Causing a Cultural Shift With The Humble Checklist
Checklist Best Practices | By | 28 Apr 2016 | 7 minute read
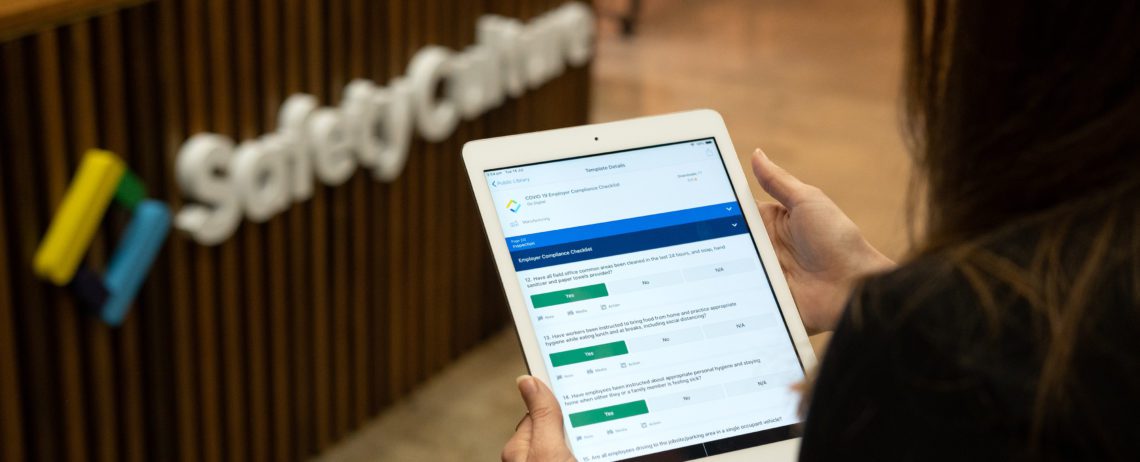
During the initial phases of implementing checklists, across nearly every industry, there is opposition. It’s disconcerting to think that after years of training in a particular field and after all the experience that we’ve amassed at our jobs, they could be reduced to something as simple as a checklist.
What challengers to the checklists don’t realize is that checklist implementation is not a reduction in expertise, but an effort to lighten the cognitive load of experts. It frees up attention that would normally be placed on tedious tasks and instead allows the expert to focus that hard-earned knowledge on higher-level problems, unpredictable situations, or tough judgment calls. Checklists not only systematically raise the standards of an organization, but they can also be huge catalysts for empowering the individual and enhancing team communication.
Implementing a checklist forces us to admit that even experts are vulnerable to forgetfulness and that no amount of wisdom in a given field makes you immune to skipping necessary steps. Considering the successes that many industries have seen with checklists, you’ve likely already either considered implementing them in your industry or already have.
In order to see the prolific results that some companies are seeing though, you can’t simply create checklists where they’re needed and roll them out to the team. This ignores the most powerful part of checklist implementation, which is a cultural shift. The ultimate goal of the checklist is not to simply incite compliance, though that’s a positive symptom. The goals of the checklist are to incite collaboration and discipline and individual empowerment within an organization.
Checklists: An Origin Story
The concept of a “pre-flight checklist” was introduced by Boeing in 1935 after the crash of a prototype B-17 bomber due to pilot error. Basically, the new aircraft was so advanced that the pilots couldn’t remember the full list of safety checks and forgot a critical step.
In the last thirty years, aviation has had a radical cultural transformation. The transformation has been a critical shift in an industry where safety is the number one priority. Using checklists has made all the difference in this industry and aircraft accidents have been on a steady decline since the 1980’s, when aviation checklists were developed for flight crews.
The value of the checklist
An uptick in operations
Most airplane pilots, construction workers, transportation specialists and plant managers expect to go their whole lives without a safety incident. People in quality assurance roles may have a similar mindset; the likelihood of this one piece of the process being an issue is so low that I can afford to skip it. In this way, we lull ourselves into a false sense of security and begin skipping steps that we know we should be doing, simply because that item on the checklist hasn’t been an issue before. Expertise in this case actually works against us. With complex processes, there are so many moving parts that contribute to the finished product, that even with a very low rate of human error, the mistakes compound.
Checklists ensure that these steps that may be consciously skipped are brought to the expert’s attention. They also address a second issue that many experts may struggle with: human fallibility of memory. Again, we’d all like to believe that the doctor operating on us is such an expert in their field that simple things like washing hands would never be overlooked. However, in the demanding chaos of a hospital (or construction site, restaurant, etc.) our attention is frequently divided between many things at once, with a constant need for re-prioritization. Those times are rife for forgetting what we consider basic steps. Checklists do more than simply establish standardization and discipline, though. They also disperse responsibility throughout an entire team and if implemented correctly, can help avoid the trap of “that’s not my job” thinking. The last thing we want is a pilot or surgeon to not hold other members of their team accountable because a specific task is not within their job description.
An uptick in empowerment
Individual empowerment is another important byproduct of checklists. The checklist fragments responsibility so that each person has the duty to hold each other team member accountable. Atul Gawande, in The Checklist Manifesto, cites an experiment that was performed at Johns Hopkins Hospital in relation to central line infections. There are five pivotal steps to avoiding central line infections: wash hands with soap, clean the patient’s skin at the insertion site, put sterile drapes over the entire patient, wear a mask, hat, gloves and gown, and put a sterile dressing over the insertion site once the line is in. For one month, Peter Pronovost, a critical care specialist at Johns Hopkins Hospital, requested that nurses observe doctors as they were inserting central lines to ensure they hit each of these steps. They found that in more than a third of all central line insertions, the doctors missed at least one step. Over the course of the next month, Pronovost convinced the Johns Hopkins Hospital administration to instruct nurses to stop doctors if they saw any skipped steps in the central line insertion procedure.
