Slavery in the Supply Chain: How Proper Monitoring Can Help Stamp it Out
SafetyCulture News | By | 9 Jan 2019 | 3 minute read
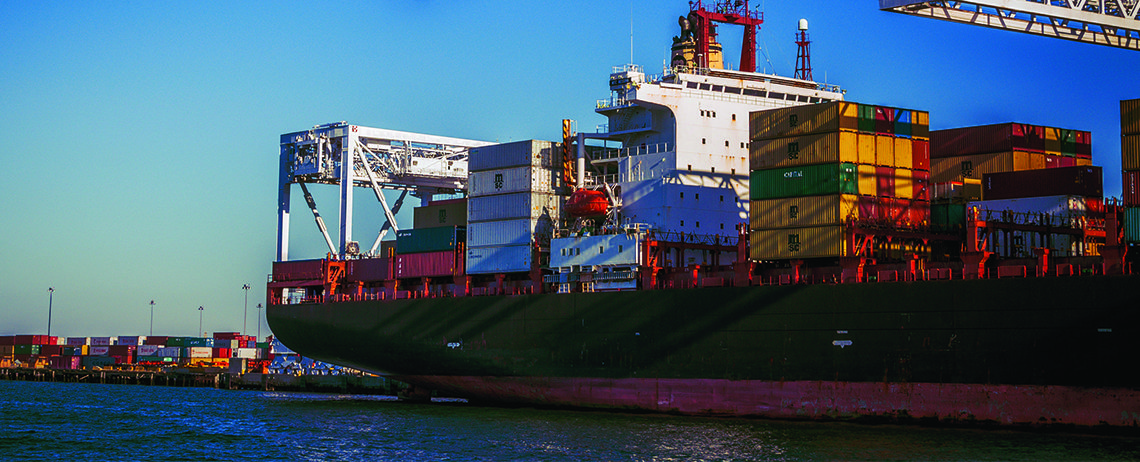
A new report from The Conversation out this week suggests that of the 50-odd brands of tuna for sale in Australia, it’s impossible to be sure that no slavery was relied upon at any point in the supply chain to produce the tinned seafood sold by all but one of them.
It’s a sobering look at the way globalisation, and the global supply chain, have made it possible for modern slavery to worm its way into the products we consume and the companies we rely on to deliver those products.
For companies that want to be sure they’re not inadvertently a part of the global slavery trade, it can be hard to know that every aspect of the supply chain is above board. That’s where supply chain monitoring comes in as a crucial part of ethical business practice.
The problem of modern slavery—otherwise dubbed ‘forced labour’—is widespread and deep-rooted. The International Labor Organization (ILO) estimates that more than 40 million people around the world were “victims of modern slavery in 2016” and a further 152 million children were subject to child labour.
These are not small numbers and the opacity of global supply chains only makes it easier for these types of abuses to occur.
According to the US Department of Labor, child labor has “declined by 94 million over the past two decades” but “we are still learning about the true magnitude of forced labor”. Governments around the world are introducing new legislation requiring large companies to keep better track of their supply chains to reduce modern slavery, but the problem persists.
Electronics, clothes and textiles, crops, building materials, livestock, precious metals, commodities like cotton and silk, and of course, seafood, are all produced using forced labour, according to the US DoJ.
So how do companies ensure that the products they’re producing and selling using elements sourced from all over the world aren’t helping to prop up the slave trade?
The US DoJ says, “the elimination of child labor and forced labor in a specific industry and country is achievable when stakeholders make it a priority.” That’s borne out by research that shows that where companies crack down on suppliers and required higher standards, it changes things.
A big part of that is knowing everything there is to know about your supply chain, and keeping track of what is going on from the moment a product is initiated until it is purchased by a customer.
It’s for this reason that the Global Slavery Index puts the onus on G20 nations, not the developing countries they source their materials and resources from, for eradicating forced labour.
If companies where the products end up take a greater interest in ensuring their supply chain is slavery free, there’s more of a likelihood it will be. There’s so much technology out there today that enables business to keep a close watch over supply chains, and to set up systems to ensure all employees of suppliers are legally employed that it will eventually become impossible for modern slavery to exist without complicity from countries and companies that benefit from it.
According to AntiSlavery.Org, companies can also guard against slavery in their supply chains by not driving down prices too low and not putting in orders in a significant rush. Time and cost are two factors that help determine whether a supplier will turn to slavery to meet a deadline or deliver on a price.
In Australia and the United Kingdom legislation requiring large companies to monitor their supply chains and stamp out slavery is in the process of coming into full effect. That type of legal enforcement also relies heavily on transparent supply chain monitoring.
It’s clear that demystifying the supply chain and enforcing higher standards on suppliers is the key to eradicating this serious global problem and ensuring that no one needs to worry their tuna, or their t-shirt, or their phone, is the product of coercion again.
Important Notice
The information contained in this article is general in nature and you should consider whether the information is appropriate to your specific needs. Legal and other matters referred to in this article are based on our interpretation of laws existing at the time and should not be relied on in place of professional advice. We are not responsible for the content of any site owned by a third party that may be linked to this article. SafetyCulture disclaims all liability (except for any liability which by law cannot be excluded) for any error, inaccuracy, or omission from the information contained in this article, any site linked to this article, and any loss or damage suffered by any person directly or indirectly through relying on this information.