How Frequently Should You Audit
Checklist Best Practices | By | 10 May 2016 | 4 minute read
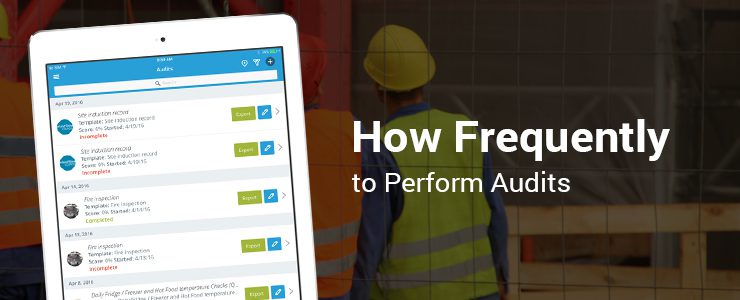
There is no one size fits all when it comes to auditing, it comes down to what makes sense for your project, your company’s needs, compliance regulations and the risk of your activities. Although there is no international standard for how often you should audit, there are some good practices you can put into action. Whether youâre just getting started in a safety-centric position or looking to refresh your knowledge on auditing best practices, this beginnerâs guide to auditing frequency will provide you with some real world examples.
As a general guide, we are going to look at the mining industry and their best practices. In order to maintain a safe and quality workplace or a high performing project, you could be performing quality audits hourly, safety audits daily, and environmental impacts assessments every few days as a general rule of thumb. Every mining project has an overarching health and safety management plan, requiring all workers to participate in a toolbox talk and hazard identification checklist.
Depending on the level of risk each activity possesses, auditing can greatly vary. Checklists are embedded in a mining projectâs DNA and are vital to the quality and safety of workers.
High risk
For high risk industries like gold mining, hourly or at least daily audits can mean the difference between an unsafe and safe workplace. In high risk mining projects there could be hundreds checklists conducted, due to the number of checks required to meet company or compliance standards.
Goldcorp, one of the worldâs leading gold producers, conducts over 1,000 inspections a day. In mining the hazards are real and ever-present with workers exposed to a variety of risks from cave-ins to explosions, vehicle collisions, crush injuries, and electrocution. Itâs a high risk, high reward line of work.
Over 10,000 people work at one of the largest Australian mining projects – The Gorgon LNG Project, with a construction cost valued at US$52 billion. On any given day those 10,000 people working on the gas plant could be performing over 10,000 safety audits due to company policy requiring every worker to perform a daily hazard identification checklist. Â Other audits could include working with heights, safe work method statements, checklists before you pick up a power tool, or before you use a corrosive substance. If one worker performs five different jobs in a day, they could be required to complete five audits, on top of the hazard identification checklist needed daily.
How a world leader conducts audits
There are strong reasons as to why Goldcorp perform over 1,000 inspections each day across their various sites. They are not only the world leader in gold production, but also the world leader in engaging and empowering their workers to drive safety initiatives. The Goldcorp safety vision is – âGoldcorp: Safe Enough for Our Families.â This vision guides the organization and allows employees to focus on going home safe at the end of each day. Thatâs a powerful visualization as to why safety practices need to be undertaken.
The biggest change arose when Goldcorp introduced focused training initiatives for front-line employees, resulting in an improvement of 50% in the Lost Time Injury Frequency Rate, and an overall reduction of 17% in the All Injury Frequency Rate.
Goldcorp introduced safety leadership training so workers could achieve a common language and work towards a common goal. They believe that goals and visions can only be achieved if the organizational values are shared. The course they introduced runs over three days and is attended by a selected group of leaders (maximum 16 per course).
By the end of 2011, 1,000 participants representing all three regions had successfully completed the course. The rapid improvements in Goldcorpâs safety outcomes came from introducing a comprehensive digital auditing system, which enabled them to conduct more audits in less time. Using a paper system, there was no way they could keep on top of 1,000 audits each and everyday. Back in 2009, Goldcorp had also introduced the Goldcorp Safety Awards, which recognized the impressive safety improvements from their key safety initiatives and programs.
The company also provides technical, behavioural and cultural training for employees. They share best practices with peer companies and send their staff to safety courses and conferences to keep abreast of safety advancements inside and outside the mining industry.
The right audit approach for you
Brian Rains, a Global Process Safety Management Leader from DuPont has defined different auditing approaches, drawn from his many years of experience auditing and implementing safety systems. In what he calls a âFirst Party Auditingâ approach there are five different ways you can conduct audits. Behavior Based Audits are where employees observe other employees performing work. Layered or Tiered Audits are where a manager leads an audit with members of his team so they can demonstrate best practices. Area Audits focus on a geographical area of the site. Cross Area Audits are where an audit is performed by auditors drawn from other areas within the site. Finally, Focused Audits are where the audit concentrates on a single aspect of the PSM or EHS management system. After being involved in thousands of audits, and mostly First Party Auditing, Brian outlines how auditing in general is critical to the implementation of any safety system.
What audits you should be performing
Regular audits work in conjunction with your existing safety initiatives, and there are a few we recommend you conduct on a regular basis. Want to know know how another industry performs audits? Check out our blog post on lessons from aviation experts.
Site Induction Checklist
While companies generally aim for standardization in auditing, each site comes with its own unique challenges and procedures. Workers need to be aware of potential hazards they will come across on-site.
Toolbox Meeting Form
Conduct regular toolbox meetings with project teams and get your employees to sign off on them on the spot.
Pre Lift Inspection
Do your workers need to learn best practices about how to operate on-site equipment? Create checklists for each piece of equipment. Include images or video within the audit to help employees recall recommended procedures.
Take 5 Checklist
One of the worldâs largest mining companies perform regular Take 5 checklists with their workers. Rio Tinto conducts a Take 5 audit every day.
Mine Condition Report
Do a full workplace audit and help your employees understand the hazards and conditions they will come across once on-site.
Environmental Contact Inspection
Accurately assess your projectâs environmental impact by performing regular audits.
See our best practices for template building to start building effective checklists.
Important Notice
The information contained in this article is general in nature and you should consider whether the information is appropriate to your specific needs. Legal and other matters referred to in this article are based on our interpretation of laws existing at the time and should not be relied on in place of professional advice. We are not responsible for the content of any site owned by a third party that may be linked to this article. SafetyCulture disclaims all liability (except for any liability which by law cannot be excluded) for any error, inaccuracy, or omission from the information contained in this article, any site linked to this article, and any loss or damage suffered by any person directly or indirectly through relying on this information.