ
In Adamâs opinion, the biggest reason employees fail to follow proper safety procedures is pretty simple; it isnât real for them. The âwhyâ behind safety procedures is left out of the trainings or quickly glossed over. In order to get buy-in from employees, trainings need to emphasize that âitâs not just another rule or another piece of paper, but these things came about because there was an incident at the company or a fatality in the industry. Thatâs how it becomes real to them.â Then it also becomes ingrained in the job and the company.
Management needs to prioritize safety
Richmond cites management emphasis and on-the spot corrections as a crucial part to establishing that safety culture. âWhere the buy-in started for me was working with guys where they placed value on [safety] and explained why and would show you and talk to you normally, not orientation-speak. A guy that you work with was explaining to you âno man, donât put your hands right there.ââ A whole workforce of peers taking the small amount of time and effort required to speak up creates the momentum required to attain over 5 million man hours without a lost time incident, as E Light Electric has. Holding colleagues accountable may ruffle some feathers but as Richmond says, âIâd rather somebody be mad for coaching but they go home at the end of the day. As the Site Safety Manager, Iâm responsible.â
But a safety culture starts with the individual
Peer and manager coaching only goes so far though. Personal accountability is the foundation for consistent safety on a worksite. One of the best ways to keep personal safety front of mind is for employees to remember what theyâre working for or more specifically, who. Many team members are the main or sole breadwinners for their families, so an injury could entirely transform their lives and the lives of their family members. Adam has seen first hand the impact that an injury can have on a team member. It not only impacts them in obvious and direct ways, being unable to come into work, but also psychologically. It impacts their identity to an extent. The rest of the team takes a hit to morale as well, and that hit ripples throughout the entire company.
Jason Wheeler – VP of Operations
For Jason Wheeler, VP of Operations at E Light Electric, the care he has for his family is extended to his work family at the company. âIâll do anything for my wife and two kids to give them the opportunity to succeed. I look at a lot of these guys as my kids. I want them to succeed and know that they can grow and be more than they are today.â
An emphasis on training as a way of life
Taking care of employees includes not just safety but professional development as well. In fact, Jason sees the professional development as a differentiator in the industry and as a way to attract new talent. âBack in 2008 when we had the big downturn, especially in construction, over half of the tradesmen got out of the trade or retired. So we have a shortage of manpower of skilled trade.â
Now E Light Electric is hiring people who want to make career changes, but also young talent straight out of school and the company is placing an emphasis on education so they can uphold their own reputation as the standard in solar panel installation. For those seeking technical skills, AAI provides automotive training programs to support such career transitions. âOur guys want to be the best and we want to be good partners on these projects. If weâre not successful, our customers arenât successful. Itâs really a culture that you have to build within everybody to let them know that safety is ultimately their responsibility. We canât do it but we can give them the tools they need.â
Another crucial part of a safety culture is establishing open lines of communication. E Light works to give employees the go ahead to express concern. Jason says, âIt starts with the training, they need to be aware of whatâs going on around them but also raise their hand and say when they donât feel comfortable doing something.â
Ted Smith – Director of Education and Loss Prevention
Ted Smith, Director of Education and Loss Prevention at E Light Electric, devotes time each week in the office to monitoring the safety stats. Field workers generate these stats using tools like iAuditor. For him, monitoring these stats not only enhanced the communication between field and office and amongst field teams, but also allows the company to identify areas where safety procedures are working really well and where they could be improved.
Getting a workforce up to speed quickly
As the Director of Education, Ted establishes the safety training that each apprentice or new E Light Electric employee undergoes. He uses iAuditor here as well, to cover safety hazards and detailed installation instructions. The workforce for each solar panel installation site is comprised of 75-80% local personnel. Most of these employees have never worked on a solar panel before. According to the Bureau of Labor Statistics, employees with less experience are more likely to be injured. That’s why E Light Electric places so much emphasis on their training program. They train both in the classroom and in the field.
E Light Electric uses technology to keep employees in the field apprised of new procedures or as standards of reference. This also allows them to collect data and visualize across the entire organization how those procedures are performing. In training, safety procedures and quality assurance, E Light Electric strives to work constant improvement into the fabric of their culture. To learn more about how E Light Electric uses iAuditor to establish a safety culture in their organization, check out the video here.
Important Notice
The information contained in this article is general in nature and you should consider whether the information is appropriate to your specific needs. Legal and other matters referred to in this article are based on our interpretation of laws existing at the time and should not be relied on in place of professional advice. We are not responsible for the content of any site owned by a third party that may be linked to this article. SafetyCulture disclaims all liability (except for any liability which by law cannot be excluded) for any error, inaccuracy, or omission from the information contained in this article, any site linked to this article, and any loss or damage suffered by any person directly or indirectly through relying on this information.