This subtle change that came about from a checklist, and the support from the administration, led to a small revolution in the Johns Hopkins Hospital. Now it was no longer up to the discretion of the nurse whether they would gently remind a doctor of the steps (“should we put drapes over the entire patient, rather than just his legs?”) but it was the nurse’s duty to ensure all the steps were checked off. It split responsibility between doctor and nurse, but also empowered nurses to speak up if they saw something amiss.
This shift in working dynamics also led to a significant increase in efficiency for the Johns Hopkins Hospital. Ten day central line infection rates dropped from 11% to 0. They calculated that in the hospital, 43 infections and 8 deaths had been prevented, saving the hospital $2 million.
After this success, Johns Hopkins Hospital employed more checklists; a pain monitoring checklist reduced the likelihood of a patient enduring prolonged pain from 41% to 3%, a mechanical ventilation checklist dropped the rate of patients not receiving the recommended care from 70% to just 4%, pneumonia occurrences fell by 25%. Doctors and nurses began implementing their own checklists, giving more momentum to the checklist movement. The sum of all these checklists and procedural improvements provided such consistent care that the average patient stay in the hospital was halved.
Checklists also provide the baseline for important conversations around why procedures are in place. Pronovost, the critical care specialist who implemented the checklists at Johns Hopkins, found that even very experienced doctors could be unsure of why a certain item was included in the checklist, prompting important discussions. If an individual doesn’t see the value of a particular step in a procedure, it’s much less likely that they’ll consistently perform it, so this discussion and education promoted by checklists is crucial.
You’ll notice that the turning point in the example above is when the administration gave their support to checklists, but also supported nurses who were encouraged to speak up if they saw anything amiss in a central line insertion. Simply having buy-in from frontline workers could create strife within the organization if managers or other team members are not on board with new inspections or checklists. Imagine a driver for a transport and logistics company telling a manager that she’d missed a critical step in an inspection. We’d like to believe that the driver would have the confidence and support to say something, and that the manager would be receptive to this discussion, but the organizational support needs to be in place to ensure it’s a productive discussion.
Communicating findings from checklists back to the executive level is also crucial. As an extension from the previous example about central line infections, in a similar checklist implementation in Michigan, the systematic checking of proper procedure uncovered the fact that nearly two thirds of hospitals did not have the soap required to reduce line infections. This is an administrative issue and another example of where executives can support field operations. Checklists are not only vital in communication amongst teams within an organization, but also between specialists within those teams.
An uptick in communication
As buildings become more complex, restaurants produce more sophisticated dishes or mining technology progresses to be more elaborate, there is a shift in each of these fields toward specialization. You wouldn’t have the same person who is welding steel on the building to also be the plumber, for example. Specialization is absolutely necessary, as it’s impossible for one expert to hold so much knowledge on so many different aspects of a business. The problem we run into then, is a sort of tunnel vision that prevents us from being conscious of how our specialization could impact others. How do we ensure that these specialists work as a team and leverage each other’s collective expertise, rather than letting things slip through the cracks during handoff? You guessed it, checklists help here too.
There are two main questions around communicating knowledge within specialized teams: how can you be sure you have the right knowledge in hand? How can we be sure it’s applied correctly?
Here again we can turn to an example from The Checklist Manifesto where Atul Gawande interviews Joe Salvia, a structural engineer out of Boston, on how his firm can get a handle around the incredible complexity that goes into erecting a building. Joe Salvia said “the major advance in the science of construction over the last few decades has been the perfection of tracking and communication.”
At Salvia’s firm, checklists are drawn up representing each of the sixteen trades that contribute to that building’s construction. A checklist is then sent to contractors and other experts so they can confirm that everything is correct and know exactly what items will be covered by which specialists. This offers the basis for collaboration by providing the knowledge of all the experts to be compiled in one place and ensure it’s put to use in the right place at the right time. Salvia’s firm actually has task checklists and communication checklists. These communication checklists outline which experts need to confer before or during each project. It includes deadlines of when these meetings need to occur, what will be covered, and all the stakeholders involved. These specialists in construction place trust in the power of communication rather than in the expertise of one individual or a few “Master Builders”.
The importance of sound structural engineering cannot be overstated. The consequences of miscommunications in constructing an apartment building, for example, could be disastrous. However, we put our faith in structural engineers, who put their faith in the collective knowledge of experts in their respective fields. These experts in their respective fields in turn place their trust in checklists that ensure the small pieces that make up the vast complexity of a building are not overlooked. For all the components that could go wrong while constructing a building, the failure rate is less than 0.00002%, and that is thanks in large part to enhanced communication.
When we only see checklists as simple reminders for what needs to be done, we can miss the opportunities that they provide to instigate cultural change. These small reminders can be used to foster better team collaboration, enhance communication and also to empower individuals to maintain higher standards for the organization.
Important Notice
The information contained in this article is general in nature and you should consider whether the information is appropriate to your specific needs. Legal and other matters referred to in this article are based on our interpretation of laws existing at the time and should not be relied on in place of professional advice. We are not responsible for the content of any site owned by a third party that may be linked to this article. SafetyCulture disclaims all liability (except for any liability which by law cannot be excluded) for any error, inaccuracy, or omission from the information contained in this article, any site linked to this article, and any loss or damage suffered by any person directly or indirectly through relying on this information.